圆锥滚子超精机检测项目的关键技术与流程
圆锥滚子超精机是轴承制造领域的核心设备,其加工精度直接影响圆锥滚子的几何形状、表面粗糙度及轴承整体性能。随着工业对高精度、长寿命轴承需求的提升,超精机的检测项目成为确保产品质量的关键环节。检测过程需覆盖设备静态精度、动态加工性能、工艺参数匹配性以及成品滚子的微观形貌等多个维度,通过科学化、数据化的手段,保障设备处于最佳运行状态,同时满足滚子尺寸公差、圆度误差、表面波纹度等核心指标要求。
1. 超精机几何精度检测
几何精度是超精机性能的基础,检测项目主要包括滚道圆度误差、主轴径向跳动、导轨直线度及锥角定位精度。通过激光干涉仪、千分表及三坐标测量仪,对设备运动轨迹进行三维空间补偿校准。重点检查磨头与修整器的同轴度偏差(≤0.005mm)、工作台倾斜角度重复精度(±2")等参数,确保滚子锥面与基准面的几何一致性。
2. 表面质量在线监测系统
采用白光干涉仪与表面粗糙度仪联用技术,对超精加工后的滚子表面进行纳米级检测。系统实时监测Ra值(目标≤0.05μm)、波纹度(Wt≤0.1μm)及烧伤缺陷,通过谐波分析识别振动导致的周期性纹路。集成机器学习算法,可自动分类表面瑕疵类型(如磨削振纹、材料剥离等),检测效率较传统方法提升80%。
3. 轴承动态性能验证
在模拟工况环境下进行滚子-滚道系统动态测试,包括:
• 接触应力分布检测:利用压力敏感薄膜测量赫兹接触区压力峰值(≤2500MPa)
