船用钢管对焊接头检测的重要性
船用钢管作为船舶动力系统、管路系统及结构支撑的核心部件,其焊接接头的质量直接关系到船舶的安全性和可靠性。焊接接头若存在缺陷,如裂纹、气孔、未熔合等问题,可能引发泄漏、断裂甚至灾难性事故。因此,在船舶制造和维修过程中,对钢管对焊接头的检测至关重要。目前,行业普遍采用多维度检测手段,结合国际标准(如ISO 5817、AWS D1.1等)和船级社规范(如CCS、DNV等),形成了一套完善的检测流程,以确保焊接质量满足严苛的船舶工况要求。
船用钢管对焊接头的主要检测项目
1. 外观检查
外观检查是焊接接头检测的基础环节,主要通过目视或借助放大镜、焊缝检测尺等工具,检查焊缝成型是否均匀、表面是否存在咬边、凹陷、飞溅等缺陷。同时需确认焊缝余高、宽度是否符合工艺要求,以及焊趾过渡是否平滑。
2. 无损检测(NDT)
无损检测是发现内部缺陷的核心手段,包括以下方法:
射线检测(RT):利用X射线或γ射线穿透焊缝,通过成像技术检测气孔、夹渣、未焊透等缺陷。适用于厚度较大的钢管对接焊缝。
超声波检测(UT):通过高频声波反射信号识别内部裂纹、未熔合等缺陷,尤其擅长检测垂直于焊缝的平面型缺陷。
渗透检测(PT)与磁粉检测(MT):用于表面及近表面缺陷的检测,渗透检测适用于非磁性材料,磁粉检测则用于铁磁性钢管。
3. 力学性能测试
通过取样实验验证焊接接头的力学性能,包括:
拉伸试验:测试焊缝及热影响区的抗拉强度是否达标。
