石油机械零配件检测的重要性与核心项目
石油机械零配件作为油气开采、钻探和加工设备的核心组成部分,其质量直接关系到设备的运行效率、安全性和使用寿命。在高温、高压、腐蚀性介质等极端工况下,零配件的微小缺陷可能导致设备故障,甚至引发重大安全事故。因此,建立科学、系统的检测体系,对石油机械零配件进行全生命周期的质量监控,是保障油气行业安全生产和经济效益的关键环节。现代检测技术已涵盖从原材料筛选到成品验收的全流程,结合国家标准(如GB/T)、行业规范(如API标准)以及国际通用准则(如ISO、ASTM),形成了一套多维度的检测方案。
核心检测项目与技术方法
1. 材质成分与金相组织检测
通过光谱分析仪、碳硫分析仪等设备对零配件材料的化学成分进行定量检测,确保符合API 6A、ASTM A182等标准要求。金相显微镜观察材料的晶粒度、夹杂物分布及热处理状态,评估其抗疲劳和耐腐蚀能力。
2. 尺寸精度与形位公差检测
采用三坐标测量机、激光扫描仪等高精度仪器,验证阀门阀体、连接法兰、轴承座等部件的几何尺寸、平面度、圆度等参数,确保与设计图纸的匹配性,满足API 607防火测试中的密封配合要求。
3. 力学性能测试
通过万能材料试验机开展拉伸、压缩、弯曲和冲击试验,测定零配件的屈服强度、抗拉强度、延伸率及冲击韧性。针对钻杆接头、泵阀弹簧等关键件,还需进行高频疲劳试验以模拟实际工况下的耐久性。
4. 表面硬度与耐磨性检测
使用洛氏硬度计、维氏硬度计测量零件表面及特定截面的硬度值,结合摩擦磨损试验机评估镀层(如镍基合金涂层)的耐磨性能,保障螺杆钻具、缸套等部件在磨粒磨损环境下的可靠性。
