石油天然气输送管用宽厚钢板检测的重要性
石油天然气输送管道作为能源运输的核心设施,其安全性与可靠性直接关系到国民经济和生态环境。宽厚钢板作为管道制造的关键材料,需具备高强度、耐腐蚀、抗疲劳及低温韧性等综合性能,以满足高压、高低温、腐蚀性介质等复杂工况需求。然而,材料生产过程中可能出现的成分偏差、内部缺陷或力学性能不足等问题,可能引发管道泄漏甚至爆裂事故。因此,对宽厚钢板进行全面、精准的检测是保障管道长期安全运行的必要环节。
核心检测项目及技术要点
1. 化学成分分析
通过光谱分析仪和化学滴定法,检测钢板中碳(C)、锰(Mn)、硅(Si)、硫(S)、磷(P)等元素的含量,确保符合API 5L、ASTM A516等标准要求。重点控制硫磷含量以减少晶界脆化,并优化合金元素配比以提升耐腐蚀性。
2. 力学性能测试
包括拉伸试验(测定屈服强度、抗拉强度、延伸率)、夏比冲击试验(评估-20℃~-45℃低温韧性)及硬度测试(布氏/洛氏硬度)。需模拟管道实际服役条件,验证材料在极端压力下的抗变形能力和抗冲击性能。
3. 显微组织分析
采用金相显微镜和扫描电镜(SEM)观察钢板微观结构,分析晶粒尺寸、带状组织、非金属夹杂物分布及第二相析出情况。良好均匀的显微组织可显著提升抗氢致开裂(HIC)和应力腐蚀(SCC)能力。
