生胶与硫化胶检测的重要性
生胶(未硫化橡胶)和硫化胶(经硫化处理的橡胶)是橡胶工业中的核心材料,广泛应用于轮胎、胶管、密封件等领域。生胶的物理性能和化学稳定性直接影响硫化胶的最终性能,而硫化工艺的精确控制则决定了产品的耐久性、弹性和抗老化能力。为确保材料质量符合行业标准和实际应用需求,必须通过科学的检测方法对生胶和硫化胶的关键指标进行全面分析。
生胶的检测项目及方法
1. 物理性能检测
生胶的物理性能包括门尼粘度、可塑性和拉伸强度。门尼粘度测试(ASTM D1646)用于评估生胶的加工流动性;可塑性测试(威廉氏塑度计)反映材料的软化程度;拉伸强度检测(ISO 37)则通过拉伸试验机测定未硫化胶的力学性能。
2. 化学成分分析
生胶的化学成分直接影响硫化效率。检测项目包括:
- 橡胶烃含量(TGA热重分析);
- 灰分含量(ISO 247);
- 挥发分含量(ISO 248);
- 防老剂及填充剂比例(红外光谱/化学滴定法)。
3. 加工性能评估
通过密炼机或开炼机的模拟加工实验,测试生胶的混炼均匀性、焦烧时间(门尼焦烧试验)及硫化特性(RPA流变仪分析),确保其适用于后续硫化工艺。
硫化胶的检测项目及方法
1. 硫化特性检测
