船用铝合金板材检测的重要性
船用铝合金板材因其轻量化、高强度、耐腐蚀等特性,在船舶制造中扮演着重要角色。然而,船舶长期处于高盐、高湿、复杂载荷的恶劣环境,对材料的性能提出极高要求。为确保航行安全和结构可靠性,必须对铝合金板材进行系统性检测。这不仅涉及材料的化学成分和力学性能,还需关注其加工工艺、焊接质量及耐腐蚀能力。通过科学严谨的检测手段,能够提前发现潜在缺陷,避免因材料失效引发的安全事故,同时为船舶轻量化设计提供可靠数据支撑。
1. 材料成分分析
铝合金板材的化学成分直接影响其物理性能和耐腐蚀性。检测时需通过光谱分析仪(如ICP-OES)精确测定铝、镁、硅、铜等主元素含量,并严格控制杂质元素(如铁、锌)的比例。例如,船用5083铝合金的镁含量需在4.0%-4.9%范围内,确保其在海洋环境中的抗应力腐蚀能力。
2. 力学性能测试
包括拉伸试验、硬度测试和弯曲试验: - 拉伸试验:测定板材的抗拉强度、屈服强度和延伸率,需符合ISO 6892标准; - 维氏硬度测试(HV):评估材料表面硬度均匀性; - 弯曲试验:验证板材在冷加工时的延展性,避免出现裂痕或分层。
3. 耐腐蚀性能评估
通过盐雾试验(ASTM B117)模拟海洋环境,连续喷洒5%氯化钠溶液,观察72小时后的腐蚀速率。同时需进行电偶腐蚀测试,验证板材与其他船体材料(如钢构件)接触时的电化学兼容性。微观组织分析(金相显微镜)可进一步检测晶间腐蚀倾向。
