轧辊车床检测的重要性与流程
轧辊车床是冶金、机械制造等行业中用于加工轧辊类工件的关键设备,其精度直接影响轧辊的几何形状、表面质量和寿命。随着工业自动化水平的提升,轧辊车床的检测需求日益严格。通过系统性检测,可确保设备加工能力符合工艺要求,避免因设备误差导致的产品报废或生产事故。检测项目需覆盖机床的静态精度、动态性能、传动系统、液压系统及控制系统等核心模块,同时结合数字化测量技术实现高效、精准的评估。
轧辊车床核心检测项目
1. 几何精度检测
包括床身水平度、导轨直线度、主轴径向跳动和轴向窜动等指标。使用激光干涉仪、电子水平仪等工具测量导轨平行度误差,确保导轨在水平和垂直方向上的偏差不超过标准(通常≤0.02mm/m)。主轴的动态回转精度需通过锥形检具配合千分表进行测试,误差值应控制在0.005mm以内。
2. 传动系统稳定性检测
重点检查主轴齿轮箱、进给伺服电机的运行状态。通过振动传感器和噪声分析仪采集传动链的振动频谱,识别齿轮磨损、轴承松动等隐患。同时验证数控系统的反馈精度,例如丝杠反向间隙补偿是否准确,重复定位误差应≤±0.01mm。
3. 液压与冷却系统检测
