凸轮轴作为发动机核心部件之一,其加工精度直接影响发动机性能与使用寿命。凸轮轴磨床作为精加工设备,需要定期进行系统性检测,以确保其机械精度、加工稳定性和工艺参数符合技术要求。随着智能制造的发展,检测项目已从传统机械精度检查延伸至数字化控制系统的校准与动态性能分析,这对保障批量生产质量、降低设备故障率具有重要意义。
一、主轴系统精度检测
使用激光干涉仪检测主轴径向跳动和轴向窜动量,要求径向圆跳动≤0.003mm,轴向窜动≤0.005mm。同步检测主轴转速稳定性,在额定转速下波动幅度不得超过±1%。
二、砂轮架动态平衡测试
通过动平衡仪测量砂轮旋转时的振动值,ISO标准规定线速度≥45m/s时振动速度应<2.8mm/s。检测包含砂轮轴锥度配合精度及法兰盘安装的同轴度误差(≤0.01mm)。
三、进给系统定位精度验证
采用光栅尺或激光测距仪检测X/Z轴重复定位精度,要求±0.002mm/300mm行程。同步测试滚珠丝杠反向间隙,超过0.005mm需进行预紧力调整。
四、热变形补偿功能检测
连续运转4小时后,用激光跟踪仪测量机床热变形量。重点检测主轴箱垂直方向热位移(≤0.015mm)和砂轮架水平偏移量(≤0.01mm),验证温度传感器补偿系统的响应精度。
