向心滚针和保持器组件作为滚动轴承的核心部件,广泛应用于汽车变速箱、工业减速器、航空航天等高精度传动系统中,其性能直接影响设备的承载能力、旋转精度及使用寿命。为确保组件在高速、重载工况下的可靠性,需通过系统性检测验证其几何精度、材料性能、装配质量等关键指标。检测流程需严格遵循ISO 3030、GB/T 309-2017等行业标准,结合目视检查、尺寸测量、材料分析及动态试验等手段,全面评估组件在疲劳寿命、抗磨损性和抗变形能力等方面的表现。
一、外观与尺寸精度检测
采用3D光学轮廓仪与电子显微镜对滚针表面进行100%全检,识别划痕、凹坑、锈蚀等缺陷。保持器需重点检测兜孔形状公差(±0.02mm)、窗梁厚度偏差(≤±5%),使用三坐标测量仪验证节圆直径(PCD)的径向跳动量(≤0.03mm)。滚针直径分组需达到微米级精度,确保同一组内直径差≤1μm。
二、材料性能测试
通过洛氏硬度计(HRC 58-62)检测滚针表面硬化层深度(0.6-1.2mm),采用光谱仪分析GCr15轴承钢的化学成分(Cr含量1.45%-1.65%)。保持器需进行盐雾试验(96小时无红锈)验证镀锌层防腐性,注塑保持器应通过DSC差示扫描量热法检测PA66材料的玻璃化转变温度(≥220℃)。
三、装配配合特性检测
使用轴向游隙仪测量组件装配后的轴向间隙(0.02-0.08mm),保持器与滚针的径向配合间隙需控制在0.05-0.15mm。动态检测包含:
- 扭矩测试:空载启动力矩≤0.15N·m
- 温升试验:3000rpm持续运转2小时温升≤35℃
- 振动值检测:加速度有效值≤1.5m/s²
四、耐久性验证试验
在专用试验台上进行加速寿命测试,施加额定动载荷(Cr值)的120%进行100万次循环,检测保持器兜孔磨损量(≤0.01mm)、滚针表面剥落面积(≤0.5%)。同时开展极限转速试验,记录保持器塑性变形时的临界转速值(需≥标称转速的150%)。
企业应建立检测数据追溯系统,建议每季度进行预防性检测,重点监控保持器窗梁应力集中区域。通过实施SPC统计过程控制,可将组件早期故障率降低60%以上,显著延长轴承使用寿命。
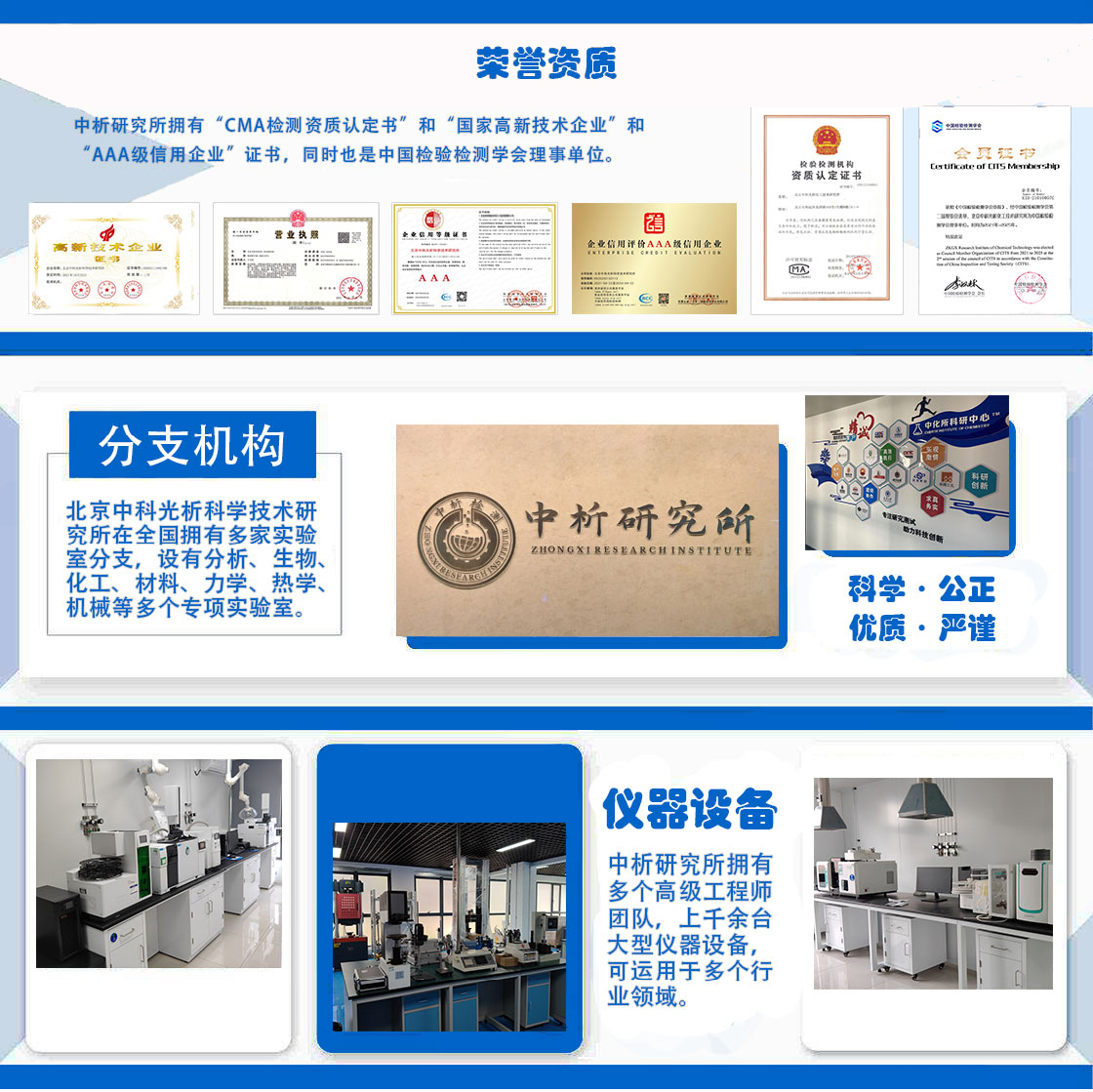
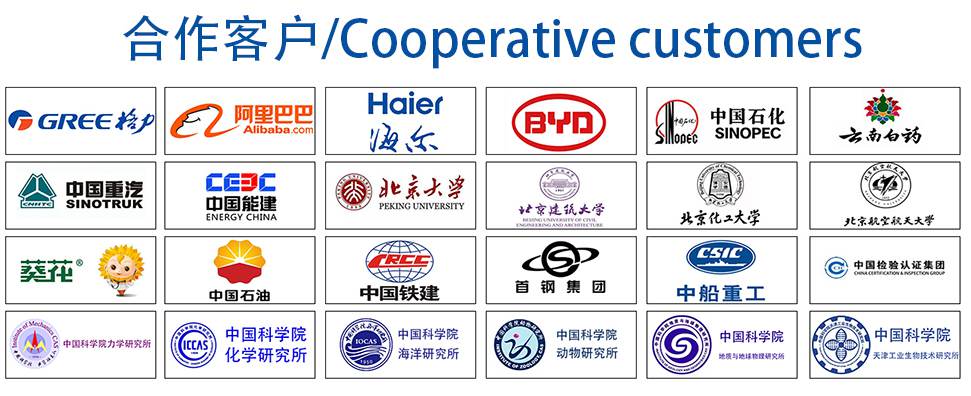