铝中间合金检测的重要性及核心检测项目
铝中间合金作为铝合金生产的关键原料,其质量直接影响最终合金的力学性能、耐腐蚀性及加工特性。这类合金通常由铝与一种或多种过渡金属(如钛、锆、硼等)组成,广泛应用于航空航天、汽车制造、电子封装等领域。为保证合金熔炼过程的稳定性及成品质量,需通过专业检测手段对铝中间合金的成分、组织及杂质进行系统分析。国际通用的GB/T 27677-2011《铝中间合金》标准明确了具体的检测要求,本文将重点解析铝中间合金检测的核心项目及其实践意义。
一、化学成分分析
采用电感耦合等离子体光谱仪(ICP-OES)和X射线荧光光谱仪(XRF)对合金主元素(Al、Ti、Zr等)及微量杂质(Fe、Si、Cu等)进行定量检测。需特别关注活性元素的含量波动,如钛含量偏差±0.2%即可能影响晶粒细化效果。
二、金相组织检测
通过电子探针显微分析(EPMA)观察金属间化合物的分布形态,结合扫描电镜(SEM)评估第二相粒子的尺寸和弥散度。优质中间合金应呈现均匀的Al3Ti或AlB2相分布,避免出现粗大的团聚组织。
三、粒度分布测试
应用激光粒度仪测定合金粉末或破碎料的粒径分布,D50值需控制在50-150μm范围。粒度均匀性直接影响熔体吸收效率,过度细粉易导致氧化烧损,粗颗粒则易出现溶解不充分。
