实验室扩大连续试验检测:流程优化与关键技术解析
在科研创新与工业转化过程中,实验室扩大连续试验检测(Scale-up Continuous Testing)作为从实验室研发到工业化生产的核心过渡环节,正受到制药、化工、新能源等领域的重点关注。该检测体系通过模拟实际生产条件,系统验证工艺参数稳定性、设备适配性及产品质量一致性,为大规模生产提供关键数据支撑。根据2023年国际过程工程协会统计显示,采用专业化连续试验检测的项目工业化成功率提升41%,成本节约率可达27%。
一、检测项目核心构成
完整的扩大连续试验检测体系包含三大核心模块:物料稳定性评估模块采用NIR在线监测技术,实时追踪原料粒径、流动性等20+项物性指标;工艺参数验证模块整合多变量DOE实验设计,在反应温度、压力、搅拌速率等关键节点建立动态控制模型;产物质量监控模块应用LC-MS联用系统,实现从分子结构到杂质分布的全面表征。
二、关键检测技术突破
新一代检测平台已实现多项技术创新:微反应器在线采样系统突破传统间歇式检测局限,采样频率提升至毫秒级;智能过程分析技术(PAT)通过机器学习算法建立多维度数据关联,异常参数识别准确率达98.7%;能量消耗监测单元采用光纤传感技术,可精确捕捉0.1%级别的能耗波动。
三、检测流程优化策略
通过建立"三阶段验证法"显著提升检测效率:前期开发阶段采用模块化装置快速筛选工艺窗口,中期验证阶段通过数字孪生技术模拟极端工况,终期确认阶段实施72小时不间断稳定性测试。某制药企业应用该策略后,工艺放大周期由常规的18个月缩短至9个月。
四、行业应用价值延伸
在新能源材料领域,该检测体系成功将锂电正极材料批次稳定性提升至99.5%;生物制药行业通过连续细胞培养检测,单抗产物收率提高32%;精细化工企业借助在线结晶监测技术,实现晶体形态精准控制。检测数据深度分析还可反向指导实验室研发,形成研发-检测-优化的闭环体系。
随着工业4.0技术的深度融合,实验室扩大连续试验检测正朝着智能化、微型化、高通量方向演进。未来检测系统将集成更多AI决策模块,在确保数据可靠性的同时,为工艺放大提供更强大的预测与优化能力。
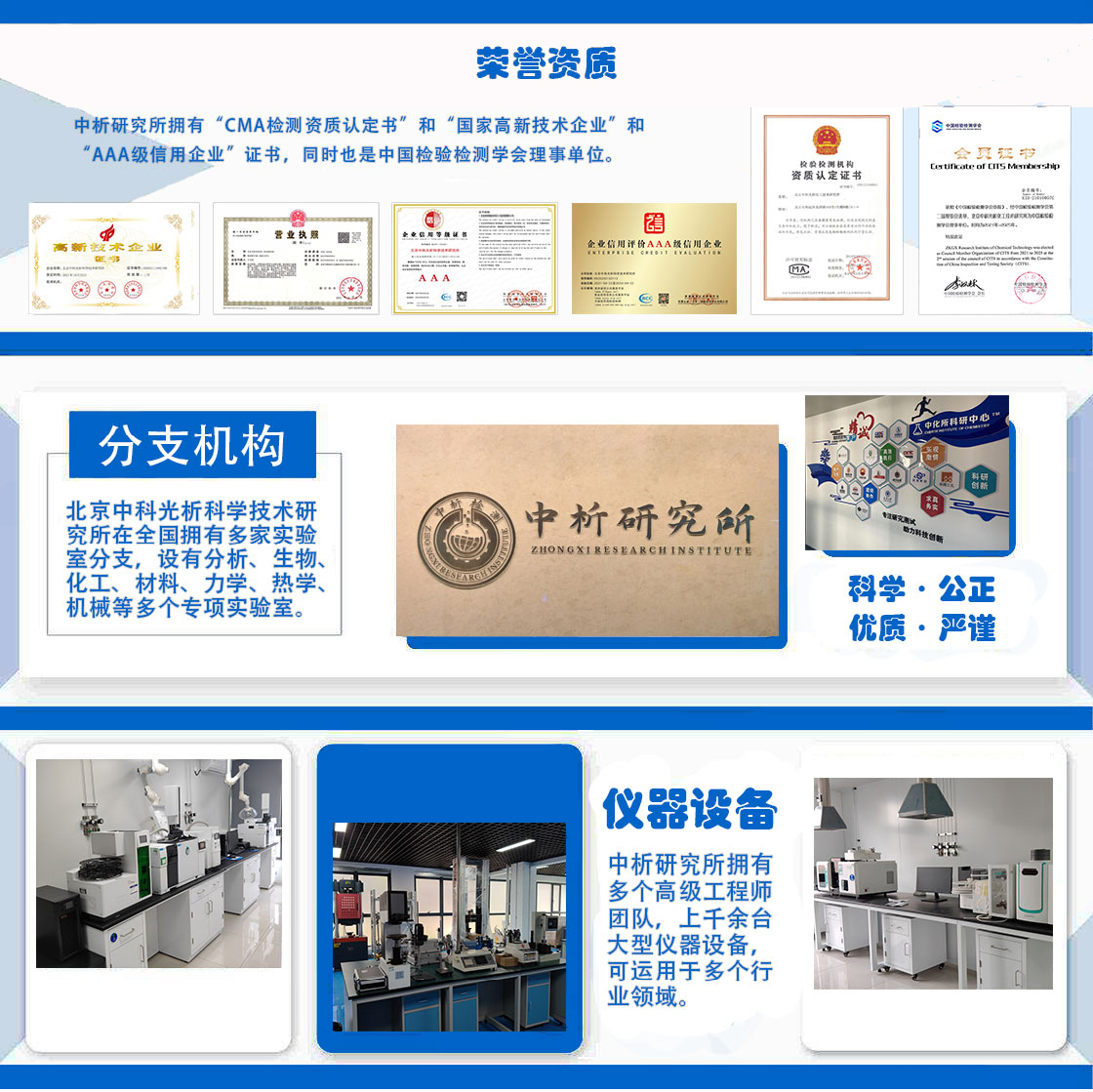
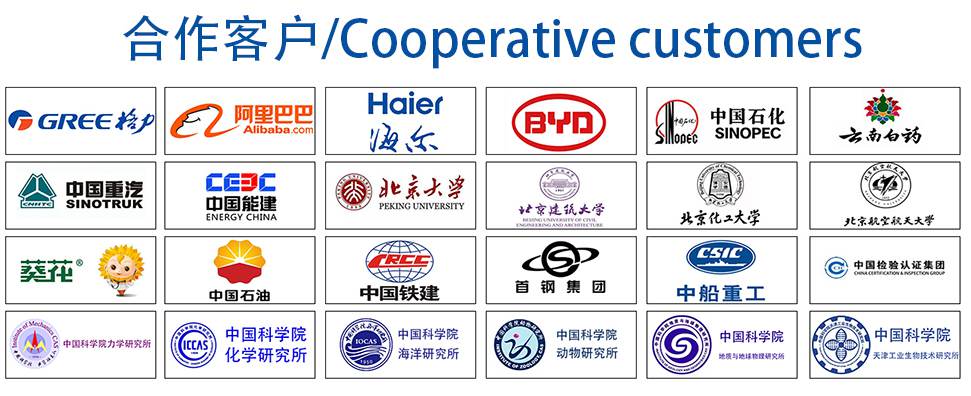