高温合金检测:确保材料性能的核心技术手段
高温合金作为航空航天、能源动力、核工业及化工领域的关键材料,需在极端高温、腐蚀和复杂应力环境下长期稳定服役。其优异的耐高温性、抗氧化性及机械强度直接决定设备的安全性和寿命。随着工业技术的迭代,高温合金的检测需求日益精细化,需通过科学的检测项目全面评估材料的成分、微观结构、力学性能及抗环境侵蚀能力。严格的检测流程不仅为研发提供数据支持,更是工业生产中质量控制的核心环节。
高温合金检测的核心项目解析
1. 化学成分分析
采用电感耦合等离子体发射光谱(ICP-OES)、X射线荧光光谱(XRF)及碳硫分析仪,精确测定镍基、钴基或铁基合金中主量元素(Ni、Cr、Co)及微量元素(Al、Ti、Mo、W等)含量。重点监控氧、氮等杂质元素浓度,避免因成分偏移导致高温强度下降或相变异常。
2. 力学性能测试
通过高温拉伸试验机(测试范围可达1200℃)、蠕变持久试验机及冲击试验装置,系统评估材料在高温环境下的抗拉强度、屈服强度、延伸率及冲击韧性。其中蠕变寿命测试需持续上千小时,模拟长期高温应力下的形变累积效应。
3. 微观组织表征
利用扫描电子显微镜(SEM)结合能谱仪(EDS)分析γ'强化相分布,透射电镜(TEM)观测位错结构,X射线衍射(XRD)检测有害相(如σ相)的存在。通过电子背散射衍射(EBSD)技术量化晶粒取向与尺寸分布,为热处理工艺优化提供依据。