• 温升特性测试:红外热像仪监控高速运转下滚子表面温升(ΔT≤45℃)
• 疲劳寿命试验:2000小时加速寿命测试中监控剥落、点蚀等失效模式
4. 工艺参数智能优化
基于数字孪生技术构建超精工艺仿真模型,对振荡频率(40-120Hz)、进给量(0.5-3μm/s)、油石压力(0.1-0.3MPa)等参数进行多目标优化。通过粒子群算法寻找最佳参数组合,使滚子圆度误差降低至0.3μm以内,批产一致性CPK≥1.67。
5. 环境适应性检测
严格监控加工环境对超精质量的影响:
• 温度波动控制:工作区温度20±0.5℃,梯度变化≤0.3℃/h
• 油液清洁度:NAS 6级标准,在线颗粒计数器实时监控
• 振动隔离:地基振动加速度≤0.5mm/s²(5-1000Hz频段)
6. 数据驱动的质量追溯体系
构建MES-QMS集成系统,实现检测数据的全生命周期管理。每个滚子附带二维码,可追溯加工参数、设备状态、检测记录等200+项数据。通过SPC控制图监控关键质量特性(Cpk≥1.33),建立基于大数据的预警模型,提前识别潜在质量风险。
通过上述系统化检测项目的实施,圆锥滚子超精机的加工精度可稳定达到DIN 620-2标准P5级要求,为高端轴承制造提供可靠保障。未来,随着机器视觉、量子传感等技术的应用,检测精度与效率将实现新的突破。
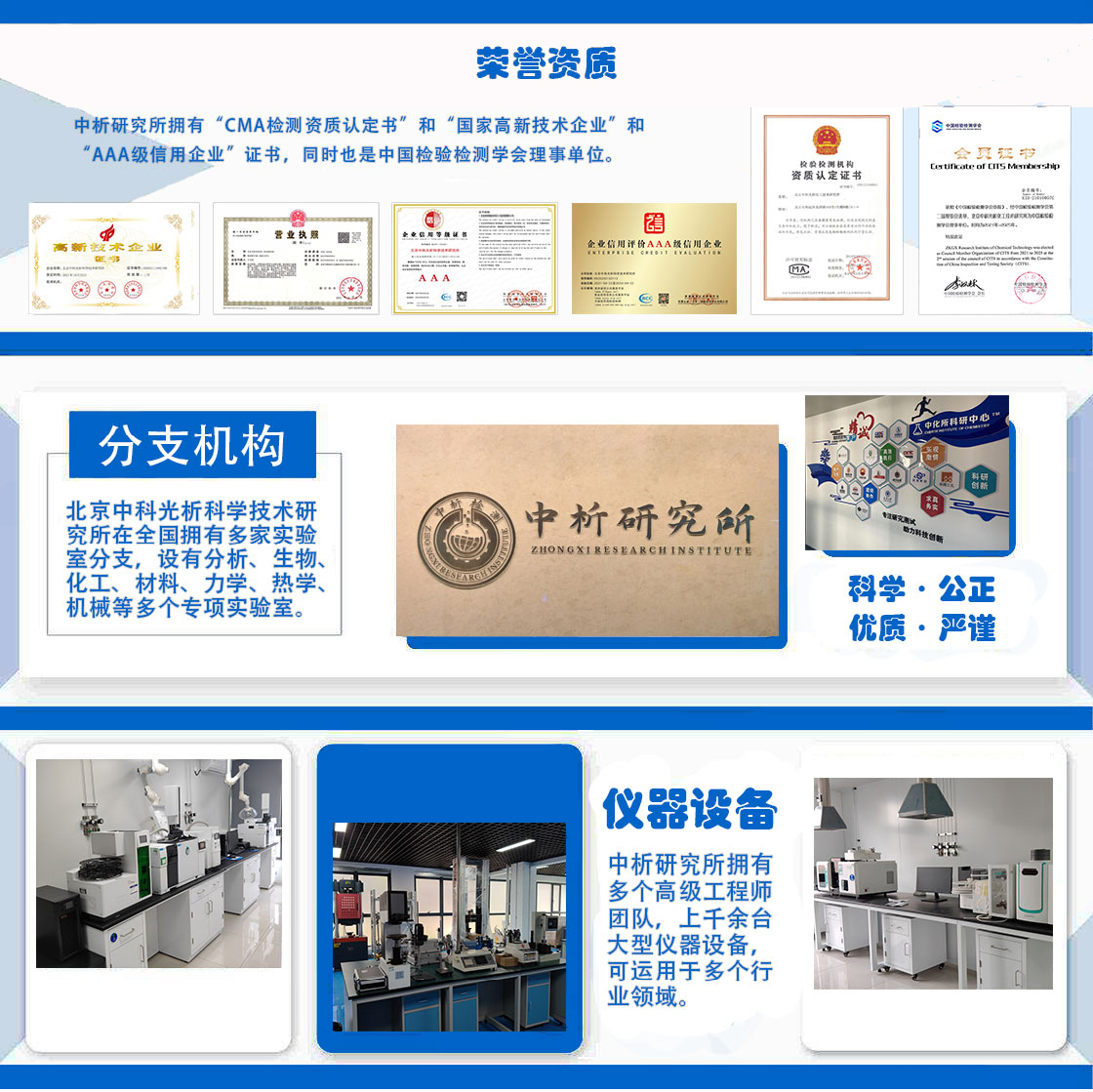
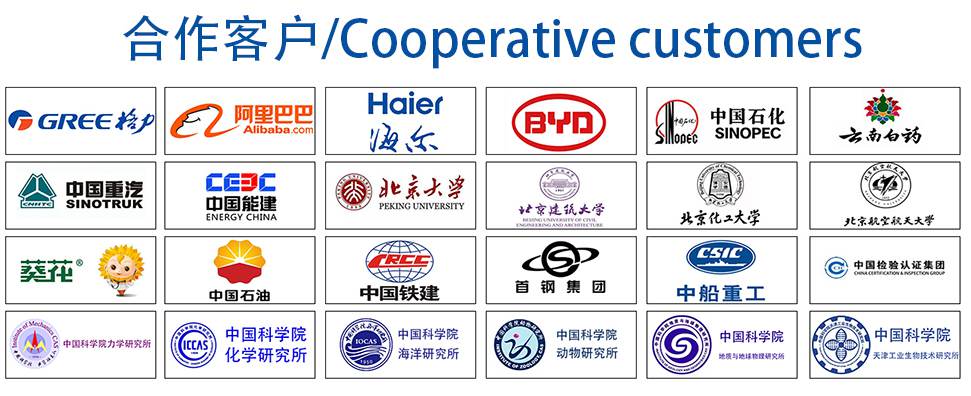