钻削加工中心检测项目全解析
钻削加工中心作为现代精密制造的核心设备,其加工精度、动态性能和系统稳定性直接决定产品质量。随着工业4.0对加工精度要求的提升,定期开展系统性检测已成为保障设备性能、延长使用寿命的必要手段。检测过程需覆盖几何精度、动态特性、主轴系统、控制系统等关键维度,通过定量数据分析实现设备状态的精准诊断。
一、几何精度检测
1. 床身水平度检测:使用电子水平仪测量X/Y/Z轴向水平偏差,要求全行程误差≤0.02mm/m
2. 主轴垂直度验证:采用精密角尺配合千分表,测量主轴与工作台面的垂直度,允差范围±0.005mm/300mm
3. 定位精度检测:通过激光干涉仪测量各轴定位精度,ISO标准要求重复定位精度≤±3μm
4. 工作台平面度检测:使用电子平尺配合测微仪,平面度偏差需控制在0.012mm/m²内
二、动态性能测试
1. 伺服系统响应特性:利用动态测试仪分析加速度曲线,检测超调量是否超过设定值的15%
2. 振动频谱分析:通过加速度传感器采集主轴800-12000rpm范围内的振动峰值,要求最大振幅≤5μm
3. 热变形监控:在连续加工4小时后,测量主轴延伸量变化,温升引起的变形应≤0.008mm
三、主轴系统专项检测
1. 主轴径向跳动量:使用三点接触式测微仪测量,高速主轴(≥15000rpm)要求跳动≤0.003mm
2. 扭矩输出特性:通过扭矩传感器验证主轴在不同转速下的扭矩曲线是否符合标称值
3. 换刀机构测试:模拟2000次自动换刀,记录平均换刀时间和位置重复精度(应≤±0.005mm)
四、控制系统与软件验证
1. 插补精度检测:执行圆形/螺旋测试程序,使用球杆仪分析轮廓精度误差≤0.015mm
2. 数据通信稳定性:连续运行72小时G代码传输,监测数据包丢失率应<0.001%
3. 安全保护功能验证:包括超程保护、刀具破损检测响应时间(≤0.1秒)等28项安全检测
通过系统化的检测流程,企业可建立完整的设备健康档案。建议每500工作小时进行基础检测,2000小时实施全面校准。检测数据应采用SPC统计分析方法,实现加工中心性能的预测性维护,确保设备始终处于最佳加工状态。
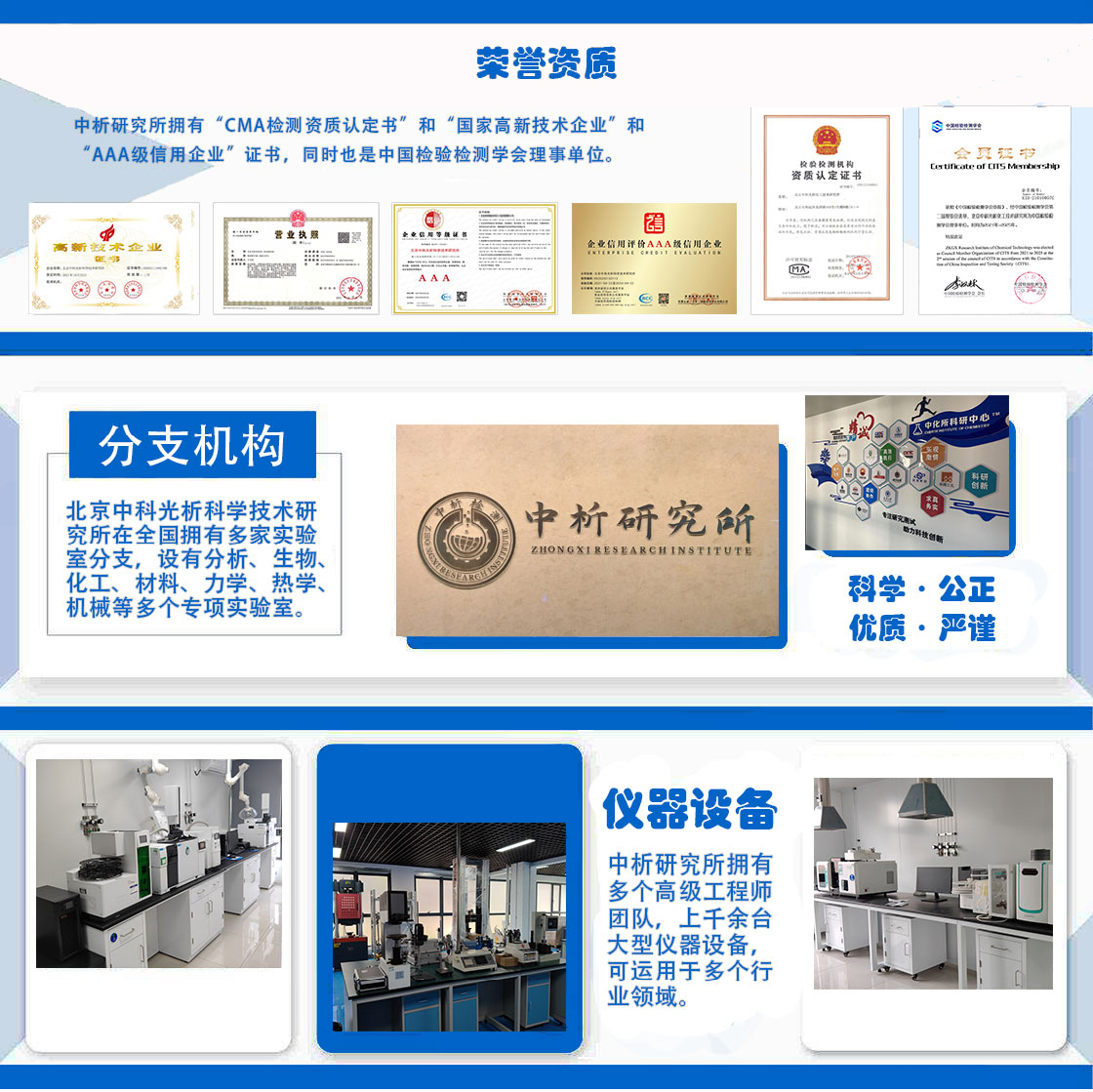
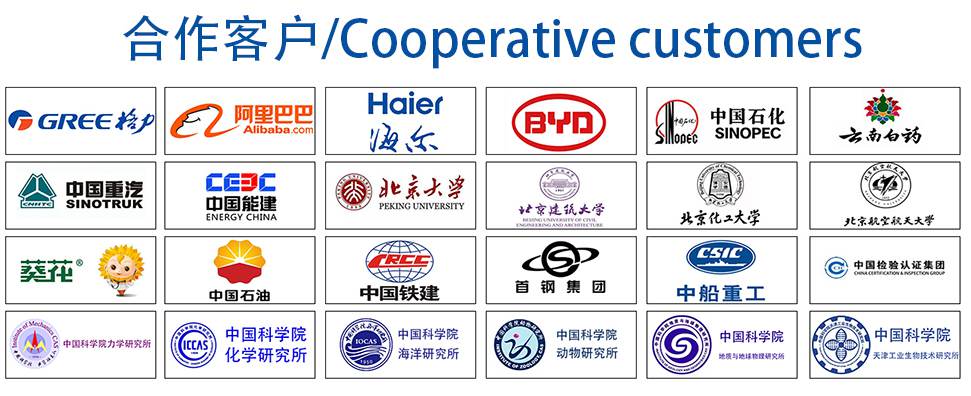