4. 尺寸与形位公差检测
使用激光扫描仪或三坐标测量机(CMM)检查板材厚度偏差(通常要求≤±0.1mm)、平面度(≤1.5mm/m)及边缘直线度。对于大尺寸板材,需分段测量并采用多点校准法,确保装配时的接缝精度。
5. 焊接接头质量检验
针对焊接区域的检测包括: - 宏观/微观金相分析:观察熔深、气孔、夹渣等缺陷; - 超声波探伤(UT):探测内部未熔合或裂纹; - 显微硬度测试:评估热影响区硬度变化,避免软化导致强度下降。
6. 无损检测技术应用
采用X射线检测(RT)识别板材内部的缩孔、夹杂物;涡流检测(ET)用于快速筛查表面裂纹;相控阵超声(PAUT)可对厚板进行分层扫描,检测深度达50mm以上的内部缺陷。
7. 表面处理质量验证
检查阳极氧化层厚度(20-25μm)、涂层附着力(划格法测试)及防污涂层的均匀性。使用涡流测厚仪确保防腐涂层符合IMO PSPC标准要求。
船用铝合金板材的检测需贯穿材料生产、加工到装配的全流程,结合齐全仪器与严格标准,构建多维度质量管控体系。通过精准的检测数据,可优化材料选型、提升船舶建造效率,并显著延长船舶服役寿命,为海洋装备的可持续发展提供技术保障。
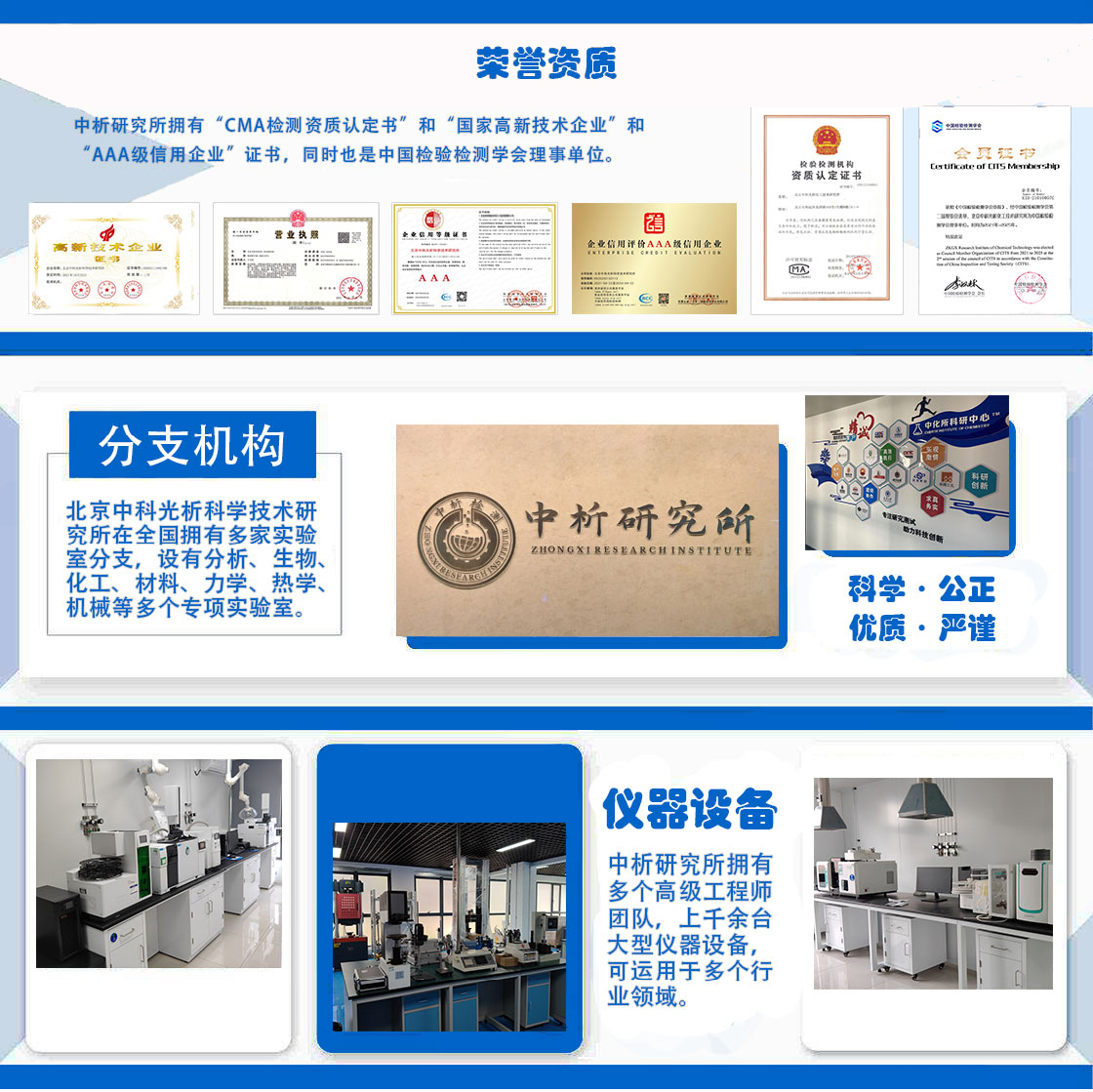
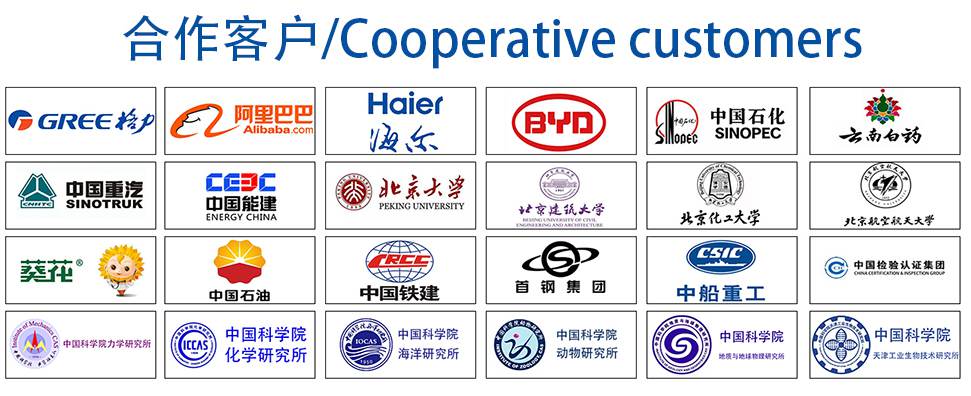