隔离阀密封检测的重要性及核心检测项目
隔离阀作为工业管道系统中控制介质流动的关键设备,其密封性能直接关系到生产安全、能源效率和环境保护。在石油化工、天然气输送、核能及制药等高危或高精度行业,隔离阀的密封失效可能导致泄漏、爆炸或环境污染等严重后果。因此,定期开展系统的密封检测是确保阀门长期可靠运行的必要手段。本文将围绕隔离阀密封检测的核心项目展开详细说明,为工程实践提供技术参考。
一、目视检查与尺寸验证
检测前需对阀门外观进行初步评估,包括密封面是否存在划痕、腐蚀或变形,阀座与阀瓣的配合间隙是否符合设计要求。使用卡尺、三坐标测量仪等工具验证关键尺寸公差,确保密封结构在安装后能够实现有效贴合。
二、泄漏率测试(气密性试验)
通过向阀门注入惰性气体(如氮气)或液体介质,模拟实际工况压力,利用流量计、气泡检测法或氦质谱仪等设备测定泄漏量。根据ISO 15848、API 598等标准,严苛工况下阀门泄漏率需低于10-6 mbar·L/s。核电站用阀门通常需满足ASME B16.34的零泄漏要求。
三、压力保持测试
在额定工作压力的1.1-1.5倍下进行保压试验,通过压力传感器持续监测30分钟内的压降情况。高压阀门(如Class 1500以上)需结合循环压力测试,验证密封结构在交变载荷下的稳定性,防止因材料疲劳导致的密封失效。
