内燃机齿轮检测的重要性
内燃机作为动力系统的核心部件,其齿轮组承担着传递动力、调节转速和扭矩的关键作用。齿轮的精度、强度及耐久性直接影响发动机的运行效率、噪音水平和整体寿命。在高转速、高负荷、交变应力的工作环境下,齿轮可能出现磨损、变形、裂纹或疲劳失效等问题。因此,通过系统化的齿轮检测项目,能够及时识别潜在缺陷,避免因齿轮失效导致的整机故障,同时为优化生产工艺提供数据支持。现代检测技术结合了材料科学、精密测量和数字化分析手段,形成了一套覆盖齿轮全生命周期的质量控制体系。
齿轮几何尺寸检测
几何精度是齿轮性能的基础,检测项目包括齿廓误差、齿向误差、齿距累积误差等关键参数。使用三坐标测量机(CMM)进行三维建模,结合齿轮专用检测仪测量渐开线形状、螺旋角、分度圆直径等指标。对于批量生产场景,会采用齿轮综合误差检测仪实现快速分选,确保齿轮副的啮合精度控制在ISO 1328或AGMA 2015标准范围内。
表面质量与缺陷检测
齿轮表面状态直接影响承载能力和疲劳寿命。检测内容包含:
1. 宏观缺陷:通过磁粉探伤或渗透探伤检测表面裂纹、折叠等缺陷
2. 微观形貌:使用表面粗糙度仪测量Ra、Rz值,评估加工质量
3. 接触斑点:通过红丹粉着色法检查啮合接触区域分布
4. 金相分析:借助电子显微镜观察表层组织结构,检测渗碳/氮化层深度
