铝及铝合金挤压型材检测的重要性
铝及铝合金挤压型材因其轻量化、耐腐蚀、高强度及易加工等特性,被广泛应用于建筑、交通、航空航天、电子设备等领域。随着行业对材料性能要求的不断提高,确保型材质量成为生产和使用环节的关键。挤压型材在生产过程中可能因工艺参数、原材料纯度或设备条件等因素出现缺陷,如成分偏差、力学性能不足、表面瑕疵等。因此,通过科学的检测手段对型材进行全面质量评估,不仅能保障产品可靠性,还能优化生产工艺,降低安全隐患。
检测工作贯穿原材料采购、生产过程控制及成品验收全流程,需结合国家标准(如GB/T 5237、GB/T 6892)和行业规范(如ASTM B221、EN 755),从化学成分、力学性能、尺寸公差到表面质量等多个维度展开。精准的检测数据为产品认证、质量追溯及技术改进提供重要依据,是提升企业市场竞争力的核心环节。
核心检测项目及技术要求
1. 化学成分分析
通过光谱分析仪(如直读光谱仪)检测铝及铝合金中主要元素(铝、镁、硅等)和杂质元素(铁、铜、锌等)的含量,确保符合牌号标准(如6063、6061)。杂质超标可能导致材料脆性增加或耐蚀性下降。
2. 力学性能测试
包括抗拉强度、屈服强度、延伸率和硬度测试。以万能试验机进行拉伸试验,验证型材的承载能力和延展性。例如,建筑用6063-T5型材的抗拉强度需≥160MPa,延伸率≥8%。
3. 尺寸与形位公差检测