四、材料兼容性测试
针对不同介质(酸性、碱性、高温蒸汽等),评估密封材料(如PTFE、石墨、金属硬密封)的耐化学腐蚀性和热变形特性。通过加速老化试验模拟长期使用后的材料性能衰减,确保密封件在寿命周期内保持弹性模量和密封强度。
五、环境适应性检测
极端温度(-196℃至800℃)、振动、辐射等特殊环境下,需通过环境模拟舱测试密封性能。例如LNG低温阀门需验证深冷收缩后的密封面贴合度,核级阀门需检测辐照脆化对密封材料的影响。
六、动态密封性能评估
通过启闭循环试验(通常5000次以上)验证阀门在频繁操作下的密封耐久性,重点关注密封面磨损量、扭矩变化及泄漏率演变趋势。采用在线监测系统实时记录参数波动,为预测性维护提供数据支持。
值得注意的是,以上检测项目需根据阀门类型(闸阀、球阀、蝶阀等)、应用场景及行业标准进行组合优化。专业检测机构通常配备高精度氦检漏系统、红外热成像仪等设备,并结合数值模拟技术(如FEA流体分析)提升检测效率。通过系统化的密封检测,可有效降低阀门故障率,延长设备使用寿命,为工业装置的安全经济运行提供坚实保障。
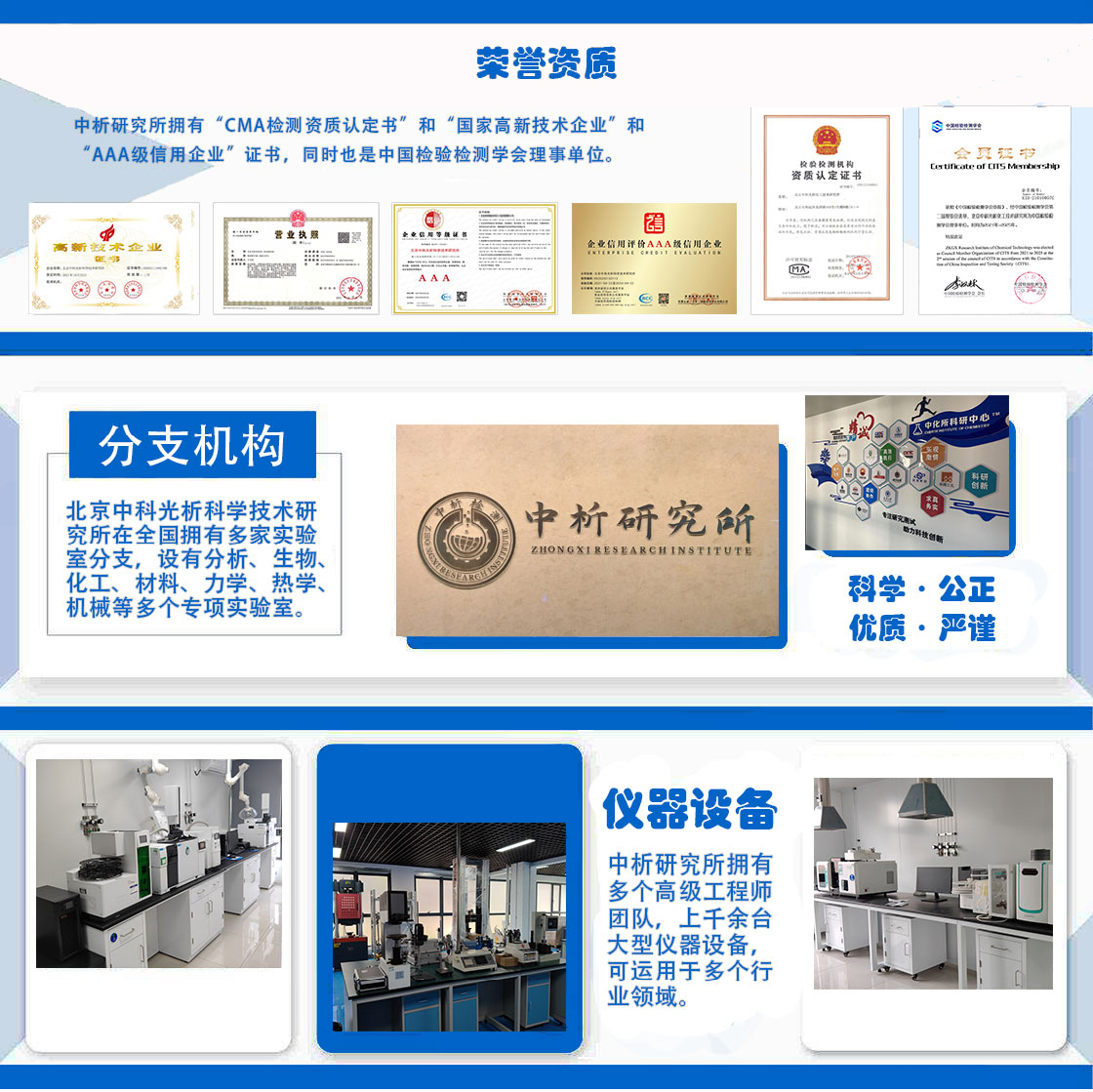
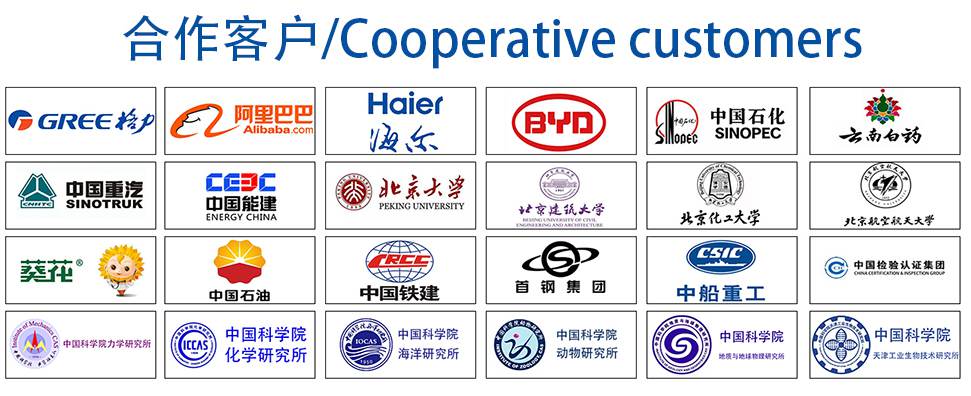