液压系统的压力稳定性直接影响刀架夹紧力和切削液供给效果。需测试系统在负载变化下的压力波动(要求≤额定压力±5%),并检查油路密封性。冷却系统需评估喷嘴流量分布均匀性,防止因局部冷却不足导致的轧辊热变形。
4. 表面加工质量验证
通过试切标准试件(如阶梯轴)分析表面粗糙度(Ra值≤1.6μm)、圆度(公差≤0.01mm)和圆柱度等参数。使用白光干涉仪或轮廓仪对轧辊表面微观形貌进行三维扫描,识别波纹度异常或刀痕缺陷。
5. 安全防护与功能测试
包括急停装置响应速度、防护门联锁功能、过载保护触发阈值等安全项目。模拟典型故障(如超程、断刀)验证数控系统的报警逻辑和应急处理能力,确保符合GB/T 15760机械安全标准。
检测后的数据管理与优化建议
检测结果需生成详细报告,建立设备健康档案。对超差项进行溯源分析,例如导轨磨损可通过刮研修复,主轴轴承间隙异常需更换高精度角接触轴承。建议企业结合预测性维护技术,利用传感器实时监测关键参数,延长设备使用寿命,降低非计划停机风险。
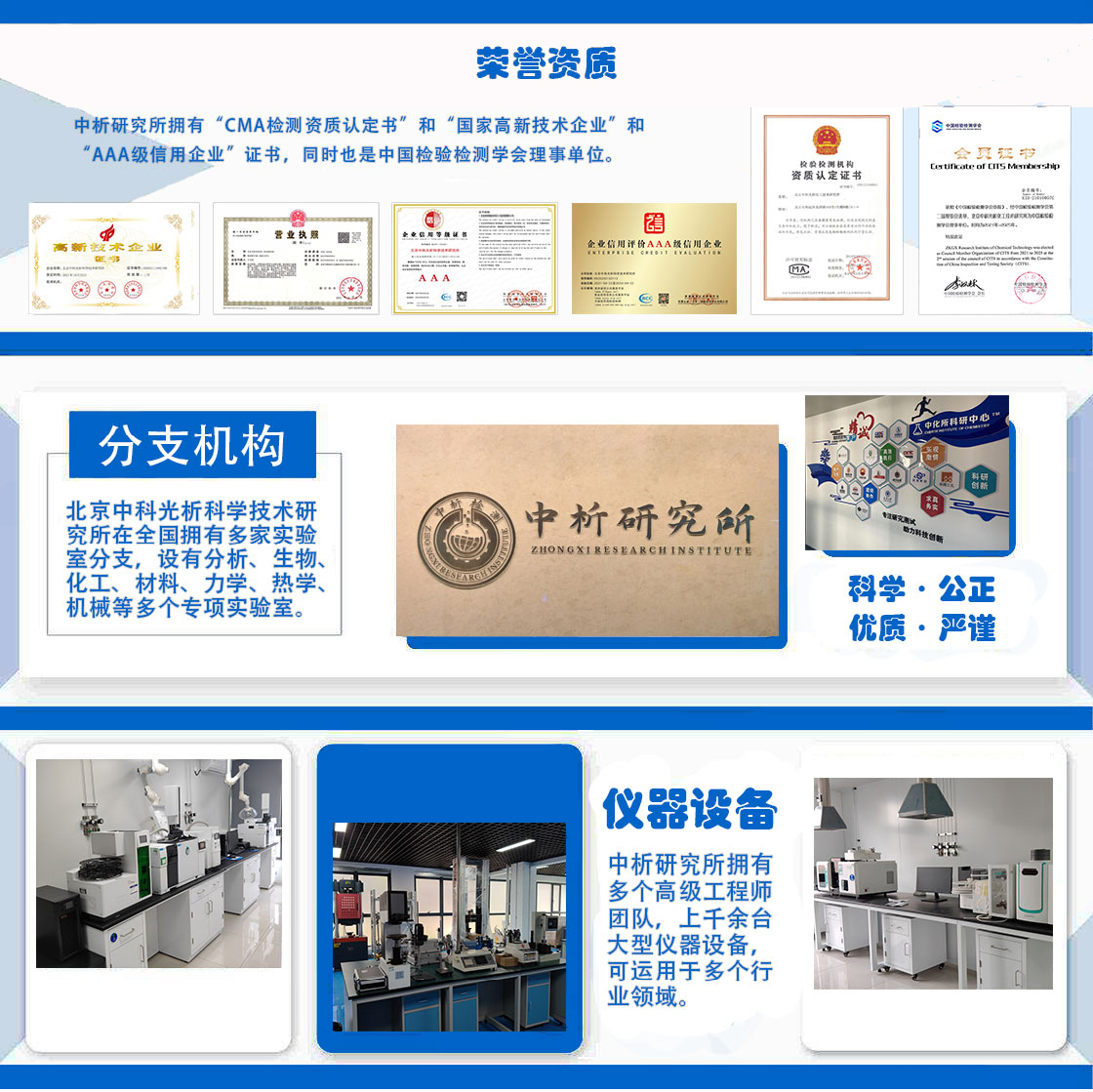
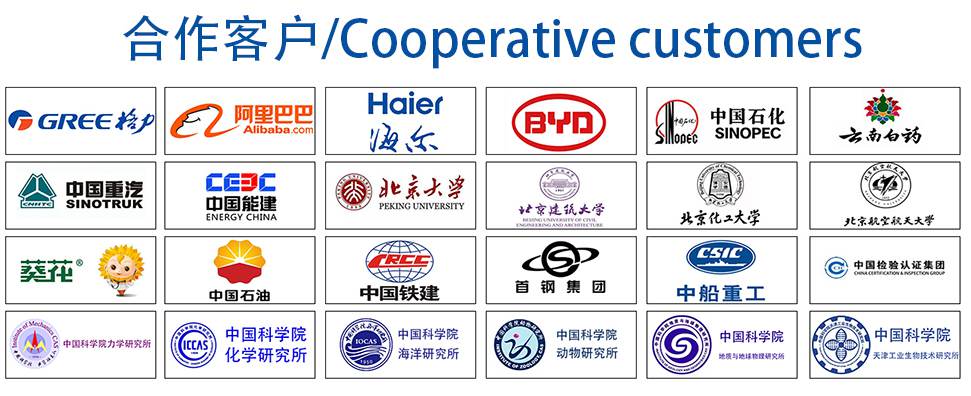