铁路货车用铝合金板材检测的重要性
随着铁路货运向高速化、重载化方向发展,铝合金板材凭借其轻量化、高强度、耐腐蚀等特性,已成为铁路货车车体制造的核心材料。然而,铝合金板材在生产、加工和使用过程中可能因工艺波动、环境因素或应力作用产生缺陷,直接影响车辆的安全性和使用寿命。因此,建立系统化的检测体系对保障铁路货车运行安全、延长零部件服役周期具有重大意义。国家铁路局颁布的《铁路货车用铝合金板材技术条件》等标准文件,明确要求对材料性能、尺寸精度、表面质量等关键指标实施全流程监控。
核心检测项目与技术要求
1. 材料性能检测
通过万能试验机进行拉伸试验,测定抗拉强度(≥320MPa)、屈服强度(≥250MPa)和延伸率(≥8%),验证板材是否满足GB/T 228.1标准要求。冲击试验采用夏比V型缺口试样,在-40℃低温环境下测试冲击吸收能量(≥15J)。耐腐蚀性测试包含96小时中性盐雾试验和晶间腐蚀试验,观察表面腐蚀等级及金相组织变化。
2. 尺寸精度检测
使用激光测距仪和三维坐标测量仪对板材厚度(公差±0.15mm)、宽度(公差±2mm)、平直度(≤1.5mm/m)进行检测。重点控制焊接区域板厚减薄量,要求最大减薄率不超过标称厚度的8%。对角线偏差需控制在3mm/m范围内,确保装配精度。
3. 表面质量检测
依据GB/T 3199标准,采用目视检查配合表面粗糙度仪(Ra≤3.2μm),排查划痕、起皮、气泡等缺陷。氧化膜厚度检测使用涡流测厚仪,要求阳极氧化膜厚10-25μm,涂层附着力测试通过划格法验证(0级为合格)。
