高速数控卧式车床检测的重要性与核心内容
在精密机械加工领域,高速数控卧式车床作为高精度、高效率的加工设备,被广泛应用于航空航天、汽车制造、能源装备等高端行业。其性能直接影响工件的加工质量与生产效率。然而,随着设备长时间运行或关键部件磨损,精度和稳定性可能逐渐下降。因此,定期开展系统性检测是确保设备可靠性和工艺一致性的必要手段。通过科学的检测流程,可以精准定位设备故障隐患,优化加工参数,并为设备维护提供数据支持。
核心检测项目与技术要求
1. 几何精度检测
几何精度是车床加工能力的核心指标,需通过专业量具和仪器进行专项测试,包括:主轴径向/轴向跳动误差(≤0.005mm)、导轨直线度(全行程≤0.01mm)、刀架重复定位精度(±0.003mm)以及尾座与主轴的同轴度(≤0.015mm)。检测过程中需严格遵循ISO 10791等国际标准。
2. 动态性能检测
动态性能反映设备在高速运转下的稳定性,主要包含:主轴最高转速验证(需达到标称转速的95%以上)、进给系统加速度测试(X/Z轴加速度偏差<5%)、切削负载下的振动值监测(振幅≤4μm)以及异常噪音频谱分析。此类检测通常采用激光干涉仪和振动传感器完成。
3. 加工精度综合验证
