钢板制对焊管件检测的重要性与核心内容
钢板制对焊管件是工业管道系统中不可或缺的连接元件,广泛应用于石油、化工、电力、船舶等领域。其质量直接影响管道系统的安全性、密封性和使用寿命。为确保管件在高压、高温或腐蚀性介质环境下的可靠性,必须通过严格的检测程序验证其性能参数。检测范围涵盖原材料性能、制造工艺、焊接质量、尺寸精度及力学性能等多个维度,是保障管件符合国家标准(如GB/T 12459、ASME B16.9)和行业规范的核心环节。
关键检测项目及技术要点
1. 原材料化学成分与力学性能检测
通过光谱分析仪对钢板材料的C、Mn、Si、S、P等元素进行定量检测,确保符合GB/T 699或ASTM A106等标准要求。同时需进行拉伸试验(测定抗拉强度、屈服强度)和冲击试验(-20℃低温韧性),验证材料的力学性能是否满足承载需求。
2. 几何尺寸与形位公差检测
使用三维坐标测量仪、卡尺及焊缝量规等工具,对管件的内径、外径、壁厚、椭圆度、端面垂直度等参数进行精确测量。重点检查坡口角度(30°±2.5°)和钝边厚度(1.6±0.8mm),确保焊接装配精度。
3. 焊接接头质量评估
采用X射线探伤(RT)或超声波探伤(UT)对焊缝进行100%无损检测,识别未熔合、气孔、夹渣等缺陷。按NB/T 47013标准评定缺陷等级,Ⅱ级及以上为合格。硬度测试(HV10)用于验证热影响区硬度≤248HV,避免脆性断裂风险。
