宏观检验检测:工业质量控制的基石
宏观检验检测作为现代工业体系中不可或缺的质量控制手段,通过肉眼或低倍放大镜(通常放大倍数不超过20倍)对材料、零部件或工程结构进行直观检查,在制造业、建筑业、能源设备等众多领域发挥着重要作用。这项技术因其操作便捷、成本低廉且能快速识别明显缺陷的特点,已成为产品出厂前和服役期间最基础且最频繁使用的检测手段。根据国际标准化组织(ISO 17635)的规定,宏观检验通常包括表面状态评估、几何尺寸验证、材料连续性检查等基础项目,其检测结果直接关系到产品的安全性能和服役寿命。
核心检测项目解析
1. 外观完整性检测
通过目视检查或低倍放大观察,识别材料表面的裂纹、折叠、气孔等缺陷。在铸件检测中可发现缩孔疏松,在锻件中能检测折叠裂纹,在焊接接头处可发现未熔合、咬边等典型缺陷,检测精度可达0.1mm级。
2. 几何尺寸验证
使用卡尺、量规等工具测量工件实际尺寸与设计图纸的符合度,重点检查关键部位的尺寸公差。管道工程中管口椭圆度测量误差需控制在0.5%以内,压力容器开孔位置偏差不得超过±3mm。
3. 腐蚀损伤评估
针对服役设备进行腐蚀坑深度测量、腐蚀面积占比计算,采用腐蚀标尺辅助判断腐蚀程度。石化管道检测要求腐蚀减薄量超过壁厚10%时必须进行修复,海上平台结构腐蚀面积超过30%需局部更换。
4. 装配状态检查
