高精度加工中心检测项目解析
在高端制造业中,高精度加工中心作为核心生产设备,其性能直接决定了零部件的加工质量与生产效率。随着航空航天、精密模具、医疗器械等领域对零件精度要求的日益严苛(公差普遍要求±0.001mm级),建立科学的检测体系已成为保障设备稳定性的关键环节。通过系统性检测不仅能验证设备初始精度,更能通过周期性监测预警潜在故障,避免因设备偏差造成的批量报废损失。
一、几何精度检测体系
采用激光干涉仪配合电子水平仪,对X/Y/Z轴直线度、垂直度及重复定位精度进行三维空间校准,重点核查主轴端面跳动(需≤0.002mm)和径向圆跳动误差。通过球杆仪测试快速诊断滚珠丝杠反向间隙与圆周轮廓精度,结合花岗岩平台验证工作台平面度达标情况。
二、动态性能评估方案
通过加速度传感器监测各轴加减速过程中的振动频谱,利用主轴动态平衡仪检测20000rpm高速运转时的振动值(应控制在ISO标准G1.0级)。采用高帧率工业相机捕捉刀具换刀轨迹,验证ATC系统定位重复性误差是否满足±0.005mm要求。
三、温度补偿系统验证
构建热变形实验环境,在连续8小时加工周期内监测主轴温升曲线与热位移量。通过布置在床身、立柱等关键位置的温度传感器阵列,验证热误差补偿算法的有效性。要求温度波动±2℃时,定位精度偏差不超过补偿系统设计值的30%。
