角接触球轴承检测的必要性与重要性
角接触球轴承作为精密机械传动系统的核心部件,广泛应用于机床主轴、汽车变速箱、航空航天设备等高精度场景。其独特的接触角设计(通常为15°-40°)可同时承受径向和轴向载荷,但这也对轴承的制造精度、材料性能和装配质量提出了更高要求。在工业4.0背景下,完善的检测体系已成为保障轴承性能稳定性、延长使用寿命(通常达10万小时以上)及预防设备故障的关键环节。从原材料入厂到成品交付,需经历尺寸公差检测(如内径公差±0.0025mm)、表面粗糙度检测(Ra≤0.1μm)等20余项专业测试。
核心检测项目体系
1. 几何精度检测
使用三坐标测量仪(CMM)对轴承内径(ID)、外径(OD)、宽度(B)进行微米级测量,其中内径公差需控制在ISO P5级(±2.5μm)。接触角偏差必须≤0.5°,保持架窗口对称度误差≤0.03mm,确保载荷均匀分布。
2. 旋转性能测试
在专用试验机上模拟实际工况:转速可达20000rpm时,温升需≤35℃;振动值按ABEC-7标准需<20dB。同时检测启动力矩(≤0.05N·m)和运行扭矩波动,异常波动可能预示滚道椭圆度超标或保持架变形。
3. 材料与热处理分析