验证零部件装配位置、连接状态是否符合设计要求。在航空航天领域,发动机叶片安装角度偏差需控制在±0.5°以内,轨道交通轮对装配游隙应保持在0.5-1.2mm区间。
5. 涂层质量检验
评估防腐/装饰涂层的覆盖完整性、附着强度及厚度均匀性。船舶涂装要求干膜厚度达到300μm以上,附着力测试需达到ISO等级1级标准,针孔检测每平方米不得超过3个缺陷点。
技术延伸与创新应用
随着数字化检测技术的发展,现代宏观检验已突破传统目视检查的局限。三维扫描仪可实现0.02mm级精度尺寸测绘,热成像技术能识别肉眼不可见的内部缺陷,无人机搭载高清相机可完成百米高空结构的全面检测。在港珠澳大桥建设过程中,工程团队通过配备激光测距仪的检测机器人,实现了对沉管隧道接缝0.1mm级精度的自动化检测。
质量控制的关键价值
有效的宏观检验能及时发现80%以上的制造缺陷,使产品报废率降低40%以上。在核电设备制造中,严格的宏观检验程序可将焊接缺陷率控制在0.3%以下。统计显示,全面实施宏观检验的工程项目,其全生命周期维护成本可降低25%,设备故障率下降60%以上,充分体现了"预防优于修复"的质量管理理念。
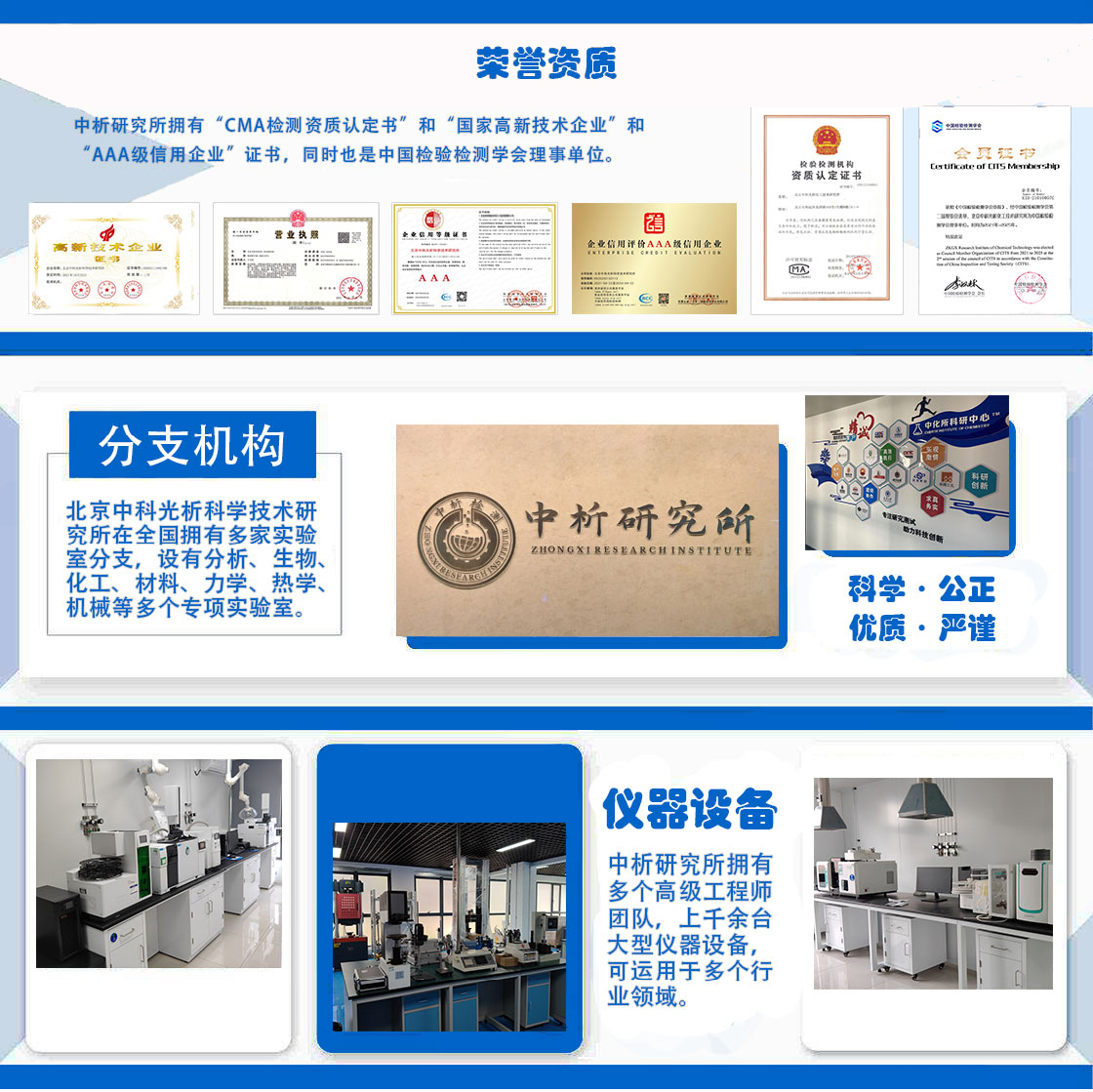
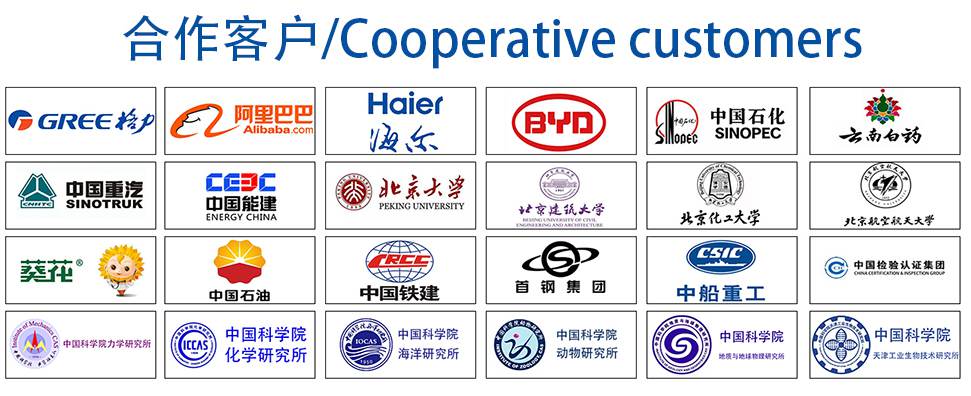