海洋平台检测:保障海上设施安全的关键环节
随着海洋资源开发力度不断加大,海上石油平台、风力发电平台等海洋工程设施的安全运行面临严峻挑战。海洋平台检测作为全生命周期管理的核心环节,涉及结构完整性评估、材料性能分析、环境适应性验证等多维度专业技术。在盐雾腐蚀、海浪冲击、生物附着等恶劣海洋环境下,通过系统化检测可提前发现潜在风险,避免重大安全事故,延长设施使用寿命,确保每年数千亿美元的海上资产安全。
核心检测项目体系
1. 结构安全检测
采用水下无人机(ROV)搭载三维激光扫描仪,对平台桩基、导管架、甲板结构进行毫米级精度的形变监测。通过应变传感器网络实时采集结构应力数据,结合有限元分析模型评估结构承载能力。对焊接节点实施相控阵超声检测(PAUT),可发现深度达50mm的内部缺陷。
2. 腐蚀防护评估
使用多频涡流检测仪量化测定金属构件壁厚损失,配合电化学阻抗谱(EIS)分析涂层劣化程度。对于水下阴极保护系统,需测量结构/电解质电位梯度,确保保护电位维持在-0.85~-1.05V(vs Ag/AgCl)有效区间。典型检测周期为:飞溅区每6个月1次,全浸区每年1次。
3. 设备功能性验证
对钻井模块、发电机组等关键设备进行振动频谱分析,诊断轴承磨损、轴系对中等机械故障。采用热成像技术检测电气系统局部过热现象,结合介质损耗因数(tanδ)测试评估绝缘性能。安全阀等压力元件需实施在线声发射检测与离线水压试验双重验证。
