塑料管道系统用塑料部件检测的重要性
塑料管道系统广泛应用于建筑给排水、市政工程、农业灌溉、工业流体输送等领域,其安全性和耐久性直接关系到工程质量和用户安全。塑料部件作为管道系统的核心组成部分,需具备优异的力学性能、耐化学腐蚀性、抗老化能力及尺寸稳定性。通过科学规范的检测手段,可验证塑料部件是否符合国家标准(如GB/T 18252、ISO 1167等)及行业应用要求,有效避免因材料缺陷导致的泄漏、开裂等问题,从而延长系统使用寿命并降低维护成本。
关键检测项目及方法
1. 物理与力学性能检测
塑料部件的物理性能直接影响其实际使用效果。主要检测项目包括:
• 静液压试验:模拟管道长期承压状态,检测耐压强度及蠕变性能,验证设计寿命内是否会发生爆管或形变。
• 环刚度测试:通过径向加压评估管材抗外压能力,适用于埋地管道或承受外部载荷的部件。
• 落锤冲击试验:测定部件在低温或高冲击负荷下的韧性,避免因外力冲击导致脆性破裂。
2. 化学与耐环境性能检测
塑料部件需适应复杂环境条件,需重点检测:
• 耐化学腐蚀性:将试样浸泡于酸、碱、盐溶液或油类介质中,观察质量变化及力学性能衰减程度。
• 耐候性与紫外老化测试:通过氙灯加速老化试验评估材料抗紫外线能力,预测户外使用时的寿命衰减。
• 氧化诱导时间(OIT):测定材料抗氧化稳定性,判断抗热氧老化能力。
3. 加工与功能性检测
生产工艺直接影响部件质量,需进行以下专项测试:
