滚丝机检测项目及流程解析
滚丝机作为金属加工领域的重要设备,广泛用于螺纹成型、管材加工等场景。其运行精度直接影响产品合格率与工艺稳定性,因此定期开展系统性检测是保障生产质量、延长设备寿命的关键环节。本文将针对滚丝机的核心检测项目进行详细阐述,帮助用户建立科学的设备维护体系。
一、设备外观与结构检测
通过目视检查确认设备外罩、导轨、传动轴等部位是否存在划痕、锈蚀或变形,重点核查滚轮夹具的完整性。使用激光水平仪测量机身垂直度偏差是否在±0.1mm/m范围内,同时检查各紧固件扭矩值是否达到设备手册要求。
二、加工精度检测
采用螺纹规、三坐标测量仪对加工样件进行全尺寸检测,包括螺纹中径、螺距误差、牙型角偏差等参数。要求螺距累积误差不超过ISO 2级精度标准,滚轮径向跳动量需控制在0.02mm以内。同步检测主轴与尾座的同轴度,允许公差范围为φ0.03mm。
三、传动系统检测
使用振动分析仪监测齿轮箱运行状态,检查齿面磨损情况是否超出JIS B1704标准。通过红外测温仪记录轴承温升,连续运行2小时后温度不应超过环境温度+35℃。同步检测皮带张紧力,V型皮带挠度应保持在中心距的1.6%-2%区间。
四、液压与气压系统检测
使用压力表检测液压站工作压力稳定性,波动范围不得超过设定值的±5%。采用超声波检漏仪排查管路接头渗漏情况,油缸运动速度需符合25-40mm/s设计标准。对气动系统进行保压测试,5分钟内压力降不超过初始值的10%。