五、加工试件综合精度测试
通过标准试件加工验证:①凸轮桃形升程误差≤±0.01mm ②相位角偏差<15' ③表面粗糙度Ra≤0.4μm。使用轮廓仪进行三维形貌分析,检测波纹度(Wt≤0.8μm)和圆度误差。
六、数控系统功能诊断
检测内容包括:①伺服驱动器响应特性 ②PLC逻辑控制时序 ③人机界面参数设置完整性 ④数据采集系统采样频率(≥1kHz)。通过模拟加工测试各轴联动插补精度。
检测流程及注意事项
建议按照"机械精度→电气系统→动态性能→加工验证"的递进顺序实施检测。检测前需进行4小时以上热机运行,环境温度控制在20±2℃,避免振动干扰。每次检测后应建立设备精度档案,采用趋势分析法预判关键部件磨损状态。
通过实施系统性检测,可使凸轮轴磨床加工CPK值稳定在1.33以上,同时降低30%以上的非计划性停机时间。随着在线监测技术的应用,未来检测将向实时化和智能化方向发展。
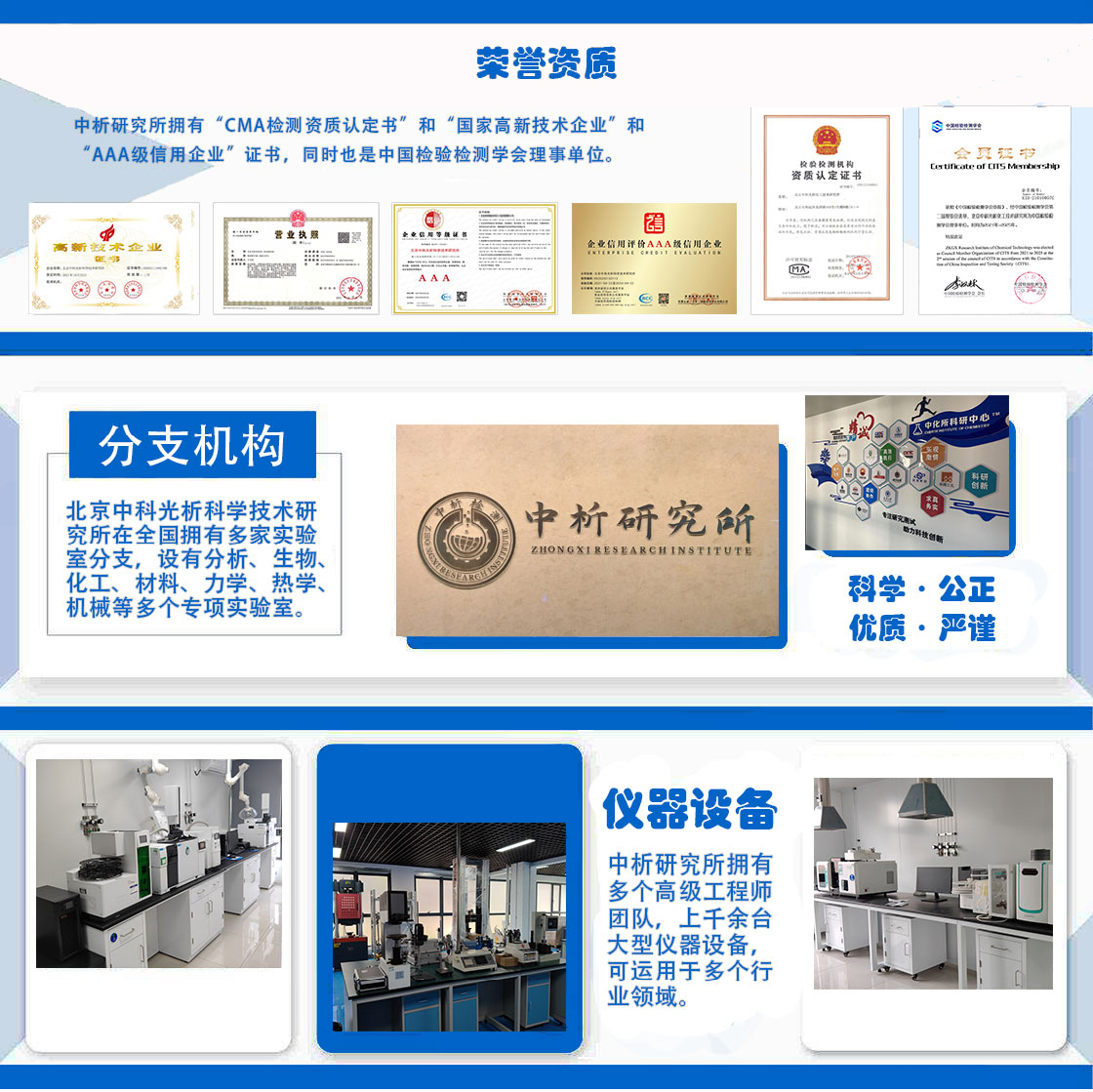
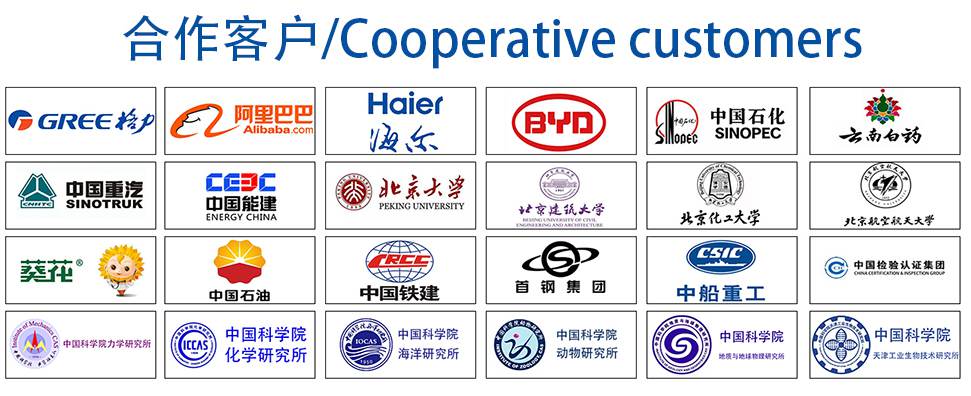