4. 化学成分分析
采用直读光谱仪对Al-Mg-Si系合金中各元素含量进行精确测定,重点控制Mg(0.6-1.2%)、Si(0.4-1.0%)、Fe(≤0.35%)等主成分,同时监测Cu、Zn等杂质元素含量,确保符合GB/T 3190规定。
5. 无损检测技术应用
对焊接接头实施100%超声波探伤(UT),探头频率选用2-5MHz,检出≥Φ2mm缺陷。渗透检测(PT)用于发现表面开口缺陷,着色渗透剂显像时间控制在10-30分钟。TOFD技术用于厚板内部缺陷三维定位,检测灵敏度达1mm当量直径。
6. 疲劳性能验证
通过高频疲劳试验机模拟车辆振动载荷,实施10^7次循环载荷试验(应力比R=0.1),监测裂纹萌生周期。断口分析采用扫描电镜(SEM)观察疲劳辉纹特征,建立S-N曲线评估材料耐久性。
检测技术创新趋势
当前检测技术正向智能化、数字化方向演进,工业CT可实现板材内部缺陷三维重构,相控阵超声检测系统可自动生成C扫描图像。基于机器视觉的表面检测系统检测速度可达3m/s,缺陷识别准确率超过98%。大数据平台的应用使检测数据与生产工艺形成闭环反馈,持续优化材料性能。
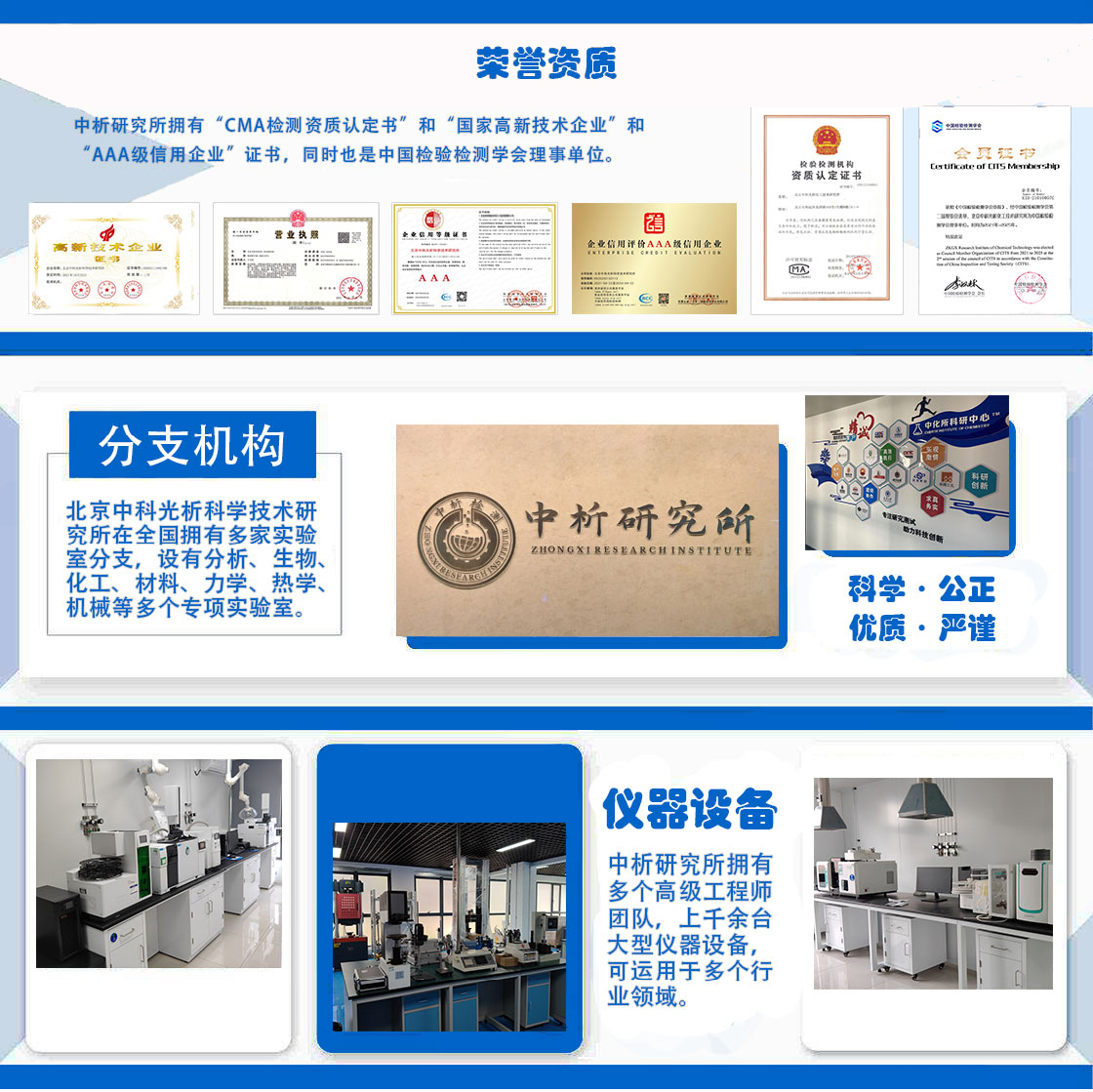
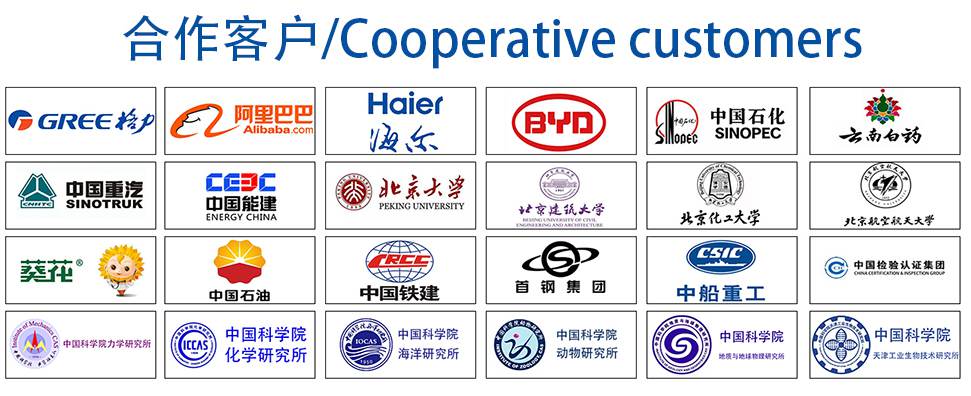