钛及钛合金铸锭检测项目及流程解析
钛及钛合金铸锭作为航空航天、医疗器械、化工装备等高端领域的核心原材料,其质量直接影响最终产品的安全性和使用寿命。为确保材料性能符合设计要求,需通过系统性检测手段对铸锭的多维度特性进行严格把控。以下是针对钛及钛合金铸锭的关键检测项目及技术要点:
一、化学成分分析
采用电感耦合等离子体发射光谱仪(ICP-OES)和惰性气体熔融法,精确测定钛基体中Al、V、Fe、O、N、H等元素的含量。重点控制间隙元素(O、N、H)的浓度,其中氢含量需≤150ppm以避免氢脆风险。
二、宏观组织检测
通过线切割取样后经酸洗处理(HF:HNO₃=1:3),观察铸锭横截面的晶粒尺寸与分布。要求晶粒均匀度偏差不超过15%,异常粗晶区面积占比<5%。
三、超声波探伤(UT)
使用5MHz聚焦探头进行全体积扫查,依据ASTM B594标准判定缺陷等级。重点关注直径≥0.8mm的夹杂物和横向裂纹,允许缺陷密度不超过2个/100mm²。
四、力学性能测试
在万能试验机上进行室温拉伸试验(GB/T 228.1),典型指标要求:抗拉强度≥895MPa,屈服强度≥825MPa,延伸率≥10%。对航空级铸锭还需增加高温(300℃)持久强度测试。
五、微观结构分析
通过金相显微镜和扫描电镜(SEM)观察α相、β相的分布形态及比例,检测晶界化合物的析出情况。要求β相含量偏差不超过标称值的±3%,晶界连续化合物长度≤50μm。
六、残余应力检测
采用X射线衍射法(XRD)测定表面残余应力,要求铸造态应力值<200MPa。对于精密器件用铸锭,需进行去应力退火处理使应力值降至80MPa以下。
七、特殊环境测试
针对医疗植入物用铸锭,需进行模拟体液腐蚀试验(ASTM F2129),腐蚀速率要求≤0.01mm/年。深海装备用材需通过3000m水压试验,检测氢渗透速率变化。
通过上述多维度检测体系,可全面评估钛及钛合金铸锭的冶金质量,确保其满足不同应用场景的严苛要求。检测数据需结合统计学过程控制(SPC)方法,建立从原料到成品的全流程质量追溯机制。
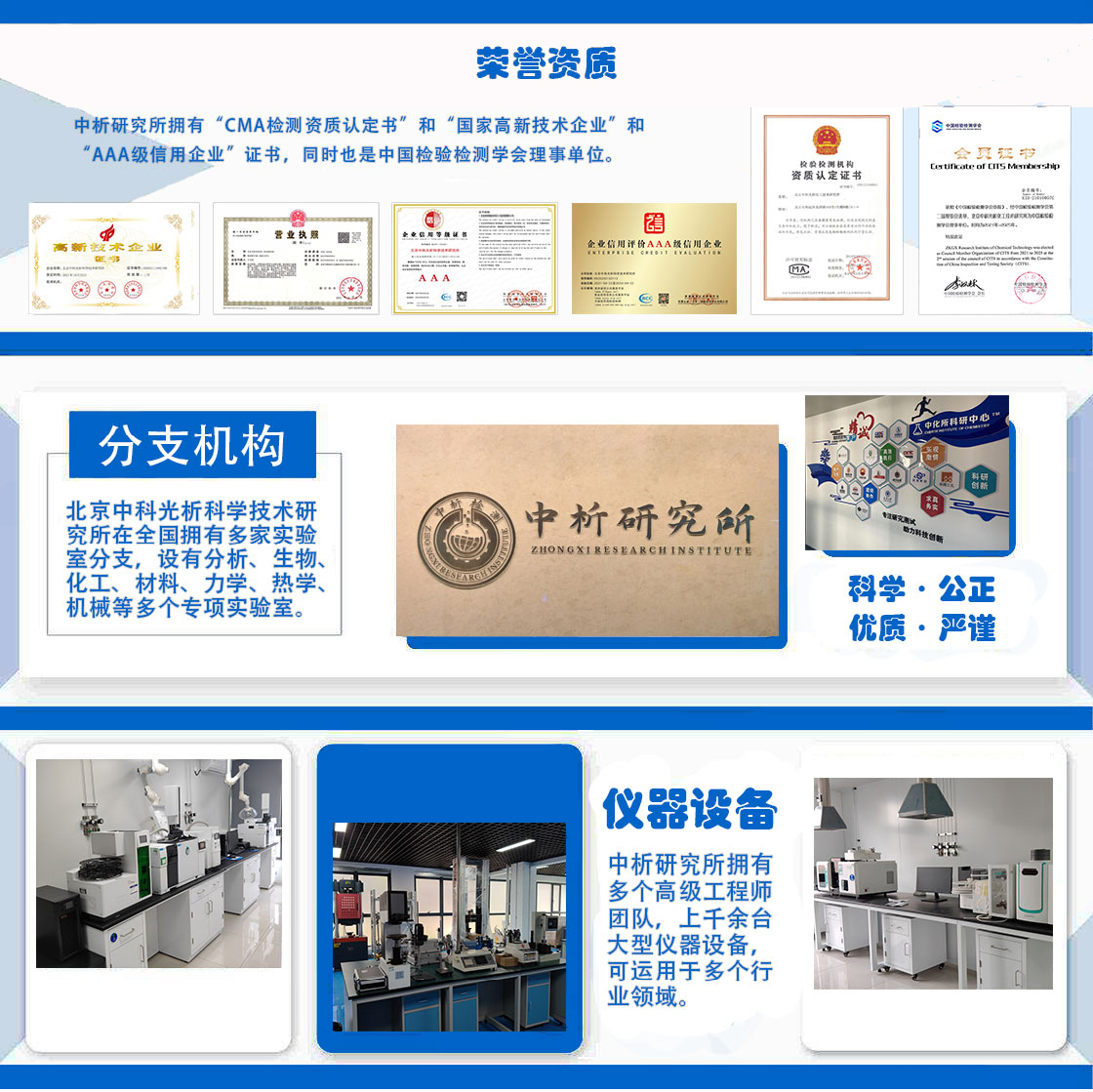
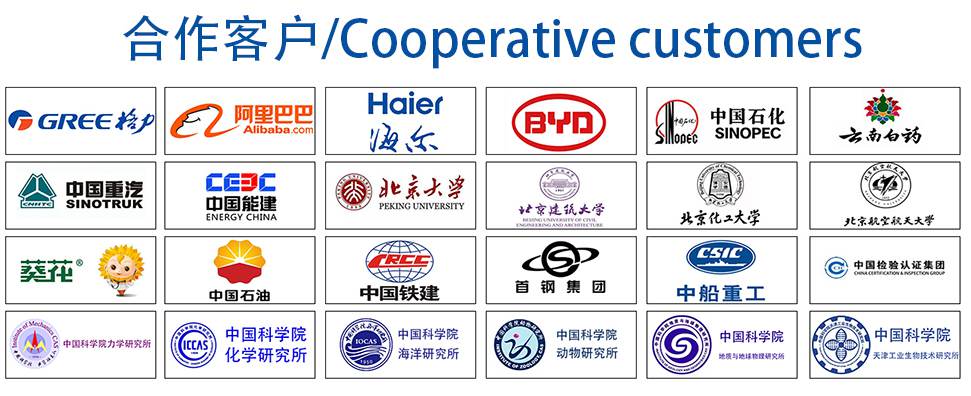