4. 表面质量与防腐性能测试
目视检查管件表面是否存在裂纹、折叠、重皮等缺陷,粗糙度需达到Ra≤12.5μm。通过盐雾试验(ASTM B117)评估镀锌层或涂层的耐腐蚀性,480小时无红锈为合格。漆膜厚度采用磁性测厚仪检测,误差需控制在±15μm以内。
5. 压力试验与气密性验证
依据GB/T 20801标准进行1.5倍设计压力的液压试验,保压时间≥10分钟,无渗漏或塑性变形。对于燃气管道管件,需额外进行0.6MPa气密性试验,采用发泡剂检测微泄漏点,泄漏率≤0.1%为合格。
现代化检测技术的应用
随着技术进步,工业CT扫描可对复杂结构管件进行三维缺陷重建,相控阵超声波检测(PAUT)可实现焊缝缺陷的精准定位。自动化测量机器人将尺寸检测效率提升40%以上,而大数据平台可对检测结果进行实时分析预警,显著提升质量控制水平。
通过上述系统性检测,可确保钢板制对焊管件满足强度、密封性及耐久性要求。企业需建立从原料入厂到成品出厂的全流程质量管控体系,并定期通过 认证实验室进行第三方复核,以降低工程风险,保障管道系统长期稳定运行。
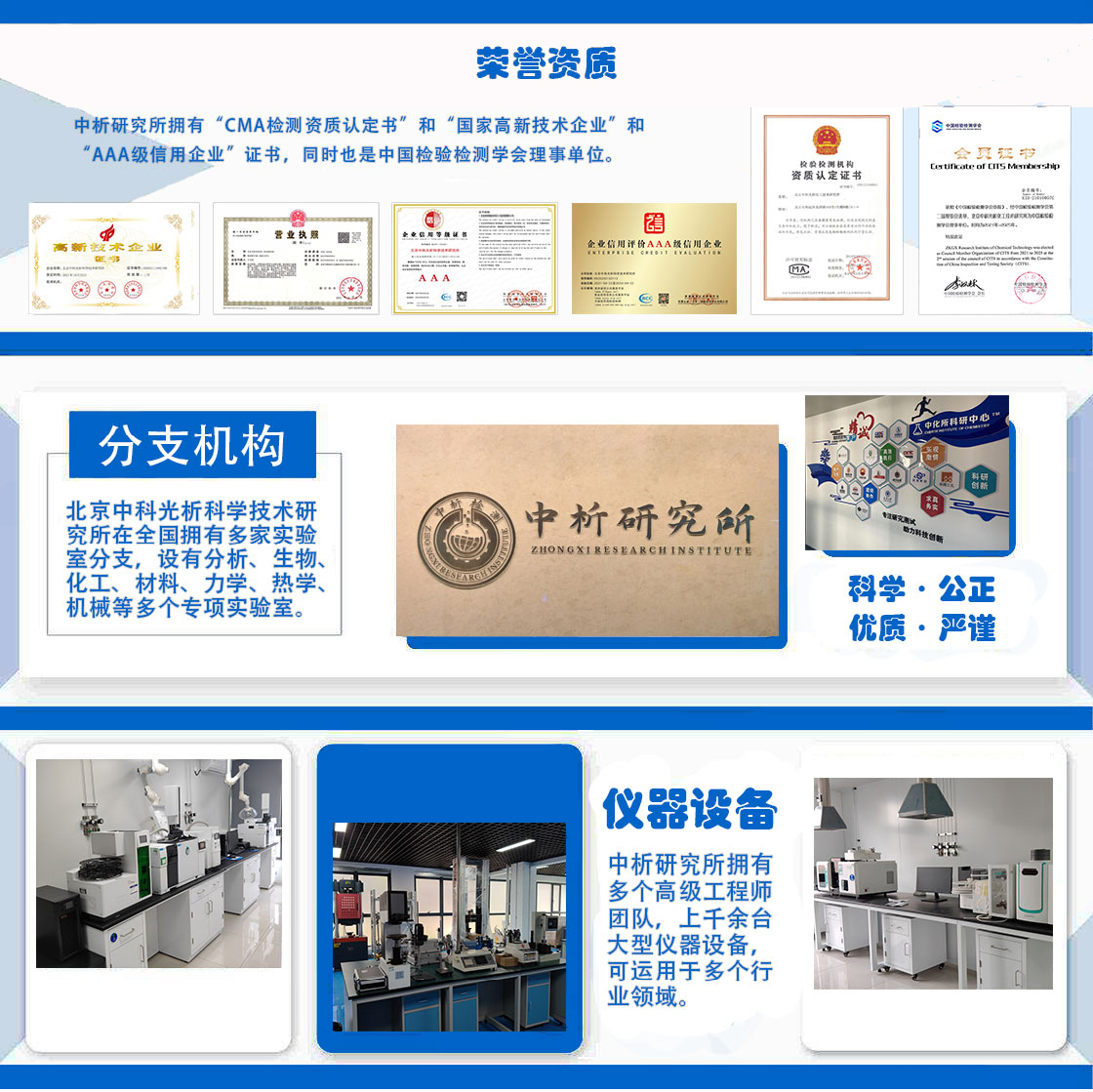
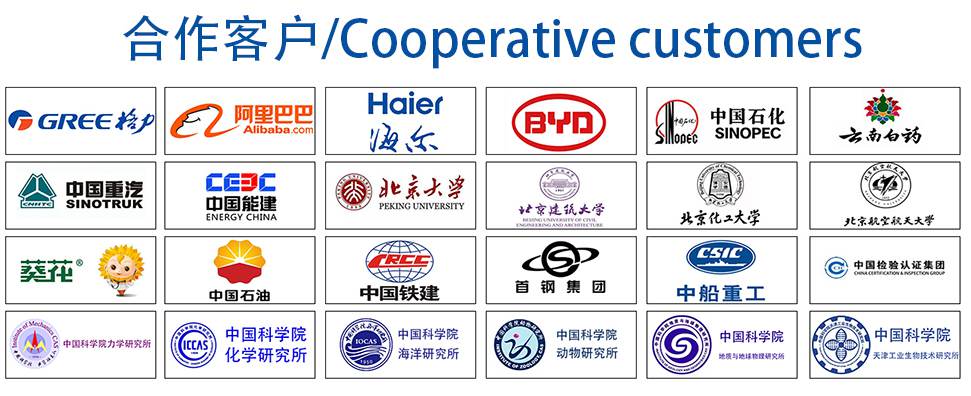