四、刀具系统精度检测
使用3D对刀仪检测刀柄锥面接触面积(需≥85%),配合气动测头验证刀具夹持重复精度。针对HSK刀柄执行拉刀力监测(标准值18-22kN),并采用频闪仪观察高速旋转刀具的径向偏摆情况。
五、数控系统功能验证
通过正弦曲线插补测试各轴动态响应特性,利用圆度测试程序检验圆弧插补精度。重点验证纳米级分辨率光栅尺的闭环控制效果,测试前瞻控制功能在微小线段加工中的轨迹平滑度,确保程序段处理时间≤0.5ms。
六、自动化在线检测集成
在加工单元集成触发式测头与激光对刀系统,建立加工-测量-补偿闭环体系。通过智能分析软件实现SPC过程控制,要求测量数据自动上传MES系统的延迟时间≤200ms,典型特征尺寸CPK值需稳定在1.67以上。
通过实施上述检测矩阵,企业可构建覆盖设备全生命周期的精度管理体系。实践表明,规范的检测流程可使加工中心年故障率降低40%,刀具损耗减少25%,在提升良品率的同时显著降低综合运维成本,为高附加值产品制造提供可靠保障。
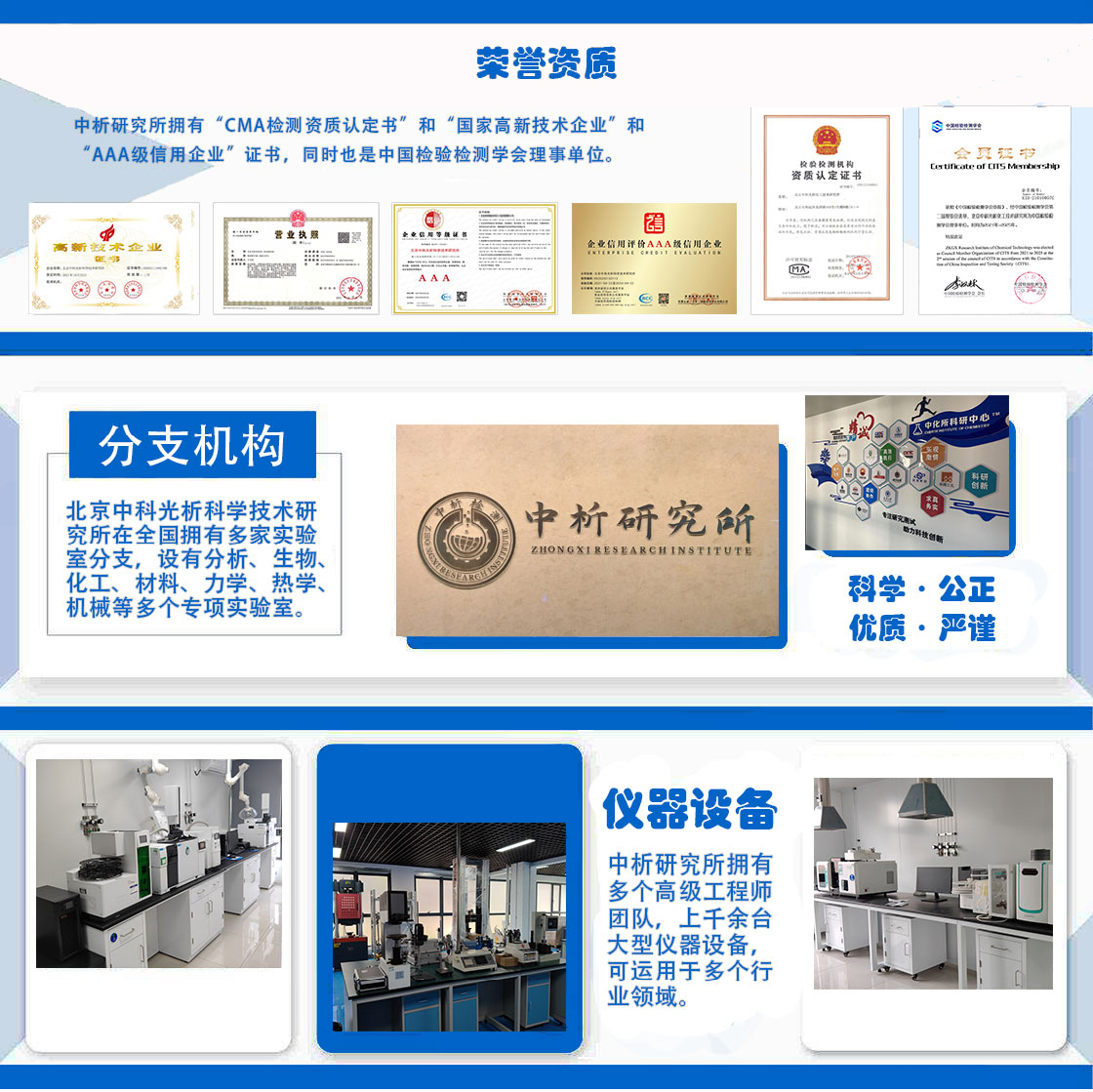
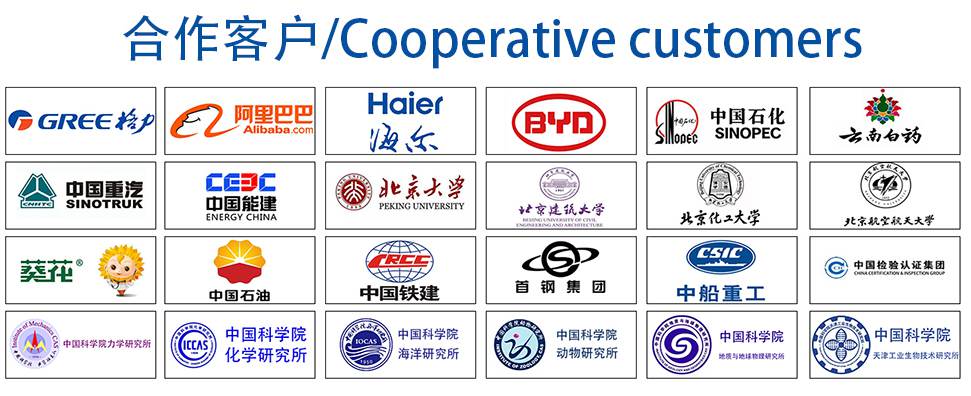