承压容器密封检测的重要性
承压容器作为工业领域中储存或运输气体、液体等介质的关键设备,其密封性能直接关系到生产安全与运行效率。这类容器广泛应用于石油化工、能源发电、医疗器械及航空航天等领域,若发生泄漏可能导致爆炸、环境污染或人员伤亡等严重后果。因此,密封检测是承压容器设计、制造、安装及定期维护中的核心环节,需通过系统化的检测项目验证其密封完整性,并确保其符合国家及行业标准(如ASME、GB/T 150等)。
承压容器密封检测的核心项目
1. 气密性测试
通过向容器内部充入压缩空气或惰性气体,利用压力表或电子传感器监测压力变化,判断是否存在微小泄漏。通常采用保压法或压降法,检测精度可达0.1%FS,适用于高压容器的初步筛查。
2. 液体渗透检测(PT)
在容器表面涂抹荧光或显色渗透剂,通过毛细作用渗入缺陷部位,再经显像剂处理以可视化裂纹、孔隙等密封失效点。此方法对焊缝、法兰连接处等关键部位具有高灵敏度。
3. 氦质谱检漏
利用氦气作为示踪气体,通过质谱仪检测极微量的氦泄漏,灵敏度可达10⁻⁹ Pa·m³/s级别。适用于核工业、半导体设备等对密封性要求极高的特殊场景。
4. 超声波检测(UT)
采用高频声波扫描容器壁厚及焊接区域,通过反射信号分析材料内部缺陷(如夹渣、未熔合等)。可量化裂纹深度并定位隐蔽泄漏源,尤其适用于高温或厚壁容器。