采用光谱仪检测GCr15轴承钢成分(Cr:1.45%-1.75%),金相显微镜观察马氏体组织(硬度HRC61-65),碳化物网状级别≤2级。X射线应力分析确保残余应力<200MPa,避免过早疲劳失效。
4. 动态承载能力验证
通过L10寿命试验(90%可靠度)验证额定动载荷,例如7014AC轴承需承受23kN径向载荷连续运转500小时无异常。采用声发射技术实时监测微点蚀情况,早期损伤识别精度达0.1mm²。
5. 特殊工况适应性检测
针对高温(150℃)、真空(10⁻³Pa)或腐蚀环境,进行72小时持续试验。润滑剂保持率需>85%,密封件泄漏量<0.01g/h。航空轴承还需通过GJB150标准下的三轴振动(5-2000Hz)测试。
智能化检测技术发展
基于工业AI的视觉检测系统可实现0.005mm级缺陷识别,在线监测系统采样频率达100kHz,可捕捉μs级异常信号。数字孪生技术将检测数据与仿真模型结合,实现故障预测准确率>92%。这些进步推动角接触球轴承检测进入智能闭环控制新阶段。
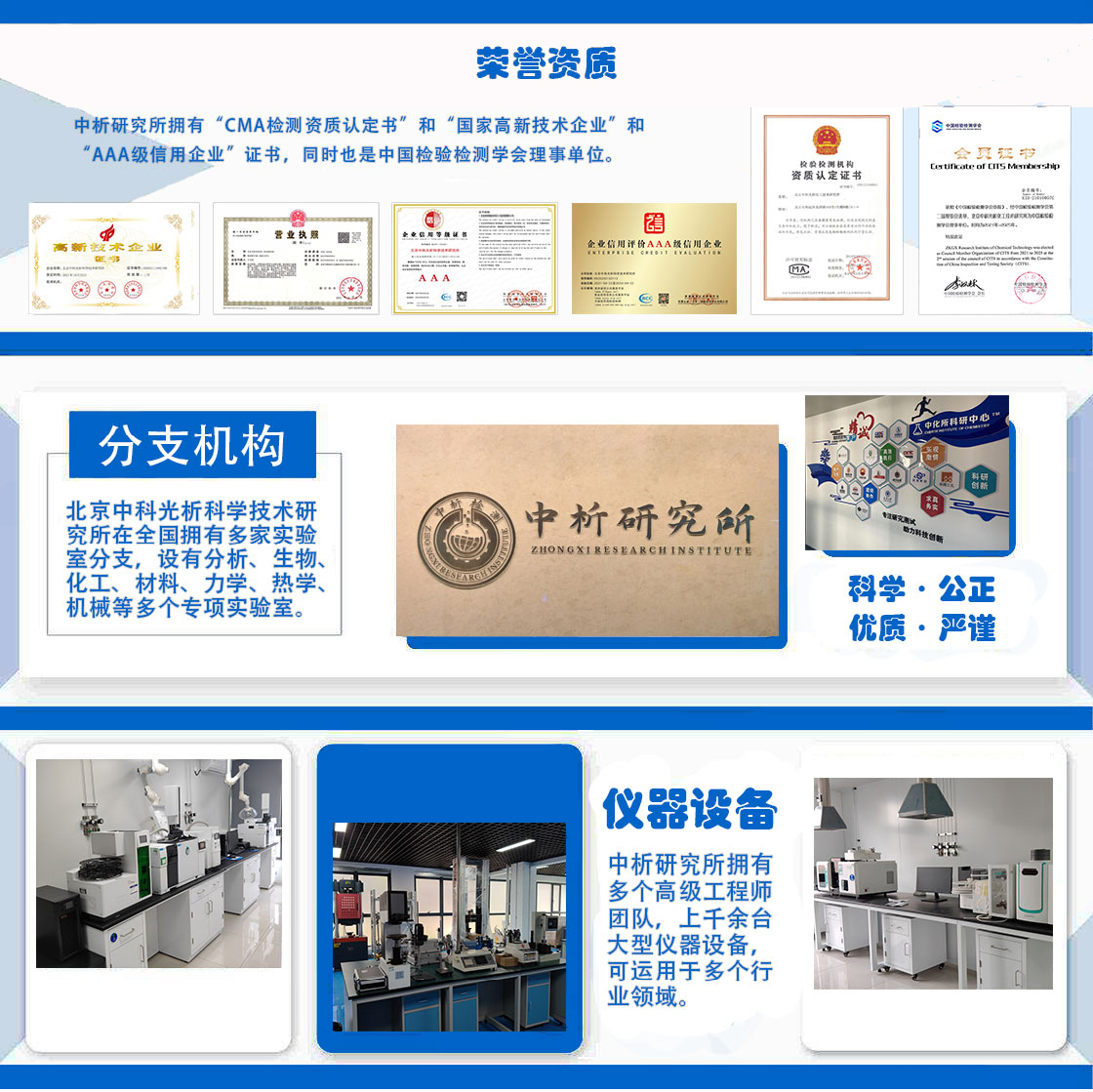
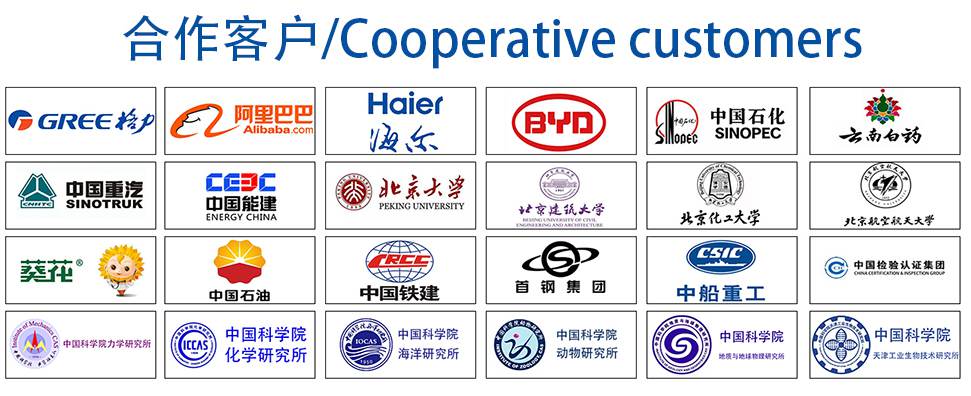