4. 海底管道完整性检测
运用智能清管器(PIG)搭载的漏磁检测(MFL)系统,可识别管壁0.5mm以上的金属损失缺陷。结合侧扫声纳与多波束测深系统,构建海底管道三维空间坐标模型,检测跨距、悬空等异常状态。对于立管系统,需进行VIV(涡激振动)监测与疲劳寿命预测。
5. 数字化检测技术应用
基于数字孪生技术构建平台虚拟模型,整合SCADA系统实时数据与定期检测结果,实现剩余寿命预测与维护决策优化。采用机器学习算法处理历年检测大数据,建立腐蚀速率预测模型,定位高风险区域。通过AR智能眼镜实现检测数据可视化叠加,提升现场作业效率。
前沿检测技术发展
新型光纤光栅传感器可实现应变、温度、振动等参数分布式测量,检测范围覆盖整座平台。磁记忆检测技术可发现构件早期应力集中区域,较传统方法提前6-12个月预警。水下激光清洗机器人逐步应用于检测前表面处理,显著提升检测数据准确性。随着ISO 19902、API RP 2A等标准持续更新,智能化、无人化、在线化正成为海洋平台检测的主流方向。
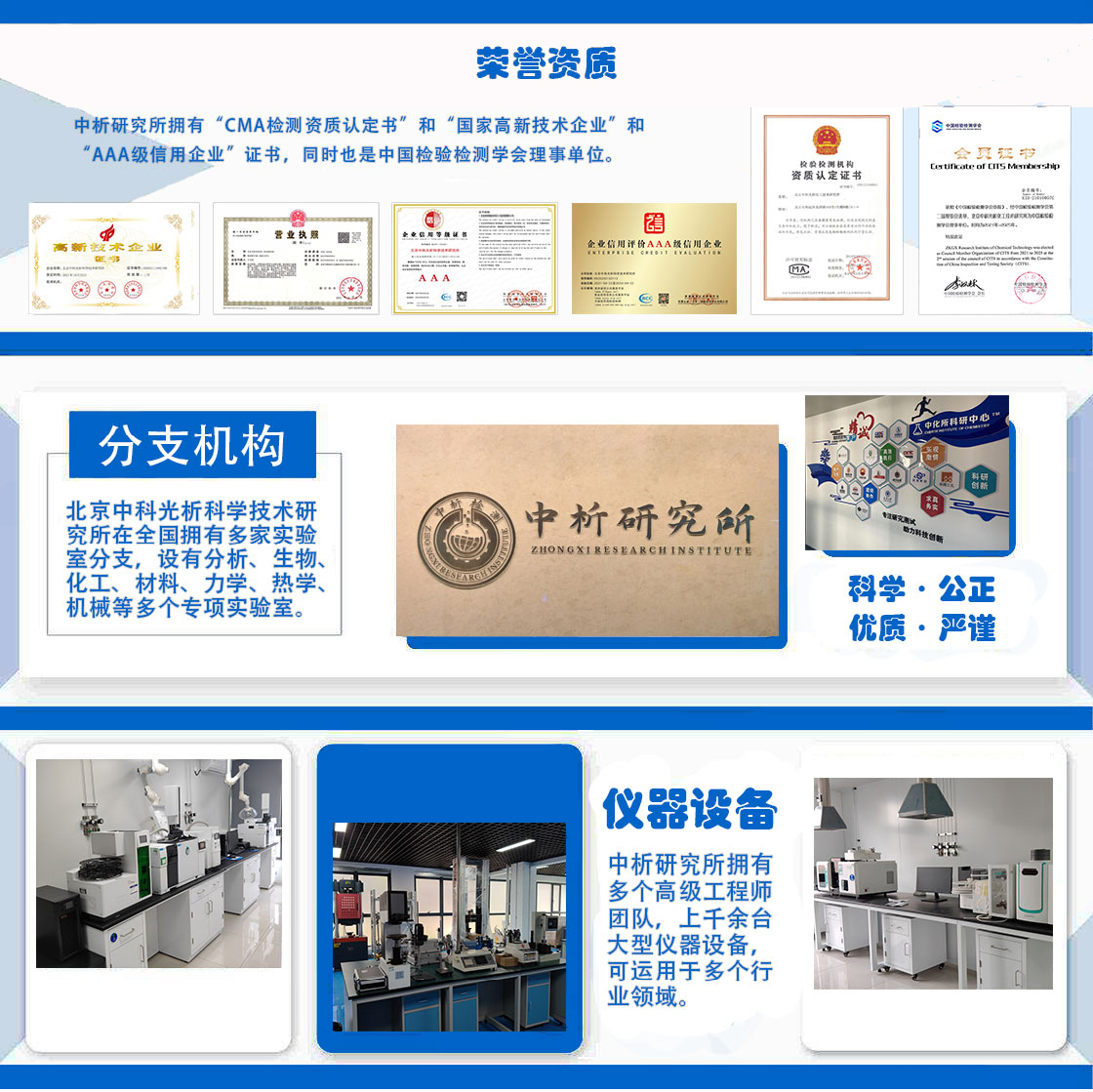
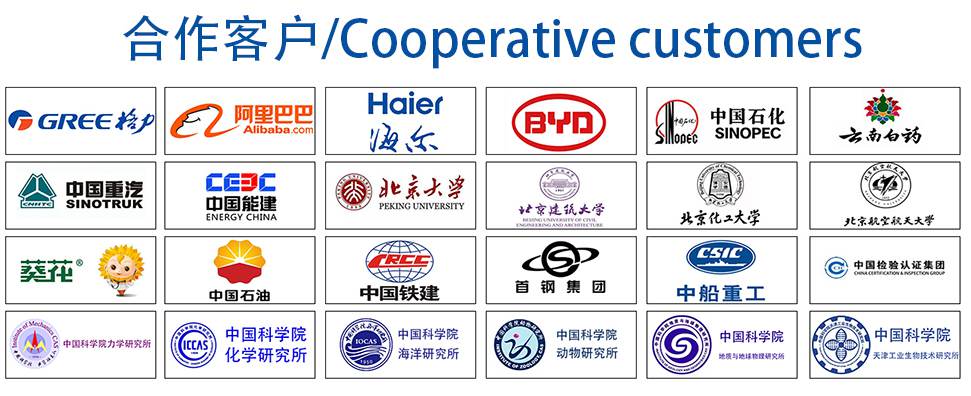