5. 密封性能与耐压试验
对阀门、管道接头等承压部件进行气密性试验(氮气检漏)和水压/气压爆破试验,检测其在额定压力1.5倍工况下的密封效果和结构完整性,符合API 6D、ASME B16.34等标准规范。
6. 无损检测(NDT)技术应用
综合运用超声波探伤(UT)、磁粉探伤(MT)、渗透探伤(PT)和射线检测(RT),识别铸件、锻件内部的裂纹、气孔等缺陷。针对特殊合金材料,采用涡流检测(ET)和工业CT扫描进行三维缺陷定位。
7. 耐腐蚀与环境适应性测试
通过盐雾试验箱模拟海洋大气环境,结合电化学工作站开展极化曲线分析,评估零配件在H2S、CO2酸性介质中的抗硫化物应力腐蚀开裂(SSCC)能力,满足NACE MR0175标准要求。
8. 动态性能与振动疲劳测试
针对井下工具、旋转导向系统等运动部件,利用振动台和动态信号分析仪进行频谱分析,检测共振频率点并评估长期振动载荷下的结构稳定性,预防因谐波振动引发的早期失效问题。
结论
石油机械零配件检测是一个融合材料科学、机械工程与信息技术的系统工程。通过上述多维度检测项目的实施,不仅能有效规避设备运行风险,还可为产品优化设计提供数据支撑。企业应建立由CMA/ 认证实验室、专业检测设备和技术团队构成的质量控制体系,确保零配件全生命周期性能满足油气行业严苛的工况需求。
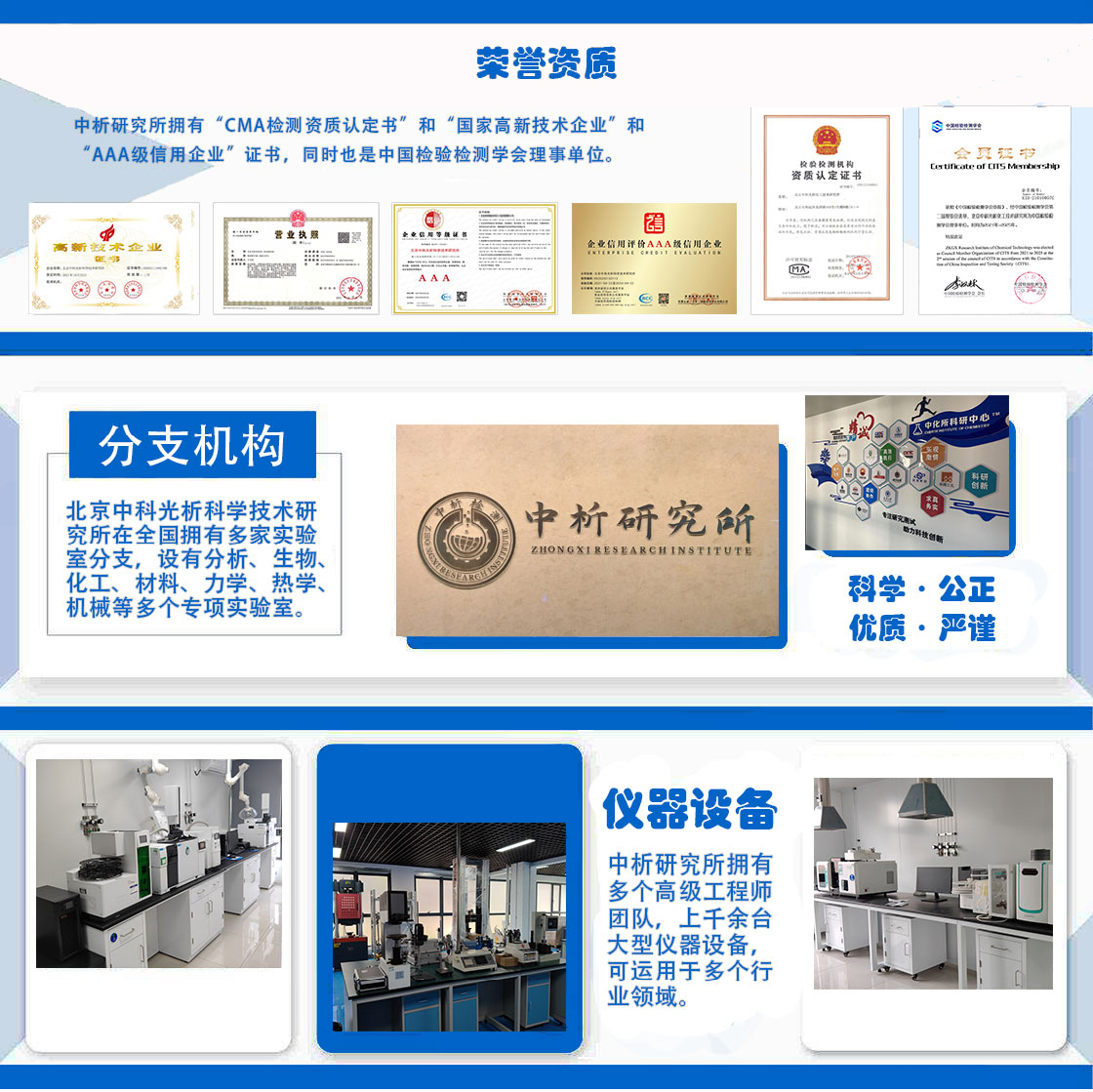
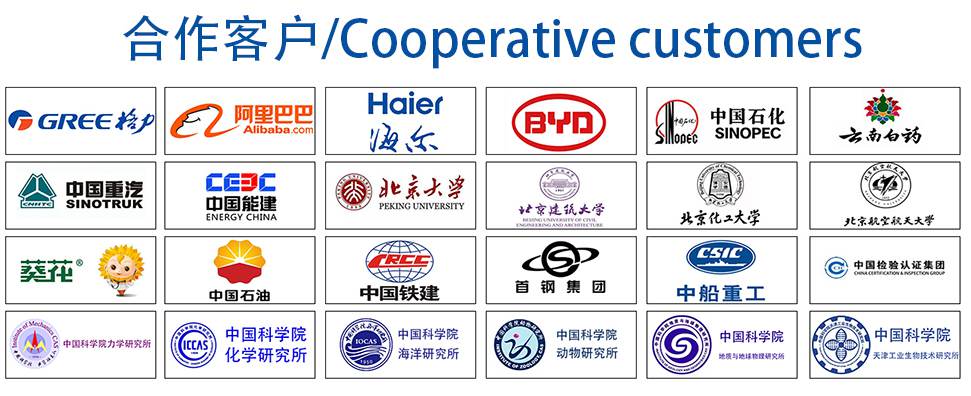