弯曲试验:评估焊缝的塑性和抗裂性能,通常包括正弯、背弯和侧弯试验。
冲击试验:在低温环境下测试焊缝的韧性,确保其适应极端工况。
硬度测试:检测热影响区硬度分布,避免因焊接热输入不当导致材料脆化。
4. 化学成分分析
采用光谱仪或化学滴定法,对焊缝金属的化学成分进行检测,确保母材与焊材的匹配性,防止因元素偏析导致耐腐蚀性或强度下降。
5. 压力试验
对焊后钢管进行水压或气压试验,验证其在设计压力下的密封性和结构完整性。试验压力通常为工作压力的1.25-1.5倍,并需保压足够时间。
6. 尺寸与形位公差检测
使用卡尺、三维扫描仪等工具测量焊缝坡口角度、错边量、焊缝宽度等参数,确保符合工艺规范。对于大口径钢管,还需检测对接后的同轴度偏差。
7. 焊接工艺评定(PQR)与焊工认证
通过工艺评定试验确认焊接参数的合理性,同时对焊工操作技能进行考核,确保其具备执行高精度焊接的能力。
检测技术的发展趋势
随着数字化技术的普及,自动化相控阵超声波检测(PAUT)、工业CT扫描、基于AI的缺陷识别系统等新兴技术逐步应用于船用钢管检测领域。这些技术可提高检测效率,减少人为误差,并为焊接质量提供更全面的数据支持。
船用钢管对焊接头的检测贯穿设计、制造、安装及运维全生命周期,通过系统化的检测项目组合,能够有效控制质量风险,为船舶的安全航行提供坚实保障。
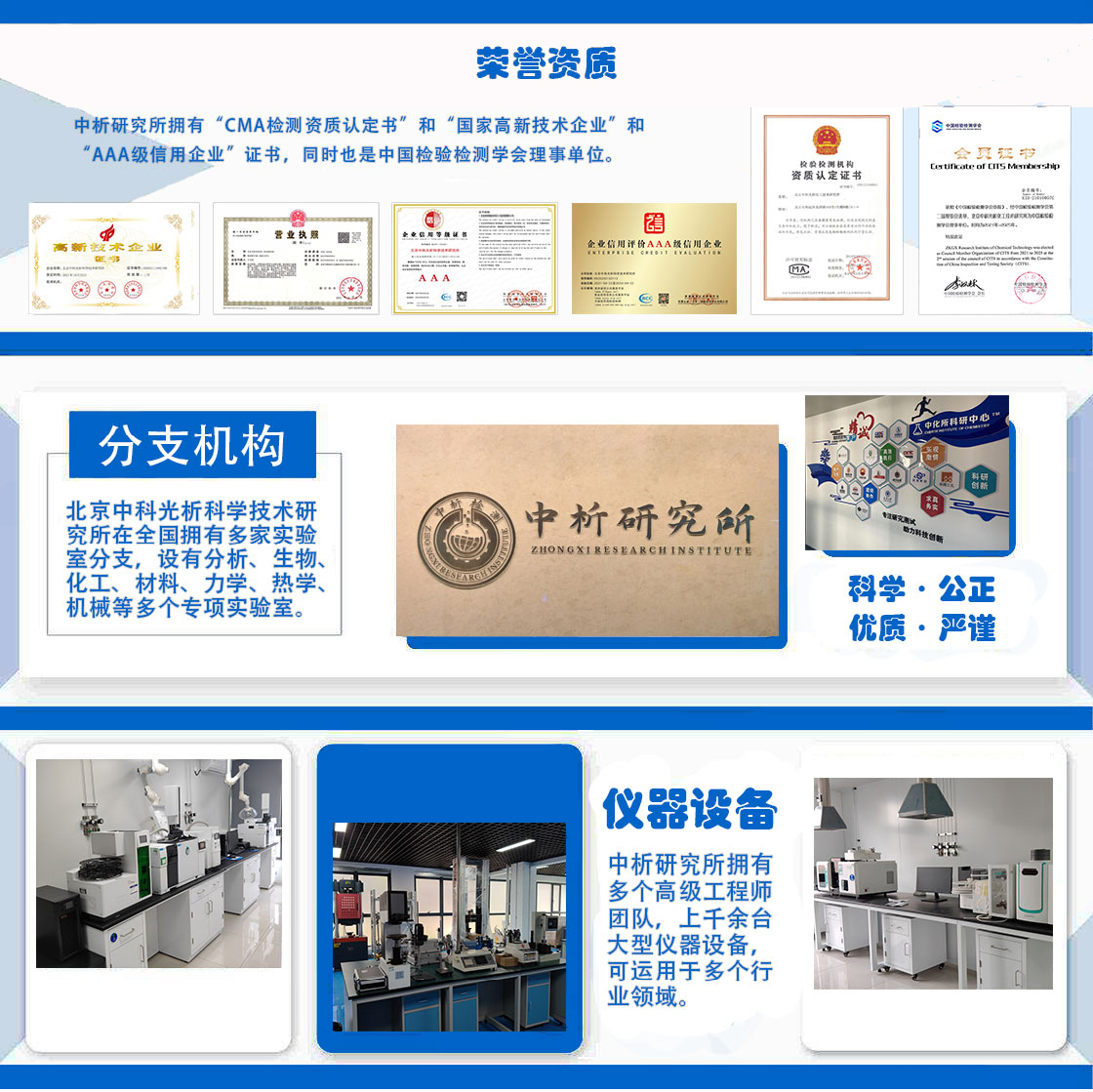
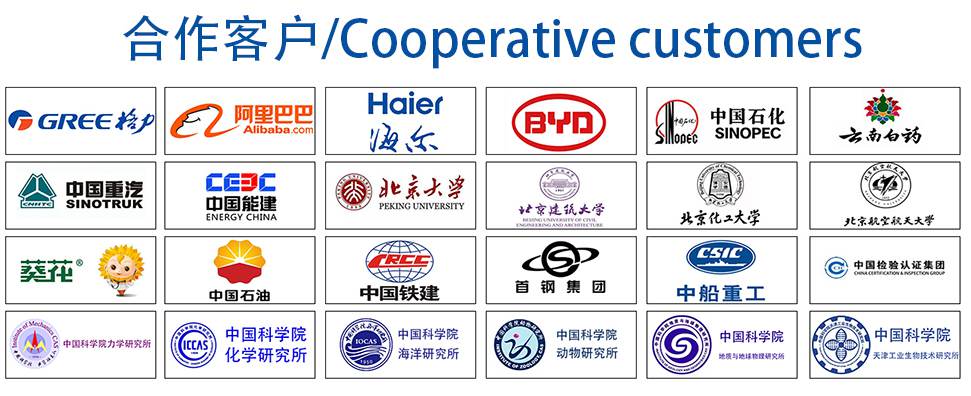