钎焊式管件检测的重要性与应用领域
钎焊式管件作为工业管道系统中的关键连接组件,广泛应用于暖通空调、石油化工、制冷设备及新能源等领域。其通过钎焊工艺实现金属材料的冶金结合,具有密封性强、结构紧凑和承压能力高等特点。然而,钎焊工艺的复杂性以及使用环境的严苛性,使得管件的质量检测成为保障系统安全运行的核心环节。通过系统化的检测项目,可以有效验证钎焊接头的完整性、材料性能及长期耐久性,避免因焊接缺陷导致的泄露、断裂等事故。
钎焊式管件核心检测项目
1. 钎焊质量检测
通过目视检查、渗透探伤(PT)或X射线检测(RT)评估焊缝的连续性、气孔、裂纹及未熔合等缺陷,确保钎料完全填充接头间隙并形成均匀渗透层。
2. 材料成分分析
采用光谱分析仪或化学滴定法验证母材(如铜、不锈钢)和钎料(银基、铜磷合金)的化学成分,防止材料错用导致腐蚀风险。
3. 力学性能测试
包含拉伸试验、弯曲试验和硬度测试,重点检测接头区域的抗拉强度、塑性变形能力及硬度分布,确保满足GB/T 11363标准要求。
4. 气密性与耐压测试
使用氦质谱检漏仪进行气密性检测,并在1.5倍工作压力下实施液压/气压爆破试验,验证管件在极端工况下的密封性能。