四、气体含量检测
采用熔融法氢分析仪检测氢含量(标准值≤0.15mL/100g),惰性气体熔融法测定氧含量(≤0.03%)。高气体含量会显著增加铸件气孔缺陷率,需结合真空熔炼工艺进行控制。
五、表面质量检测
通过工业内窥镜观察锭坯表面氧化膜厚度,使用涡流检测仪排查皮下裂纹。对于线材产品需进行表面粗糙度测试(Ra≤1.6μm),确保后续加工过程的送料稳定性。
六、力学性能验证
对铸态试样进行三点弯曲试验,检测断裂延伸率(≥8%)和抗弯强度(≥120MPa)。通过显微硬度计(HV标尺)测定基体硬度波动范围(60-80HV),评估合金强化效果。
七、夹杂物分析
采用电解分离法提取非金属夹杂物,通过EDS能谱分析确定夹杂成分。重点关注Al2O3和SiO2类硬质颗粒的含量(≤0.05%),该类夹杂物会显著降低材料的疲劳强度。
通过以上系统检测,可全面评估铝中间合金的工艺适用性和质量可靠性。现代检测实验室普遍采用ASTM B928、ISO 209等国际标准方法,结合智能检测系统实现数据自动采集与分析,为铝合金产业链的质量控制提供科学依据。
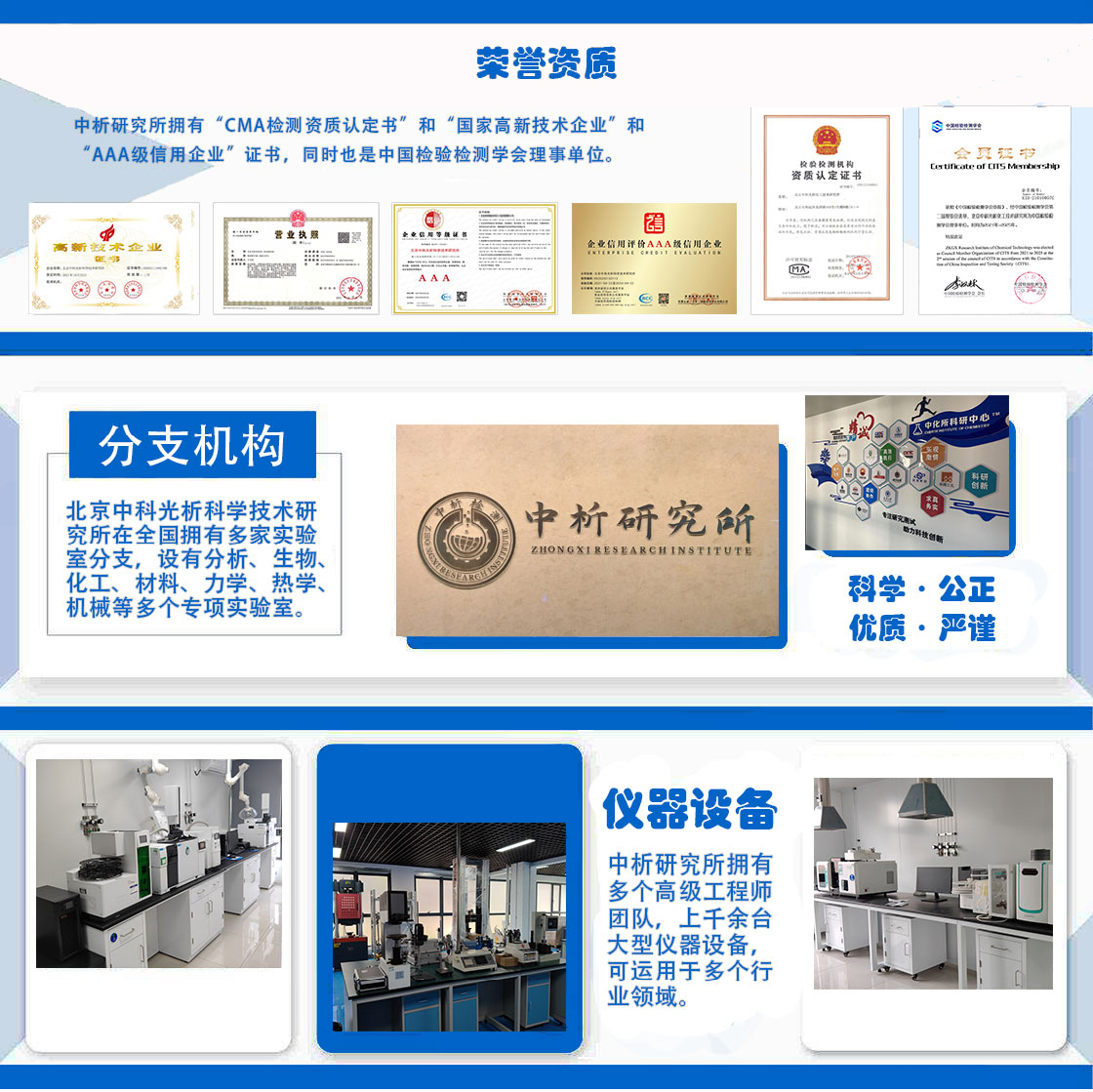
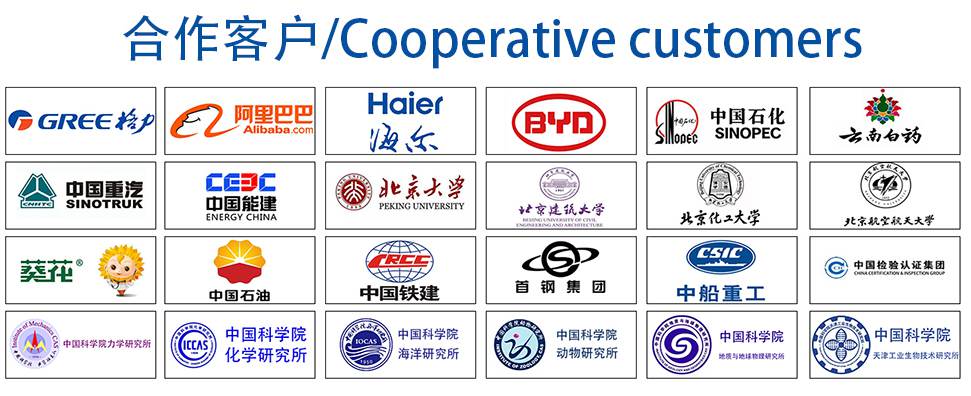