五、电气控制系统检测
使用万用表测量电机绝缘电阻值,要求≥5MΩ(500V兆欧表)。通过PLC诊断软件检查程序逻辑响应时间,信号延迟不得超过0.1秒。验证急停装置触发灵敏度,从按下按钮到完全停机应在0.5秒内完成。
六、润滑系统检测
拆解检查自动润滑泵供油量,单点注油量误差需≤±10%。使用污染度检测仪分析润滑油清洁度,NAS等级需达到8级以下。检查油路分配器是否堵塞,要求各润滑点油膜覆盖率≥95%。
七、安全防护装置检测
验证光电保护装置的响应距离与遮挡灵敏度,触发时间应≤20ms。检查防护罩联锁装置功能有效性,开盖断电响应时间需≤0.2秒。使用分贝计测量设备运行噪声,连续工作状态下不得超出85dB(A)。
八、综合性能测试
在额定负载下进行50件连续加工测试,统计成品合格率(要求≥98%)。记录设备温升曲线,各部件温度均需处于安全阈值内。通过功率分析仪监测能耗指标,空载功耗不应超过额定功率的15%。
完整检测周期建议每500小时或每季度进行一次,关键参数应建立动态监测数据库。通过实施标准化检测流程,可使滚丝机故障率降低40%以上,同时提升15%-20%的生产效率。
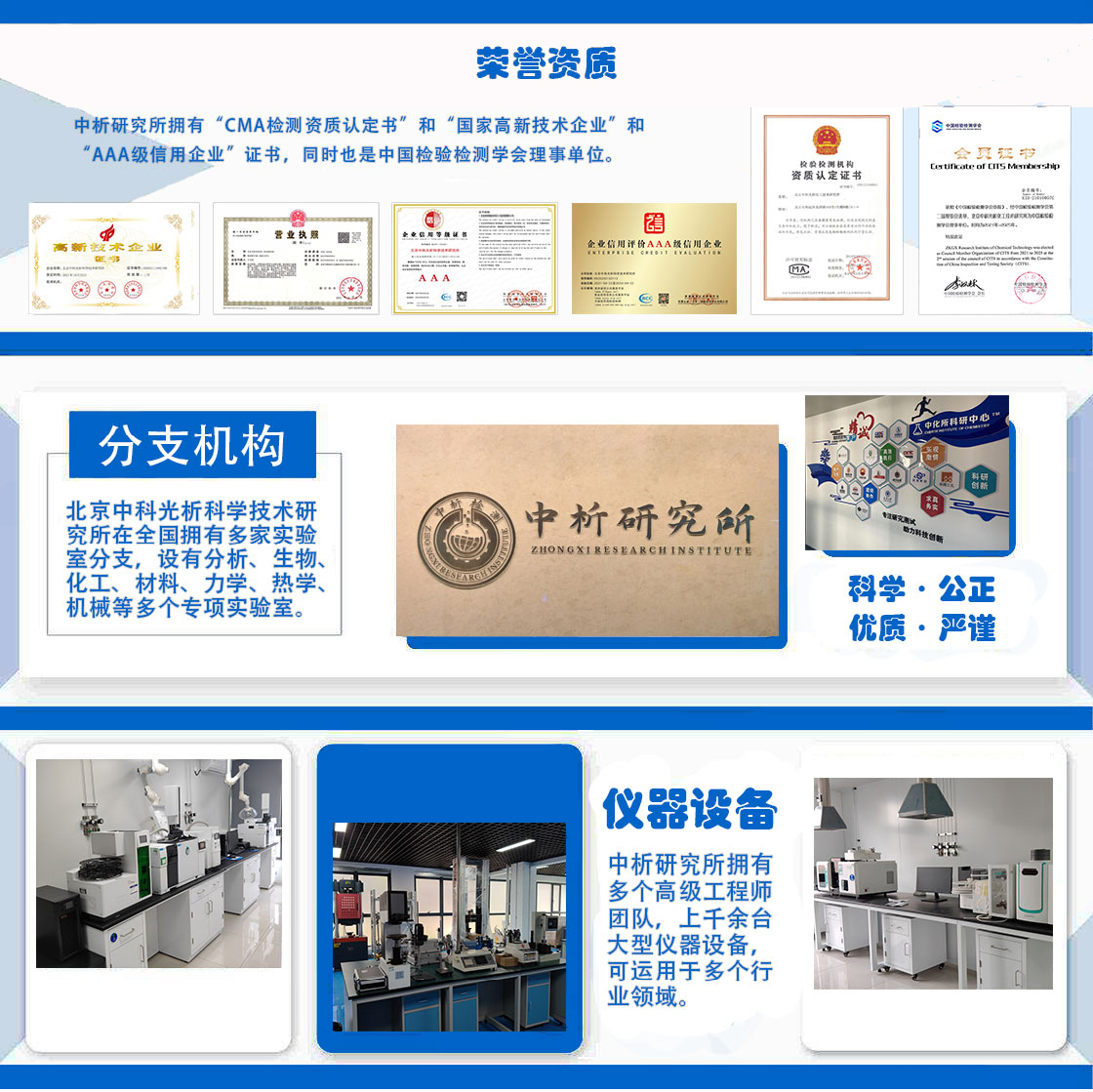
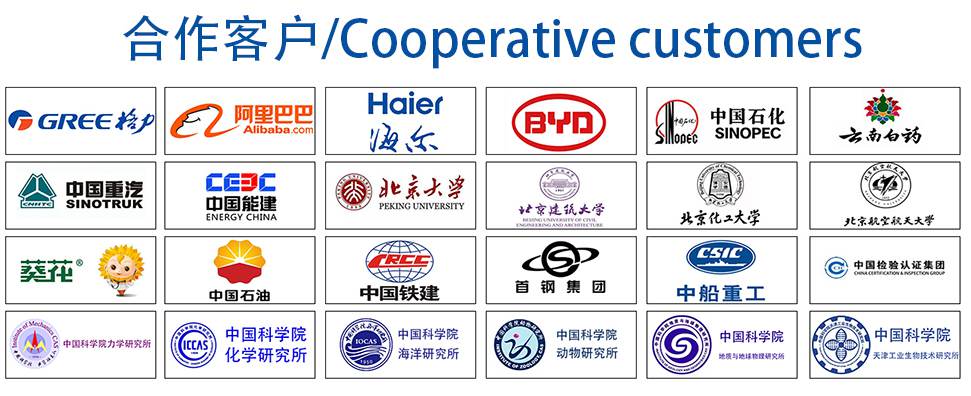