4. 无损检测(NDT)
运用超声波探伤(UT)检测内部裂纹、分层缺陷;磁粉检测(MT)识别表面及近表面缺陷;射线检测(RT)验证焊缝质量。检测灵敏度需满足ASTM E317标准,缺陷尺寸需严格控制在API 5L规定的允许范围内。
5. 腐蚀性能评估
通过盐雾试验、电化学阻抗谱(EIS)和慢应变速率试验(SSRT),模拟H2S、CO2等腐蚀环境,评估钢板的耐均匀腐蚀、点蚀及应力腐蚀开裂性能,确保其在含硫油气田中的长期稳定性。
6. 尺寸与外观检验
使用激光测距仪、三维轮廓仪等设备检测钢板厚度偏差(±0.1mm)、平面度(≤3mm/m)及边缘直线度。表面需无氧化皮残留、划痕深度不得超过标准允许值(通常≤0.3mm)。
质量控制与标准体系
检测过程需严格遵循ISO 3183、GB/T 9711等国际/国家标准,结合数字孪生技术建立材料性能数据库,实现从原料到成品的全流程追溯。通过智能化检测设备的应用(如自动探伤机器人),可将检测效率提升40%以上,同时降低人为误差风险。
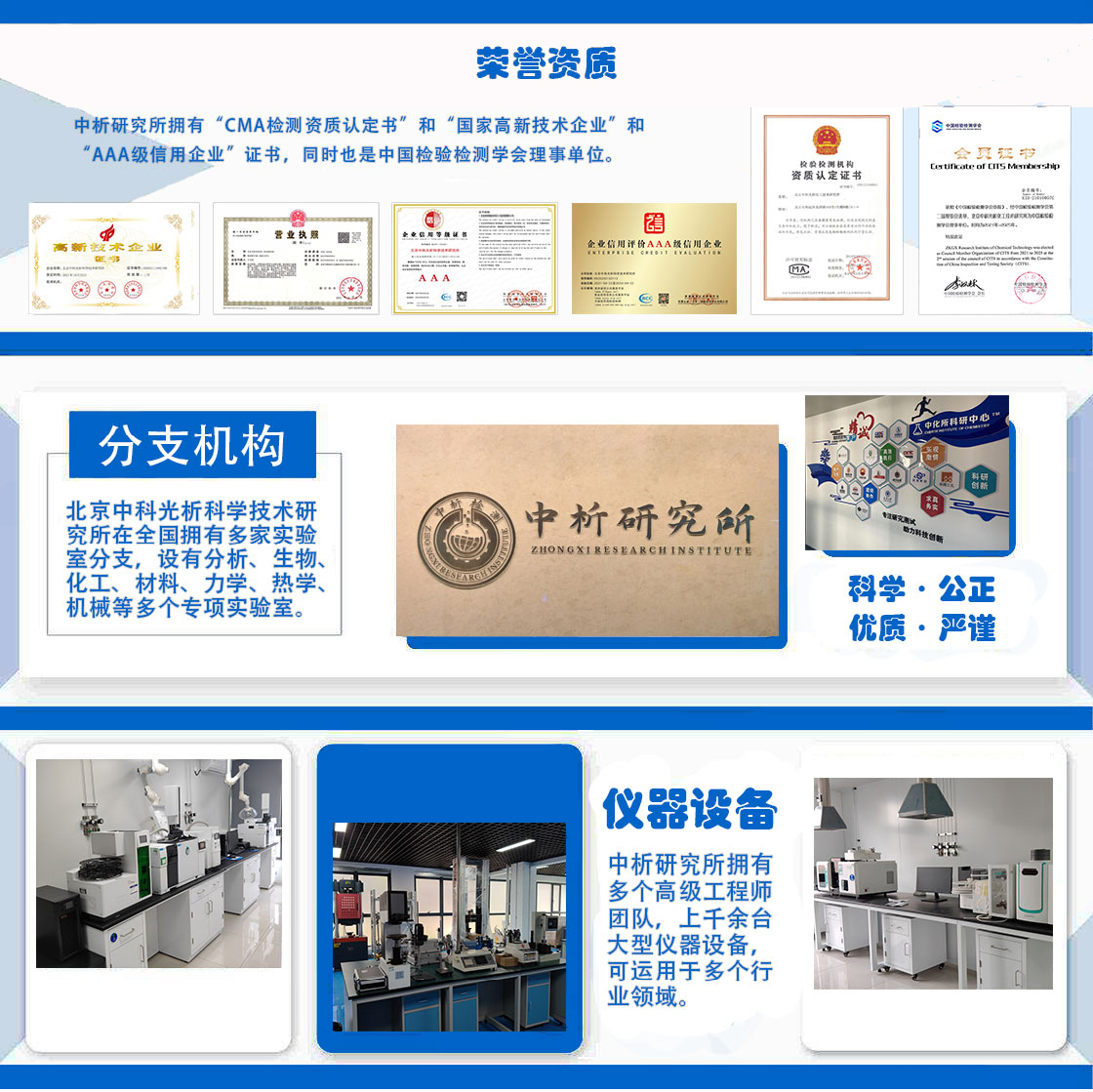
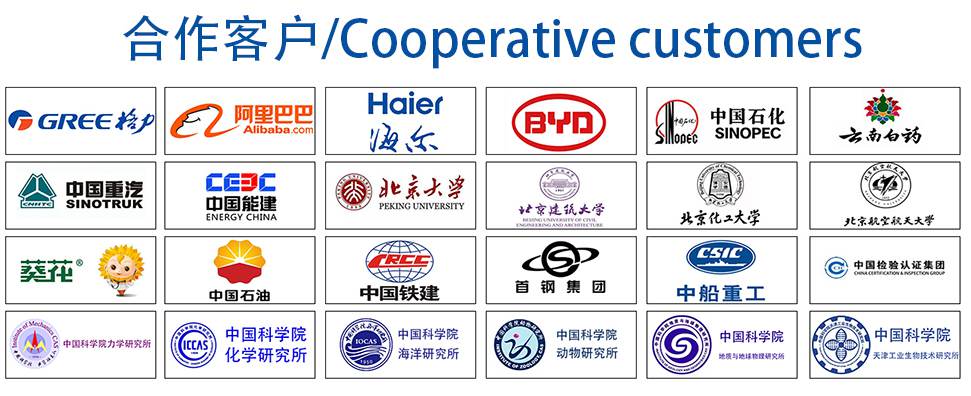