4. 抗腐蚀性能评价
设计高温氧化实验(800-1100℃/1000h)、热腐蚀试验(Na₂SO₄+NaCl盐雾环境)及电化学测试,量化氧化增重速率、氧化膜剥落临界温度及点蚀电位。通过截面显微分析评估氧化层结构致密性,识别内氧化导致的性能劣化风险。
5. 无损检测与缺陷分析
采用工业CT检测内部孔隙率(分辨率<10μm),相控阵超声探伤定位微裂纹,涡流检测筛查近表面缺陷。结合金相剖切验证缺陷三维形貌,建立缺陷尺寸-位置-服役性能的对应关系模型。
6. 特殊环境模拟测试
搭建高温高压水蒸气循环装置(模拟核反应堆环境)、等离子体风洞(模拟超音速气流冲刷)及液态金属腐蚀试验台,评估材料在真实服役条件下的性能演变规律,为部件寿命预测提供数据支撑。
检测技术的前沿发展方向
随着同步辐射光源、原位电镜等齐全表征手段的应用,高温合金检测正从宏观性能评价向多尺度耦合分析升级。基于机器学习的成分-工艺-性能预测模型,以及高温原位监测传感器的集成,将推动检测体系向智能化、实时化方向突破,为新一代高温合金研发提供更强技术保障。
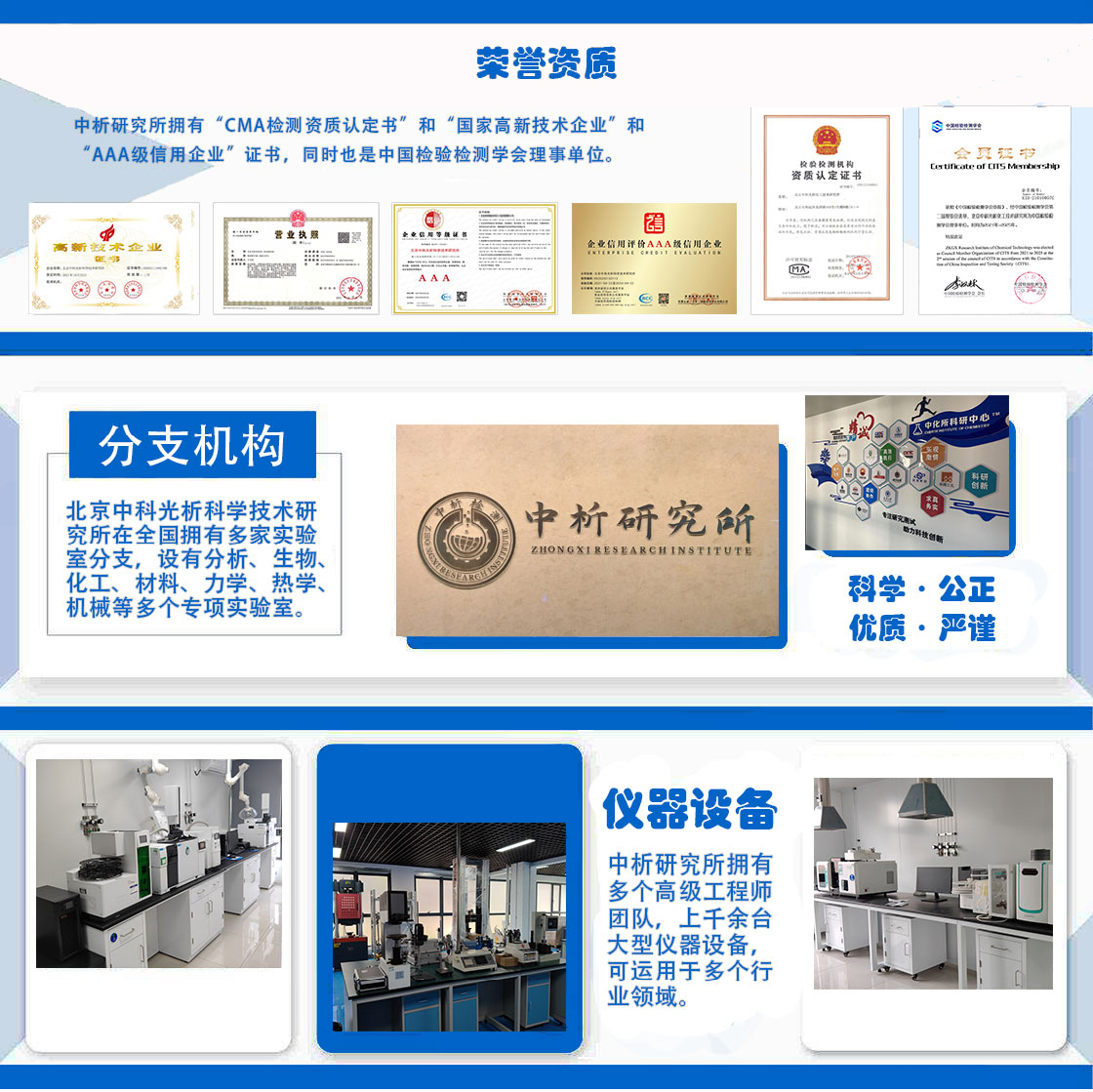
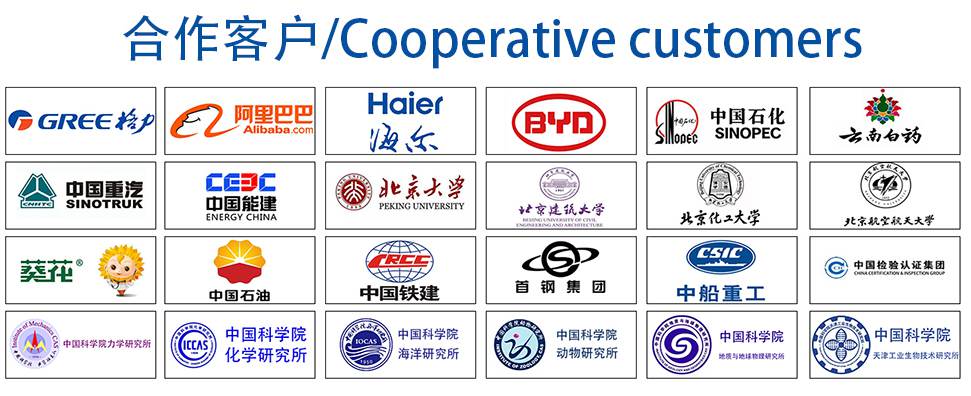