5. 尺寸与形位公差检查
通过三坐标测量仪对管件的内径、壁厚、同心度及法兰平面度进行精密测量,确保装配精度和系统密封性。
6. 腐蚀性能评估
开展盐雾试验(ASTM B117)、晶间腐蚀试验(GB/T 4334)和应力腐蚀开裂测试,模拟不同环境下的耐蚀表现。
7. 无损检测技术应用
采用超声波检测(UT)定位内部缺陷,涡流检测(ET)评估导电材料表面裂纹,实现高效非破坏性质量筛查。
8. 表面质量与清洁度检测
检查钎焊残留物、氧化皮及表面粗糙度(Ra≤3.2μm),保证流道通畅并提升介质传输效率。
检测标准的执行与未来发展
当前钎焊式管件检测需严格遵循ASME B16.22、ISO 17635及行业专用规范。随着智能制造技术的进步,基于机器视觉的自动缺陷识别系统和数字化孪生技术的模拟验证平台将进一步提升检测效率与精度,为新型钎焊材料的开发应用提供更可靠的质量保障体系。
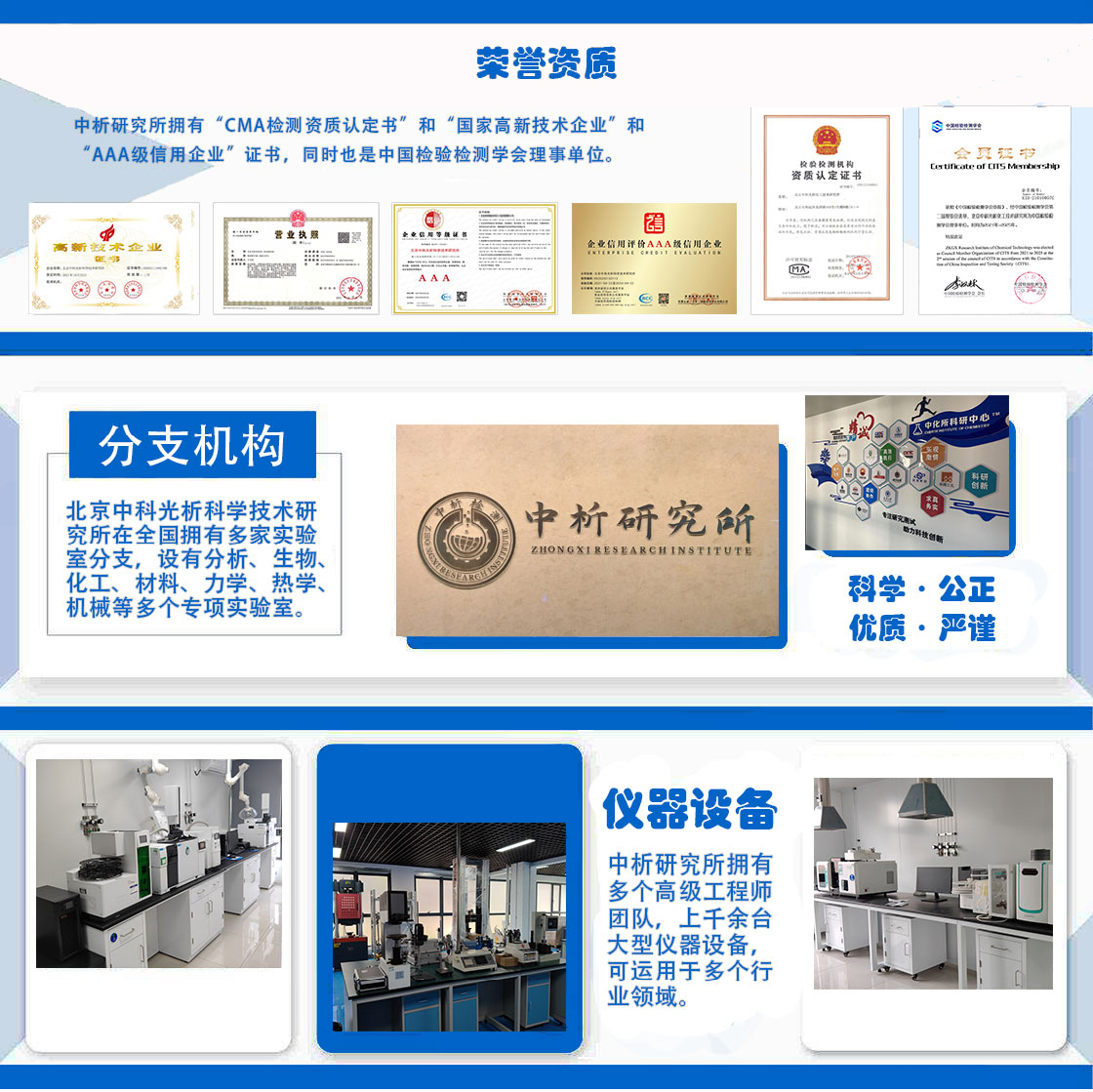
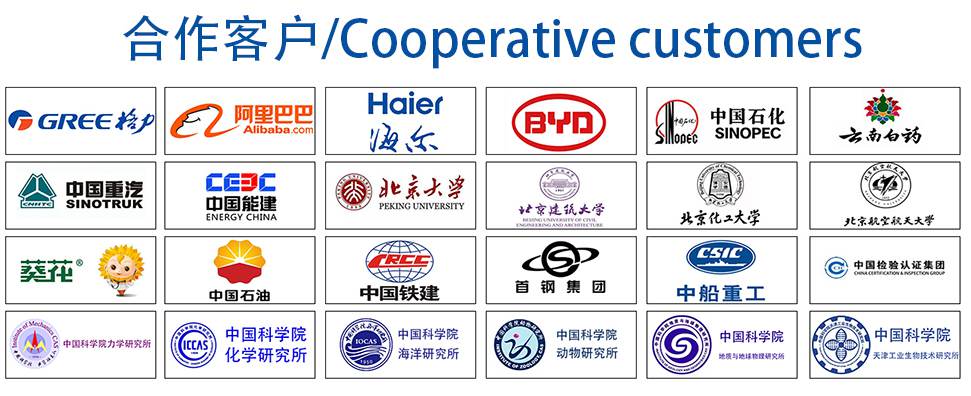