用热设备节能监测检测的重要性与实施要点
随着工业领域对能源效率要求的日益提升,用热设备节能监测检测已成为企业实现绿色生产、降低运营成本的重要环节。锅炉、热交换器、干燥设备等用热装置在运行过程中普遍存在热量损失、燃料浪费等问题,通过科学系统的节能监测检测,可精准定位能效短板,优化设备运行效率。根据《工业锅炉经济运行标准》(GB/T 17954)等规范要求,定期开展节能检测不仅能够满足国家政策监管,更能为企业每年节约5%-30%的能源成本,具有显著的经济效益和社会效益。
核心检测项目及技术要求
用热设备节能监测检测需围绕能效核心指标展开,主要包括以下关键项目:
1. 热效率测试与分析
通过测量设备输入燃料热值与有效输出热量的比值,计算热效率。需使用高精度温度传感器、流量计等设备,结合热平衡方程评估能量转换效率。依据GB/T 10180标准,工业锅炉热效率应≥85%,低于此值需排查燃烧不充分、传热面结垢等问题。
2. 排烟温度与烟气成分监测
采用烟气分析仪实时检测排烟温度及CO、O₂、NOx含量。排烟温度过高(如燃煤锅炉超过160℃)表明余热回收不足,烟气中CO浓度超标则反映燃烧效率低下。建议通过加装换热器、优化空燃比等措施改善。
3. 设备保温性能检测
