汽车电喇叭检测的重要性与核心项目解析
作为车辆安全警示系统的核心部件,汽车电喇叭的可靠性直接关系到行车安全与交通秩序。根据《GB 15742-2019 机动车用喇叭性能要求及试验方法》等国家标准,电喇叭需要通过严格的质量检测才能投入使用。检测过程不仅关注声音的清晰度和传播距离,还需验证其耐久性、环境适应性及电磁兼容性,确保在各种复杂工况下均能稳定工作。
核心检测项目与技术要点
1. 声学性能测试
使用声级计在距离喇叭正前方2m处测量声压级,A计权声级应达到90-118dB范围。同时通过频谱分析仪验证频率特性,要求基频误差不超过标称值的±10%。测试需在标准消声室或半消声室进行,避免环境噪声干扰。
2. 耐久性试验
模拟极端工作状态,以10秒工作/50秒休息的循环模式进行5万次连续触发测试。试验后需满足声压级衰减不超过5dB、音色无明显畸变的质量要求,验证触点材料和弹簧结构的可靠性。
3. 环境适应性检测
包含高低温交变试验(-40℃~80℃)、湿热试验(温度40℃/湿度95%)、盐雾腐蚀试验(5%NaCl溶液喷雾96小时)以及IPX5级防水测试,确保金属部件抗腐蚀能力和密封性能达标。
4. 电磁兼容性验证
通过传导骚扰和辐射骚扰测试(频率范围150kHz-2.5GHz),确保电喇叭工作时不会干扰车载电子设备,同时能承受ISO 7637标准规定的电压瞬态脉冲冲击。
5. 机械强度检测
包括振动试验(频率10-500Hz/加速度20m/s²)、冲击试验(半正弦波/峰值加速度300m/s²)以及喇叭膜片的疲劳测试,评估结构件在车辆行驶中的抗振能力。
常见失效模式与维护建议
检测数据显示,触点氧化(占比35%)、线圈烧蚀(28%)、膜片破裂(18%)是主要故障类型。建议车主定期清洁触点间隙(标准0.3-0.5mm),检查线束连接状态,并避免长时间连续鸣笛(单次不超过10秒)。
结语
专业的汽车电喇叭检测体系覆盖了从声学特性到环境耐受的全维度验证,为安全行车提供有力保障。建议车辆每行驶2万公里或每年进行1次专项检测,及时更换性能衰减超过15%的喇叭组件,确保警示效果符合法规要求。
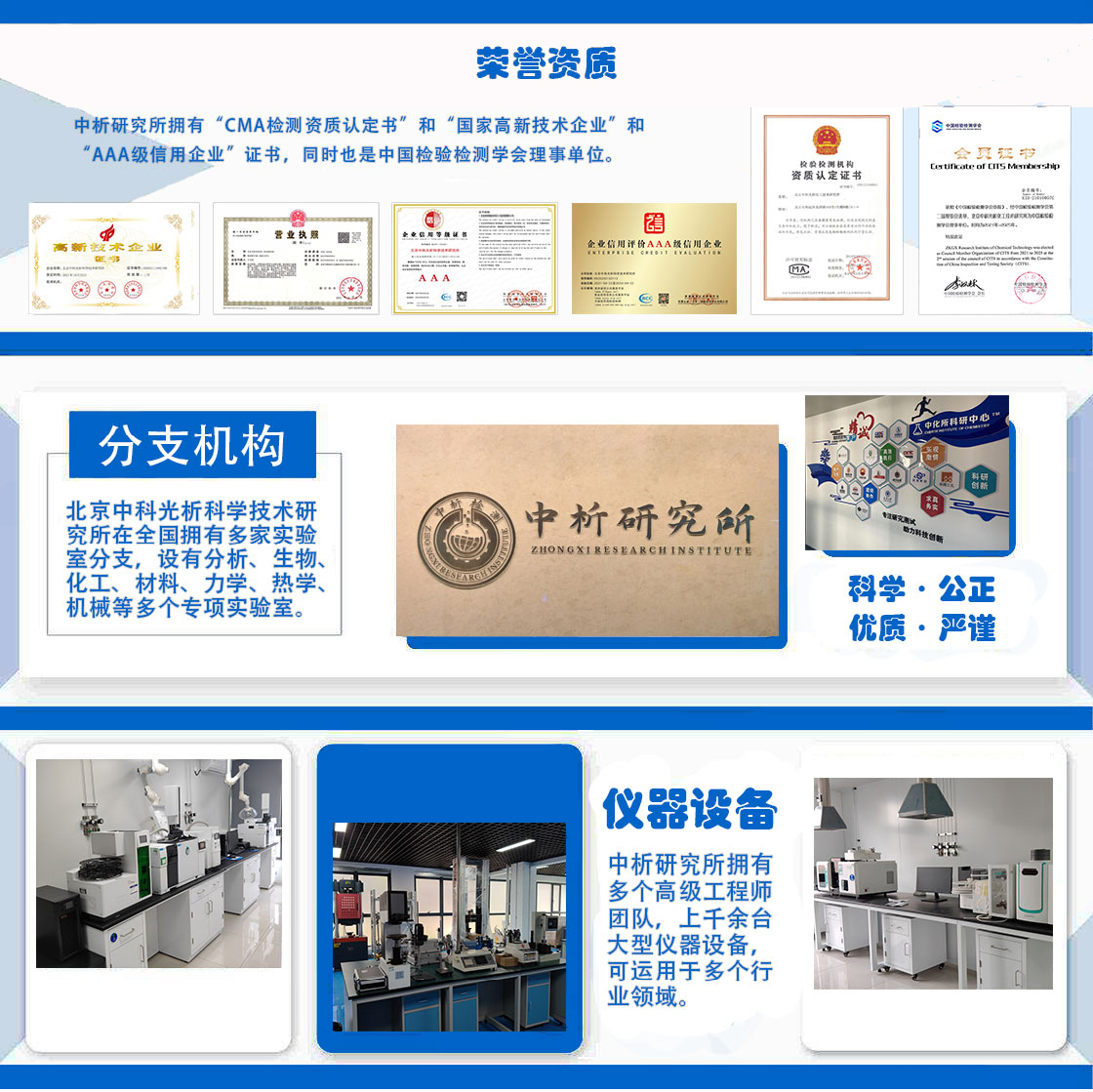
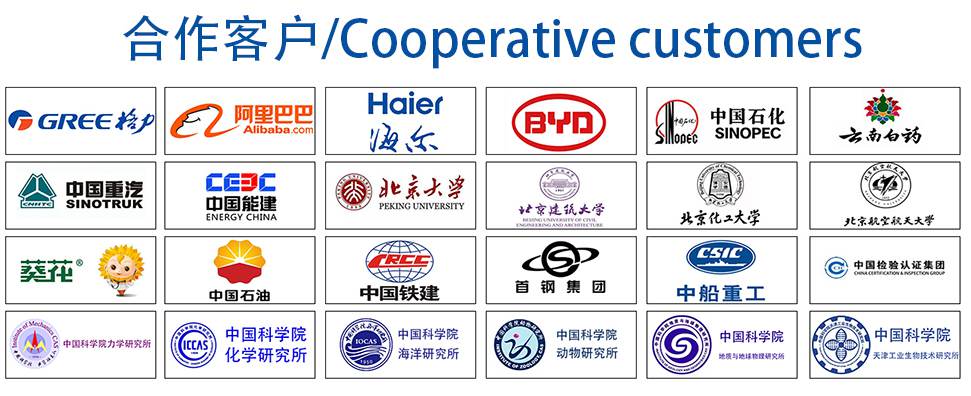