硫化曲线的测定(ASTM D5289)是核心检测项目,通过硫化仪分析正硫化时间(T90)、扭矩最大值等参数,优化硫化工艺条件。
2. 力学性能测试
包括:
- 拉伸强度与断裂伸长率(ISO 37);
- 硬度(邵氏硬度计,ISO 7619-1);
- 耐磨性(阿克隆磨耗试验,ISO 4649);
- 撕裂强度(ASTM D624)。
3. 耐环境性能评估
- 耐老化性:热空气老化试验(ISO 188)、臭氧老化试验(ISO 1431);
- 耐油/耐化学性:浸泡法(ASTM D471)测定体积变化率;
- 低温脆性(ASTM D746)。
检测标准与质量控制
国际标准(ISO)、美国材料协会标准(ASTM)及行业特定规范(如轮胎行业TRA标准)是检测的主要依据。通过严格的实验室检测与生产现场快速检测(如XRF元素分析)相结合,实现从原料到成品的全流程质量监控。
总结
生胶与硫化胶的检测是橡胶制品质量控制的核心环节。通过科学的检测手段对物理性能、化学成分及环境适应性进行精准分析,可有效提升产品可靠性并降低生产风险。企业需结合具体应用场景选择检测项目,并依托专业检测机构确保数据的准确性与权威性。
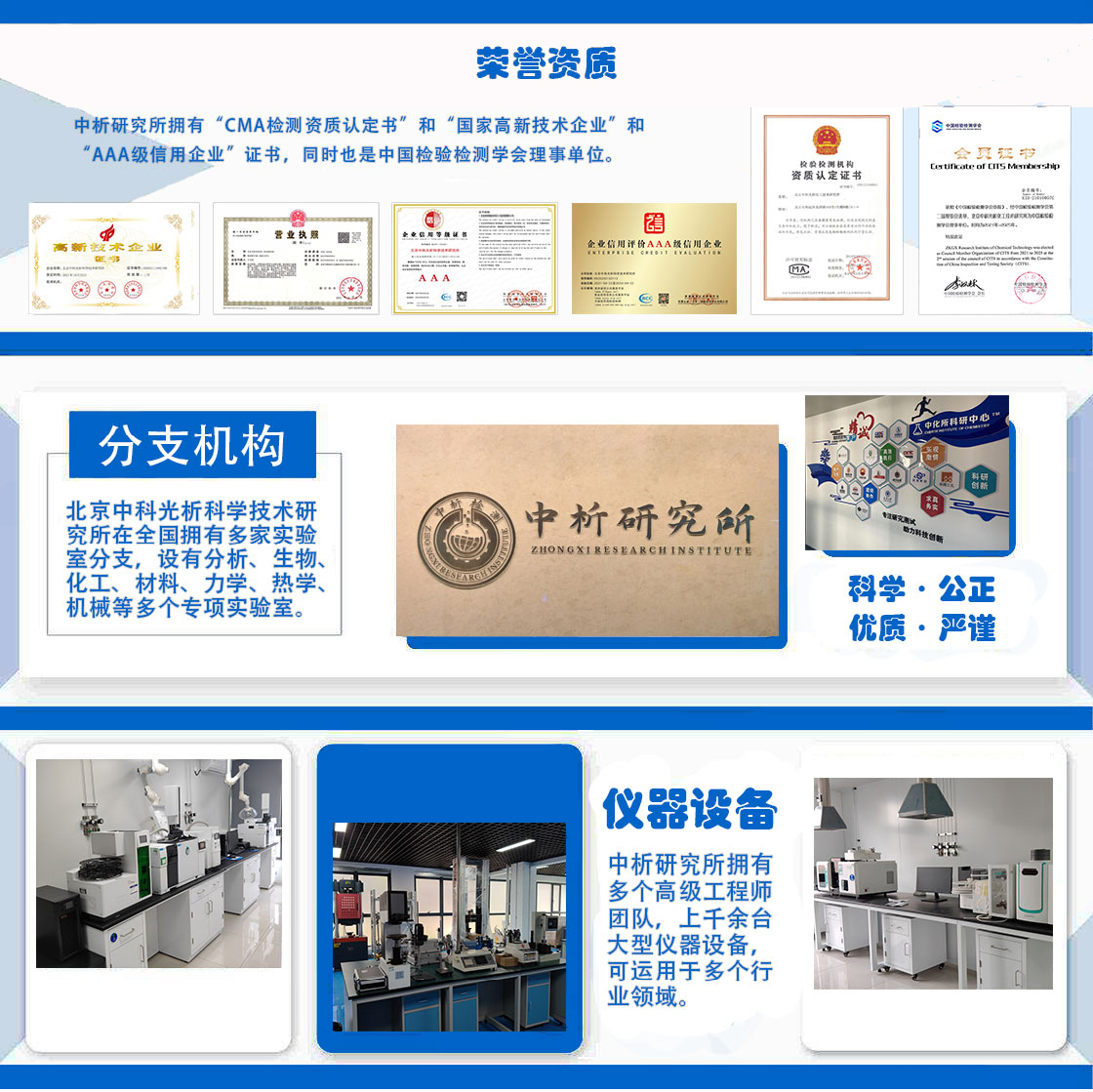
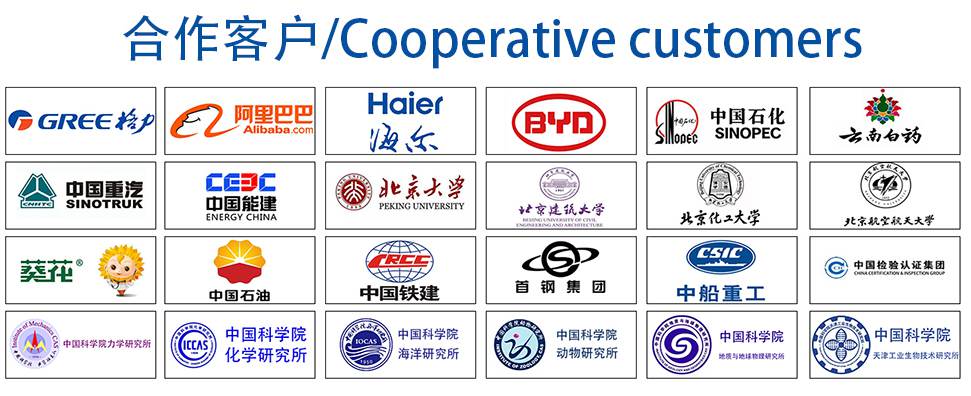