通过试件加工进行实际工况验证,重点检测:直径尺寸公差(IT6级及以上)、端面平面度(≤0.008mm)、表面粗糙度(Ra≤1.6μm)以及螺纹中径一致性。需选用标准试棒(如直径Φ50×200mm)进行多工序复合加工测试。
4. 安全功能与防护检测
安全性能检测涵盖急停响应时间(≤0.5秒)、防护门联锁灵敏度、过载保护触发阈值(额定电流的110%-130%)以及冷却液泄漏监测。同时需检查导轨防护罩密封性及排屑系统的运行效率。
5. 数控系统功能校验
对数控系统进行G代码执行验证、插补精度测试(圆弧误差≤0.01mm)、伺服电机跟随误差(±2脉冲以内)以及通讯接口稳定性测试。需使用球杆仪和动态刚度分析仪进行多轴联动精度评估。
检测结果分析与优化建议
完成检测后,需结合设备历史数据和行业标准生成多维分析报告,对超差项提出针对性改进方案,如主轴轴承预紧力调整、伺服参数优化或导轨铲刮修复。同时建立检测周期数据库,通过趋势分析实现预防性维护,最大限度降低非计划停机风险。
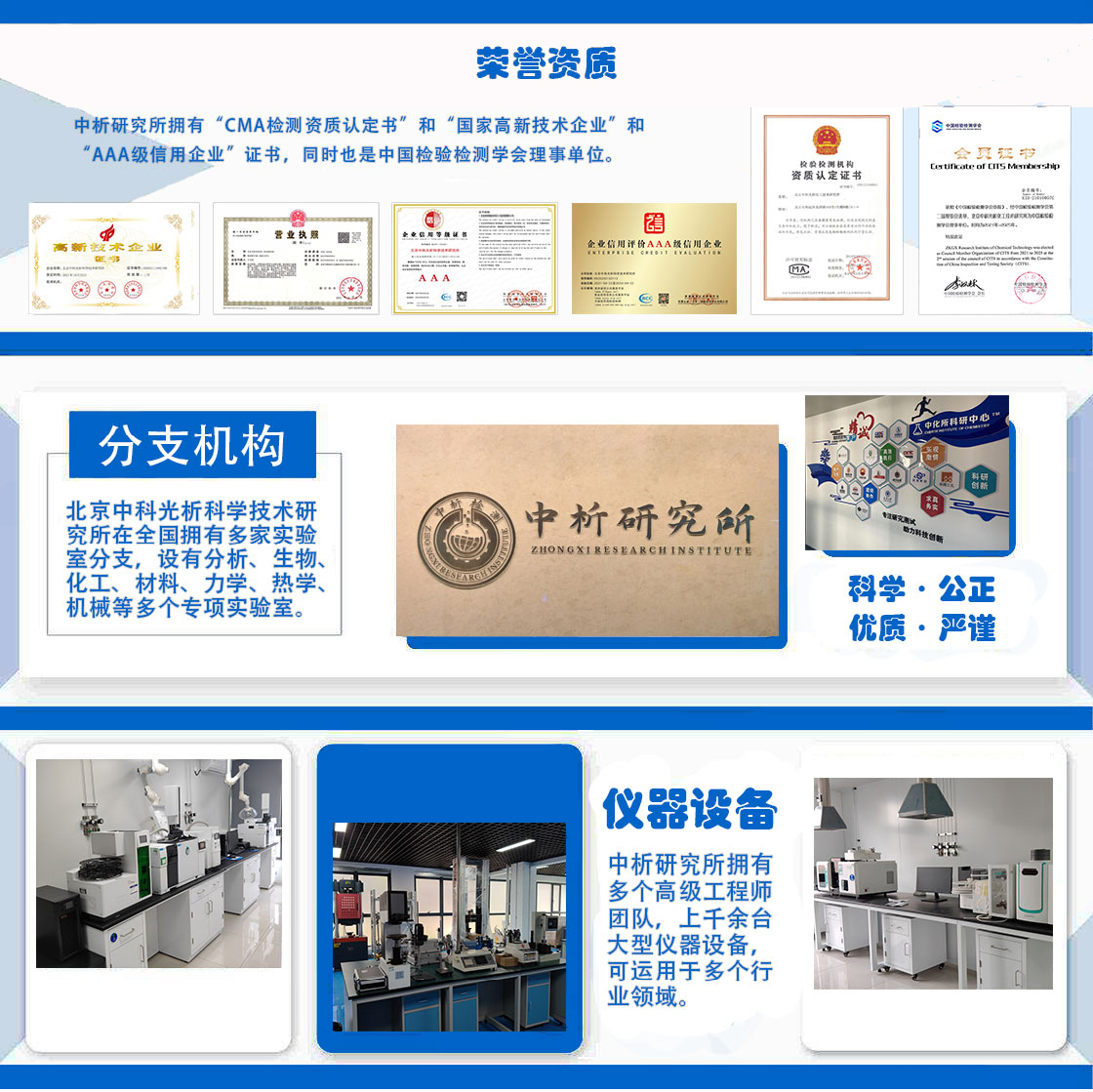
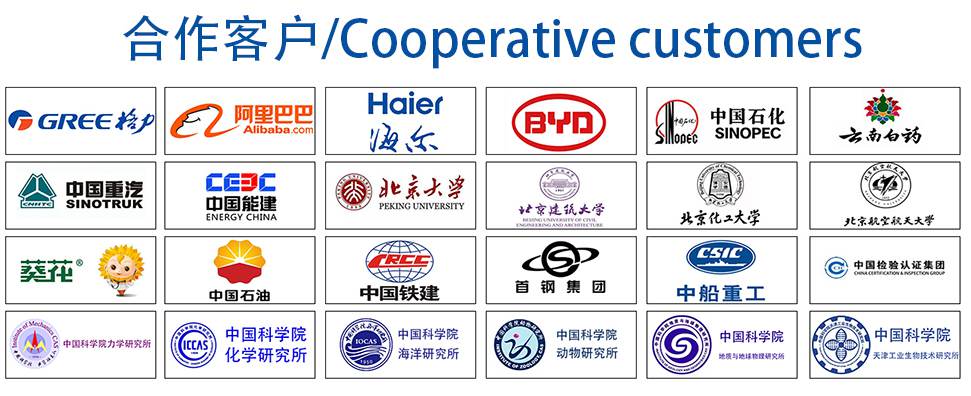