使用红外热成像仪扫描设备表面温度,结合环境温度计算散热损失。管道保温层表面温升不得超过25℃(环境温度+25℃),阀门、法兰等特殊部位需重点核查。对于保温材料老化、破损的情况应立即更换。
4. 燃料消耗量比对监测
连续记录单位时间燃料消耗量,与设计值或历史数据进行横向对比。若实际耗量超过理论值10%以上,需检查设备负荷率、燃烧控制系统及燃料品质,排除计量仪表误差等因素。
5. 循环水系统能效评估
针对蒸汽系统、热水循环系统,检测循环水泵电耗、管道阻力、冷凝水回收率等参数。通过加装变频器、优化管网设计,可使水泵节电率达20%-40%。冷凝水回收率应达到80%以上,减少热能及水资源浪费。
6. 智能控制系统的合规性验证
核查DCS、PLC等控制系统是否具备自动调节燃烧工况、温度联锁保护功能。重点检测PID控制参数设置合理性,确保在负荷波动时仍能维持最佳热效率。建议配置能源管理平台实现数据可视化分析。
通过上述检测项目的系统实施,企业可构建完整的用热设备能效档案,制定针对性的节能改造方案。检测周期建议每半年开展一次,对于高耗能设备可缩短至季度检测,同时建立能耗基准线以实现持续改进。
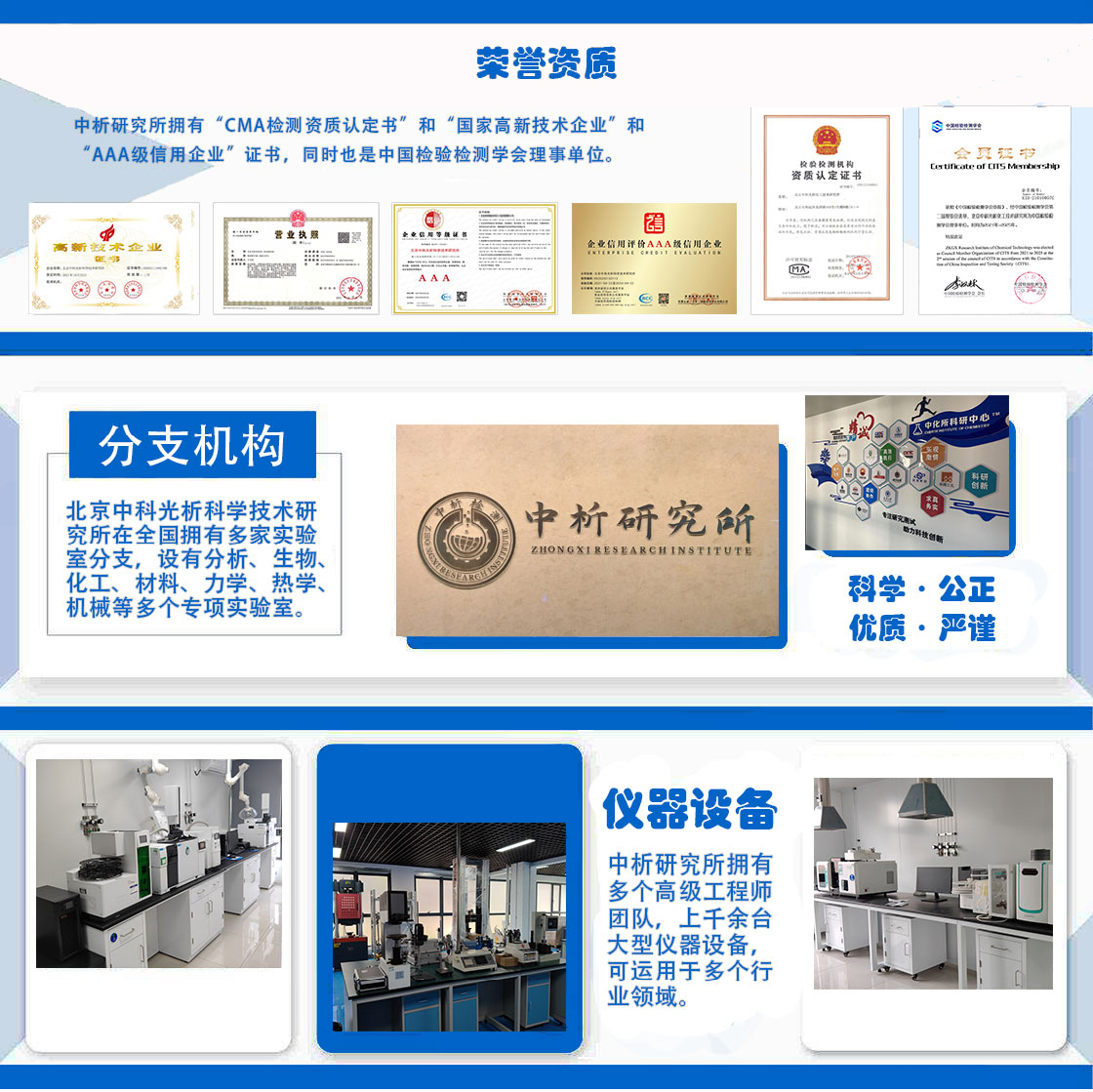
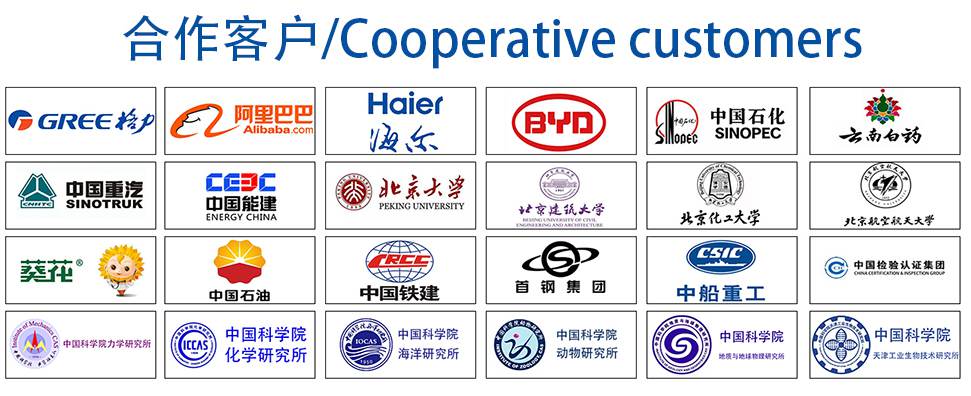