材料性能检测
齿轮材料需满足高强度、高韧性及耐磨性要求,主要检测项目包括:
- 化学成分分析(光谱仪)
- 拉伸试验测定抗拉强度、屈服强度
- 冲击试验评估材料韧性
- 硬度测试(洛氏/维氏硬度计)
- 残余应力检测(X射线衍射法)
热处理效果验证
热处理工艺直接影响齿轮的机械性能,需重点检测:
• 硬化层深度与梯度(显微硬度法)
• 心部硬度与表面硬度匹配性
• 金相组织中马氏体、残余奥氏体含量
• 畸变量测量(热处理前后尺寸对比)
动态性能测试
在模拟工况下评估齿轮实际表现:
- 动平衡测试:确保高速旋转时振动值符合ISO 1940标准
- 疲劳试验:在齿轮试验台上进行循环加载,检测点蚀、断齿等失效模式
- 噪声检测:通过声级计分析啮合噪音频谱特性
结语
内燃机齿轮检测是集精密测量、材料分析和动态测试于一体的系统工程。随着智能制造技术的发展,在线检测、数字孪生等新方法正逐步应用,推动检测效率与精度的双重提升。通过严格执行标准化检测流程,可显著提高齿轮可靠性,为内燃机的高效稳定运行提供坚实保障。
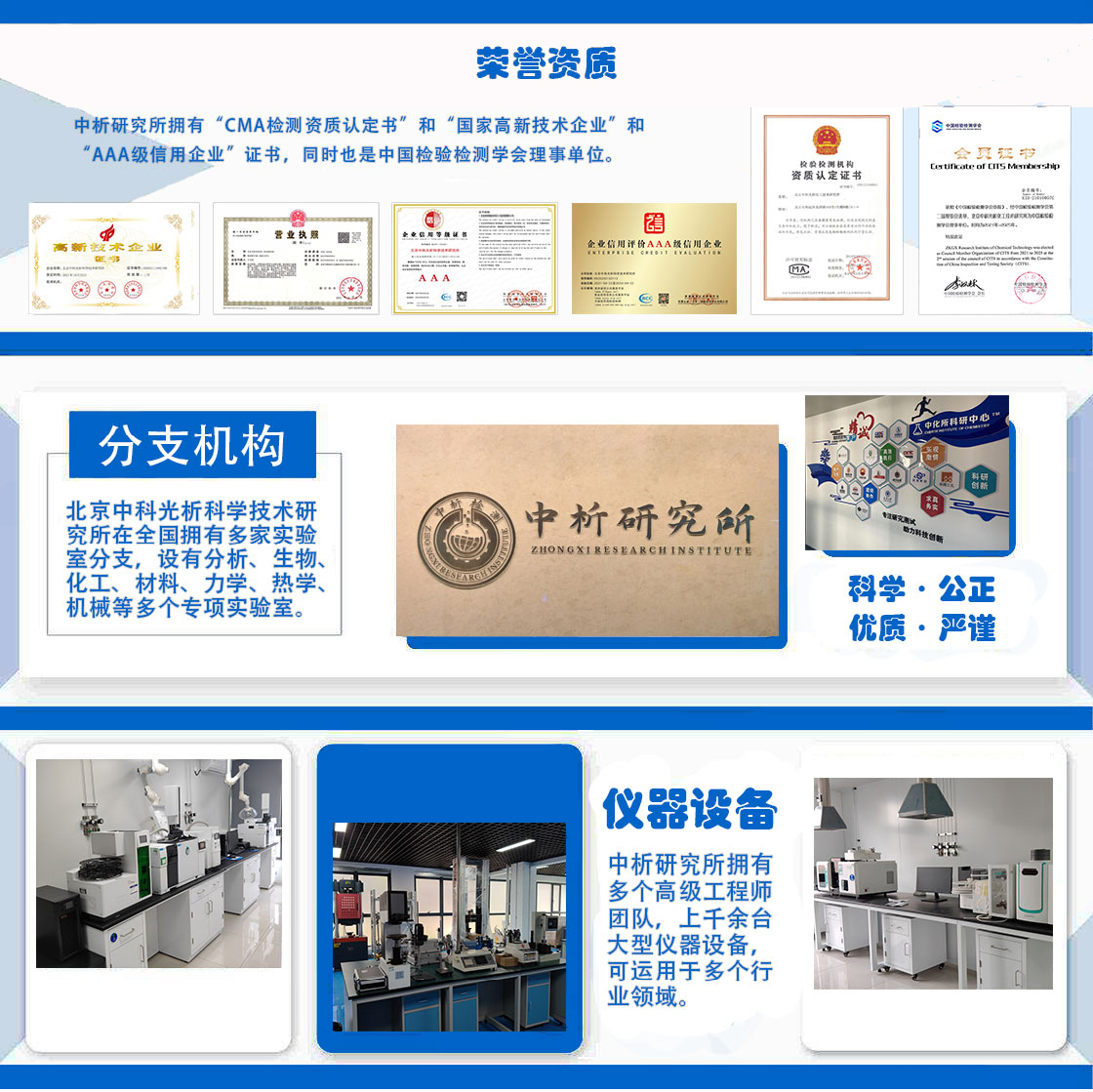
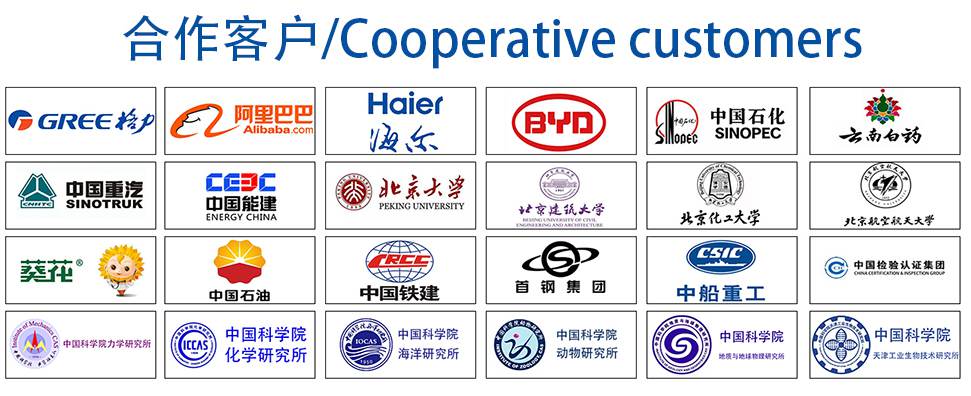