• 熔体质量流动速率(MFR/MVR):评估材料加工流动特性,确保注塑或挤出成型的工艺稳定性。
• 热稳定性测试:通过热重分析(TGA)检测材料分解温度,优化加工参数。
• 接缝强度试验:针对焊接或粘接接头,测定其抗拉强度是否符合密封要求。
4. 尺寸与结构完整性检测
几何精度是保证系统密封性的基础,包括:
• 壁厚均匀性测定:使用超声波测厚仪或光学测量设备检测管材截面厚度偏差。
• 外径/内径公差检测:通过精密量具验证部件尺寸是否符合连接件配合要求。
• 圆度与直线度测量:确保管道安装时无应力集中现象,减少局部变形风险。
检测标准与质量控制体系
检测需严格遵循GB/T 8804(拉伸性能)、GB/T 6111(液压试验)、ISO 3127(耐化学性)等标准。企业应建立从原料入厂检验到成品出厂测试的全流程质控体系,结合第三方实验室认证,确保数据真实可靠。对于食品接触类管道,还需额外通过GB 4806系列标准的安全性评估。
结语
塑料管道部件的系统性检测是保障工程安全的核心环节。通过多维度性能验证,不仅能筛选出不合格产品,更能推动材料改性技术升级和工艺优化。随着智能检测设备与大数据分析技术的应用,未来行业将向更高效、精准的智慧检测模式发展,为塑料管道系统的可靠运行提供坚实保障。
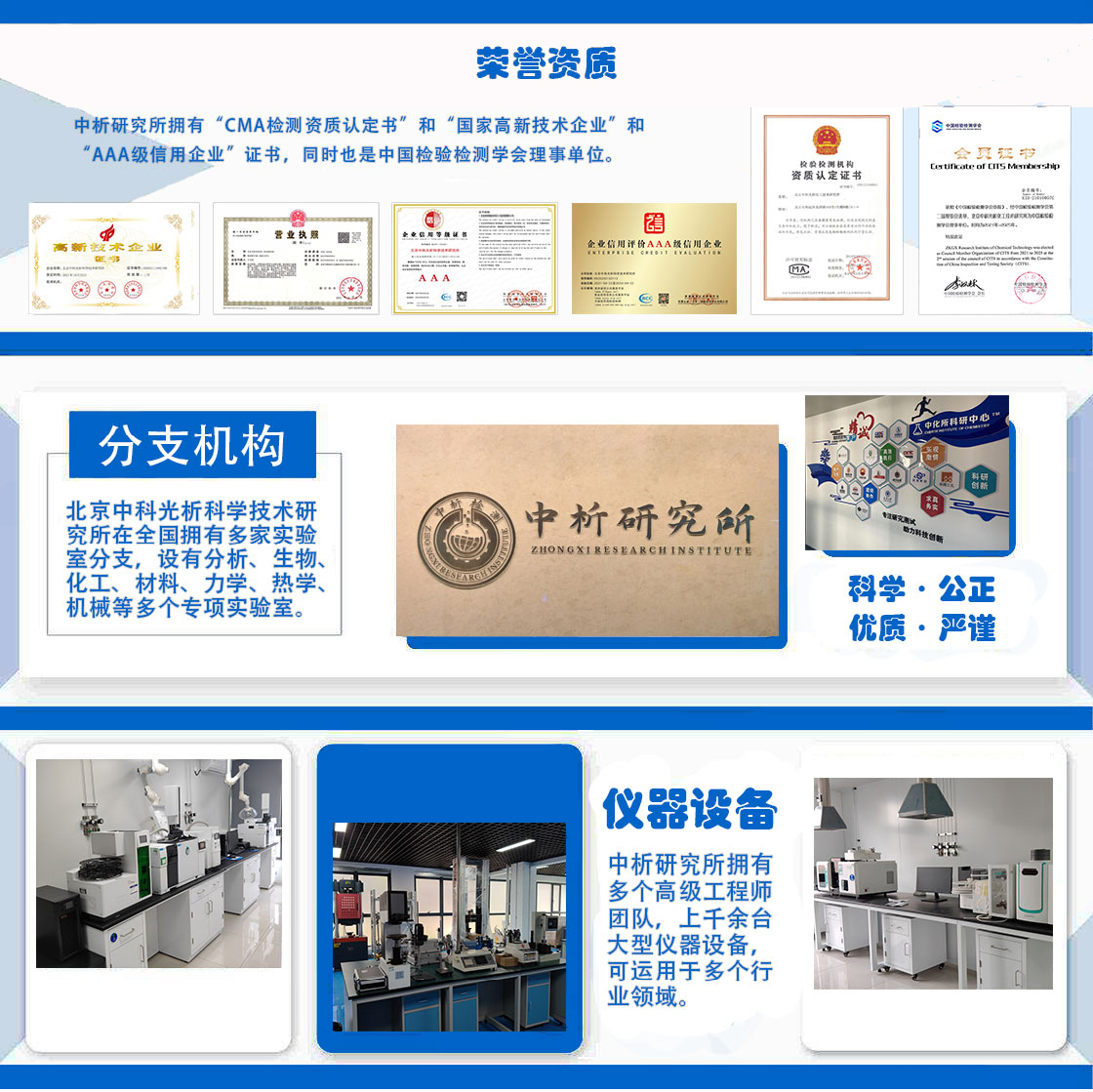
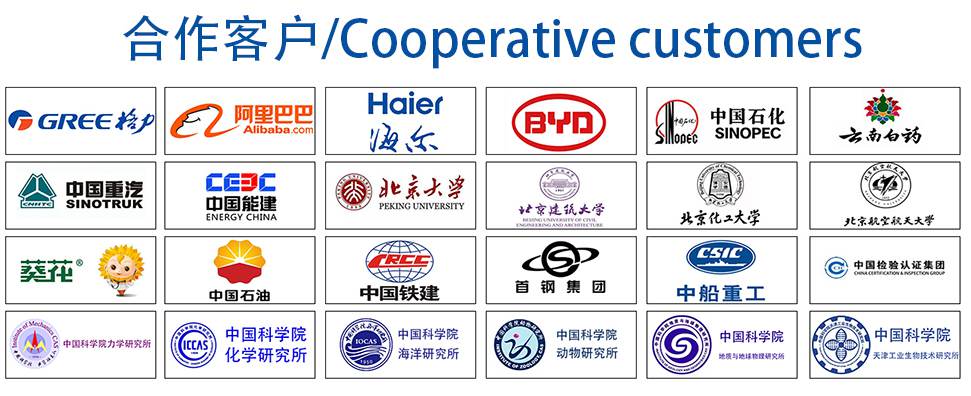