使用三坐标测量仪、卡尺、角度规等工具,测量型材的截面尺寸、直线度、平面度及角度偏差。根据GB/T 14846标准,壁厚公差通常控制在±0.2mm以内,弯曲度不超过0.3mm/m。
4. 表面质量检验
目视检查或借助显微镜观察型材表面是否存在裂纹、气泡、划痕、氧化膜不均匀等问题。阳极氧化型材需额外检测膜厚(如AA15级要求膜厚≥15μm)和色差,盐雾试验可评估耐腐蚀性能。
5. 金相组织分析
通过金相显微镜观察晶粒度、第二相分布及是否有过烧组织。挤压工艺不当可能导致晶粒粗大,影响材料韧性和疲劳强度。
检测方法与设备选择
现代检测技术结合了传统仪器与数字化手段。例如,超声波探伤仪可检测内部缺陷;X射线荧光光谱仪(XRF)用于快速成分筛查;而扫描电镜(SEM)则能深入分析断口形貌。企业需根据产品用途及检测成本,合理选择实验室检测或在线监测方案。
质量控制与标准化管理
建立完整的检测体系需涵盖人员培训、设备校准、数据记录和报告审核。企业应定期参与行业比对试验,确保检测结果的可比性和准确性。同时,结合ISO 9001质量管理体系,将检测流程嵌入生产各环节,实现全生命周期质量管控。
结语
铝及铝合金挤压型材的检测不仅是合规性要求,更是企业提升产品附加值的关键。通过系统化的检测项目设计和严格的执行标准,可有效降低质量风险,满足高端市场需求,推动行业向高质量方向发展。
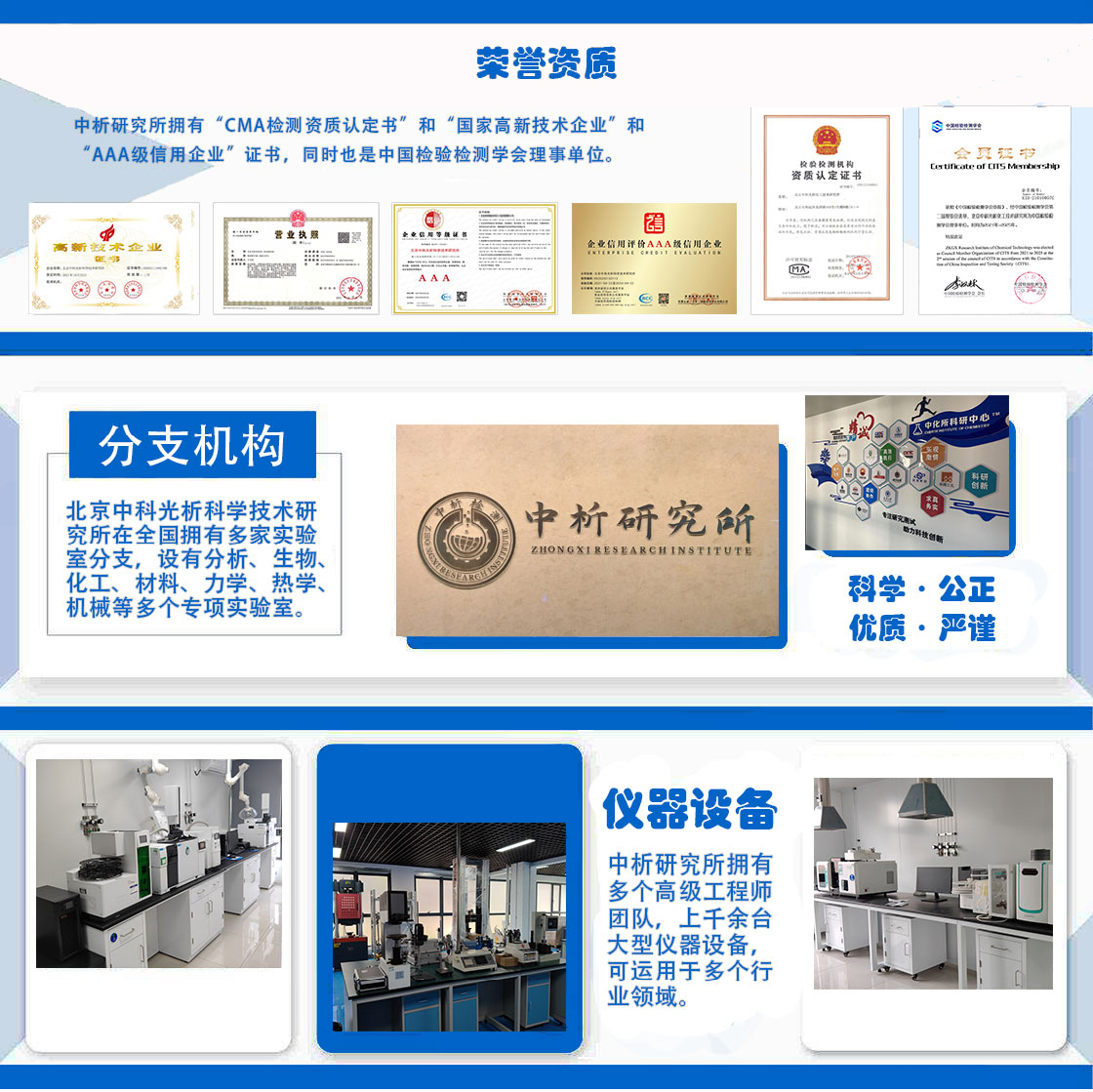
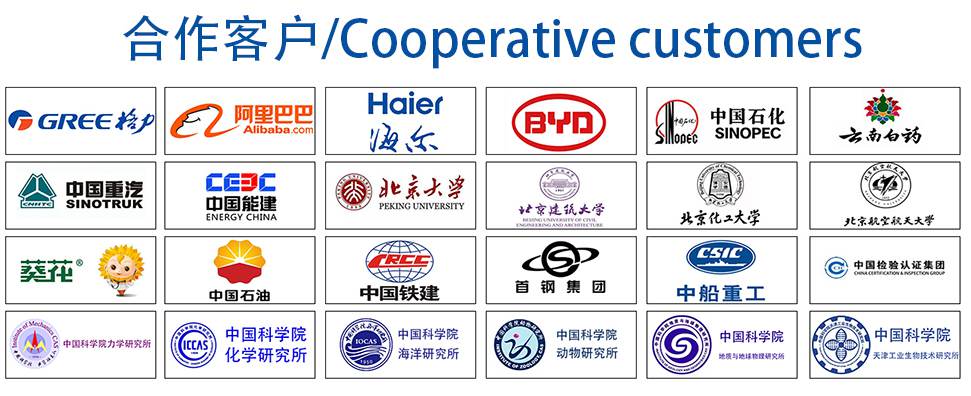