5. 密封元件性能评估
对垫片、O型圈、阀门等密封部件的压缩回弹率、耐温性及抗腐蚀能力进行实验室测试,确保其在设计寿命周期内维持有效密封。需结合ASTM D1414等标准进行老化模拟实验。
6. 压力循环试验
模拟容器实际工况下的压力波动,进行多次升压-降压循环,验证结构疲劳强度与密封系统的稳定性。试验压力通常为设计压力的1.25-1.5倍,持续周期依据行业规范确定。
检测技术选择与标准执行
检测方案的制定需综合考虑容器材质、介质特性、设计压力及使用环境。例如,腐蚀性介质容器需增加定期壁厚监测,而低温容器则需关注材料冷脆性。严格执行NB/T 47013等检测标准,结合数字化检测系统(如智能压力记录仪)可提升数据追溯性与分析效率。
结语
承压容器的密封检测是贯穿其全生命周期的重要安全保障措施。通过多维度检测项目的组合实施,不仅能及时发现潜在风险,还可为容器的优化设计和维护策略提供数据支持。企业需建立完善的检测管理体系,并委托具备特种设备检验资质的专业机构执行检测,以确保结果的法律有效性与技术可靠性。
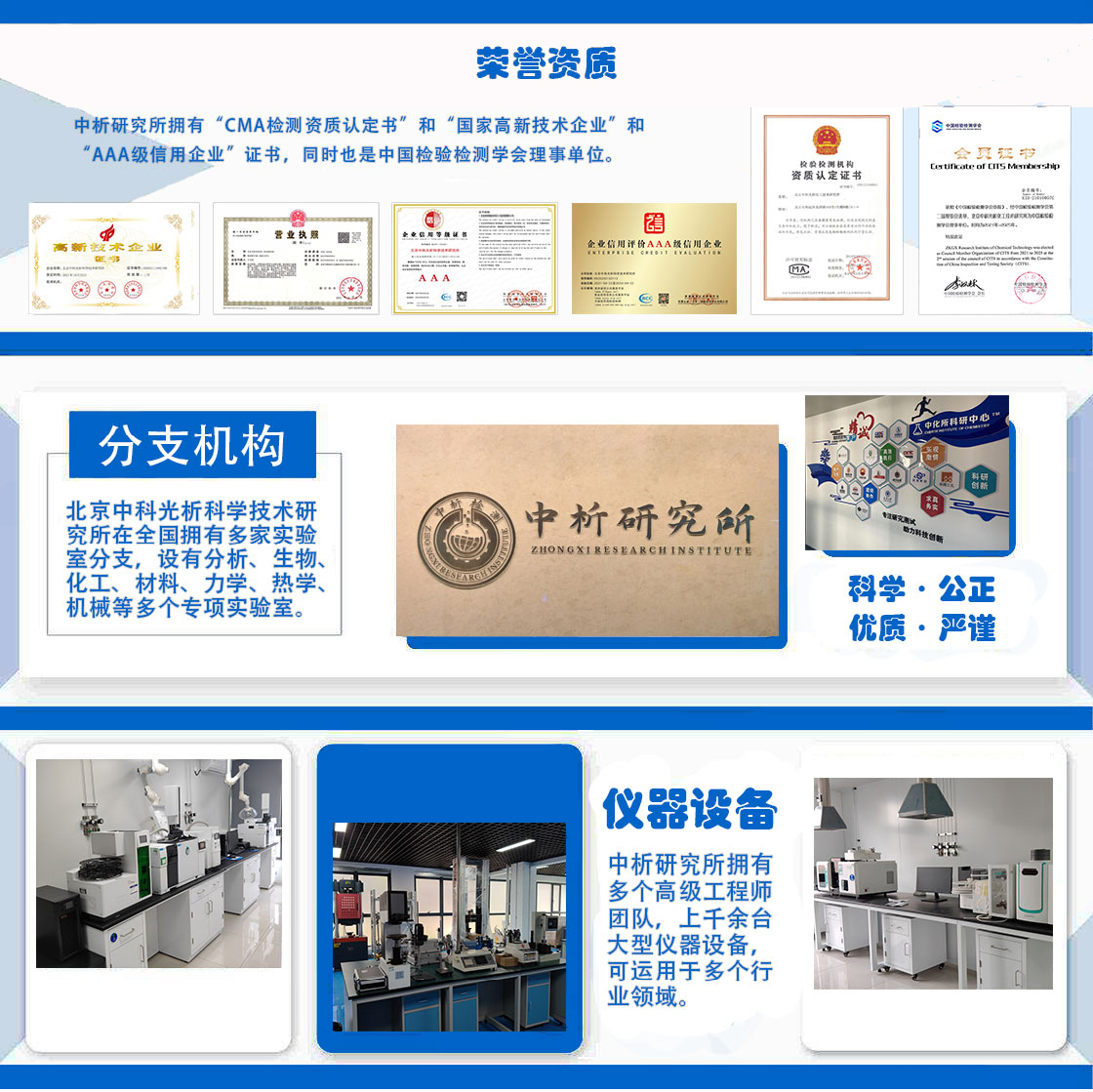
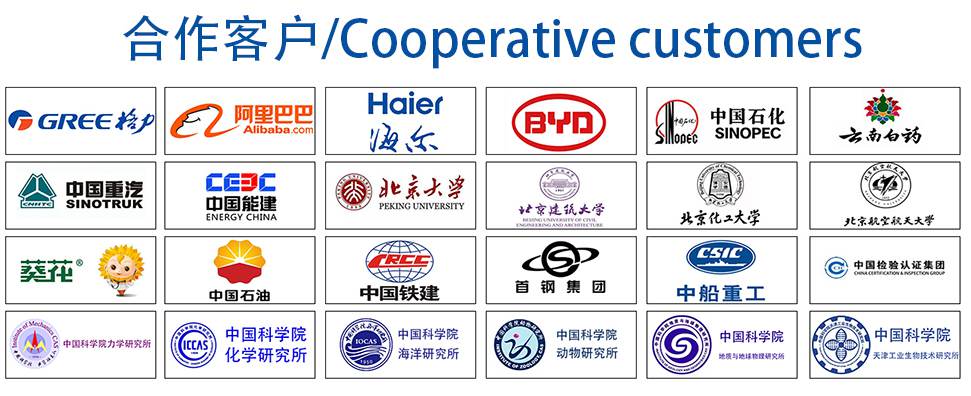