组合机床镗孔车端面头检测项目详解
组合机床作为现代机械加工领域的核心设备,其镗孔车端面头的加工精度直接影响工件质量与生产效率。该部件集成了镗削、车削复合功能,长期运行中易受刀具磨损、主轴偏移、温度形变等因素影响。开展系统化检测是保障加工尺寸公差、表面粗糙度及设备稳定性的关键环节,需覆盖几何精度、运动特性、动力性能等多维度指标,检测周期建议结合设备使用强度设置为500-2000小时/次。
一、几何精度检测
使用激光干涉仪配合标准芯轴,检测主轴轴线与工作台面的垂直度(允许偏差≤0.02mm/m);通过千分表测量镗杆伸出不同长度时的径向跳动(≤0.015mm为合格);采用光学平晶检测端面车刀安装基面的平面度(误差需控制在0.01mm内)。重点排查导轨磨损导致的运动轨迹偏差,该项异常会引发锥孔或椭圆孔缺陷。
二、主轴系统检测
采用振动分析仪监测主轴在3000-8000rpm区间的振动烈度(应<2.8mm/s),同步检测轴承温升(超过环境温度35℃需预警);使用扭矩传感器测试额定转速下的输出扭矩衰减情况(对比新机下降超过15%需维护);通过声发射技术捕捉齿轮箱异常啮合信号,提前发现齿面点蚀故障。
三、切削性能测试
设定标准试件(45钢,HB200-220)进行阶梯镗孔试验,每档进给量递增0.05mm/r,监测切削力波动(允许值±8%);采用表面轮廓仪测量孔壁Ra值(应≤1.6μm),同时观察积屑瘤生成情况;通过功率分析仪记录空转与满负荷状态能耗比,能效下降10%以上提示传动系统损耗异常。
四、润滑与温升检测
使用红外热像仪扫描关键运动副温度分布,导轨滑块区域温升不应超过45℃;定期抽取润滑油进行铁谱分析,当磨粒浓度>100ppm或出现>50μm大颗粒时,需立即停机检修;检测液压夹具系统保压性能,10分钟内压力下降超过0.5MPa判定密封失效。
五、重复定位精度验证
通过雷尼绍激光校准系统,在X/Y/Z三轴方向进行双向重复定位测试(±0.005mm为A级标准);模拟换刀500次后,检测刀柄拉紧力衰减(不得低于额定值的85%);使用球杆仪进行圆周插补测试,圆度误差>0.03mm时需补偿反向间隙。
六、安全防护装置检测
验证防护门联锁响应时间(<0.5秒),测试急停按钮全轴制动距离(≤50mm);检测切削液过滤系统颗粒物捕捉效率(5μm以上颗粒去除率应>95%);通过接地电阻测试仪确认整机接地电阻值(≤4Ω),防范静电积聚风险。
通过上述系统性检测,可精准定位组合机床镗孔车端面头的性能劣化点。建议建立检测数据库,通过趋势分析预测部件寿命,将事后维修转变为预防性维护。每次检测后需出具包含实测数据与调整建议的完整报告,特别关注同轴度、主轴刚度和热变形补偿参数的变化趋势,这对保持精密加工能力具有决定性作用。
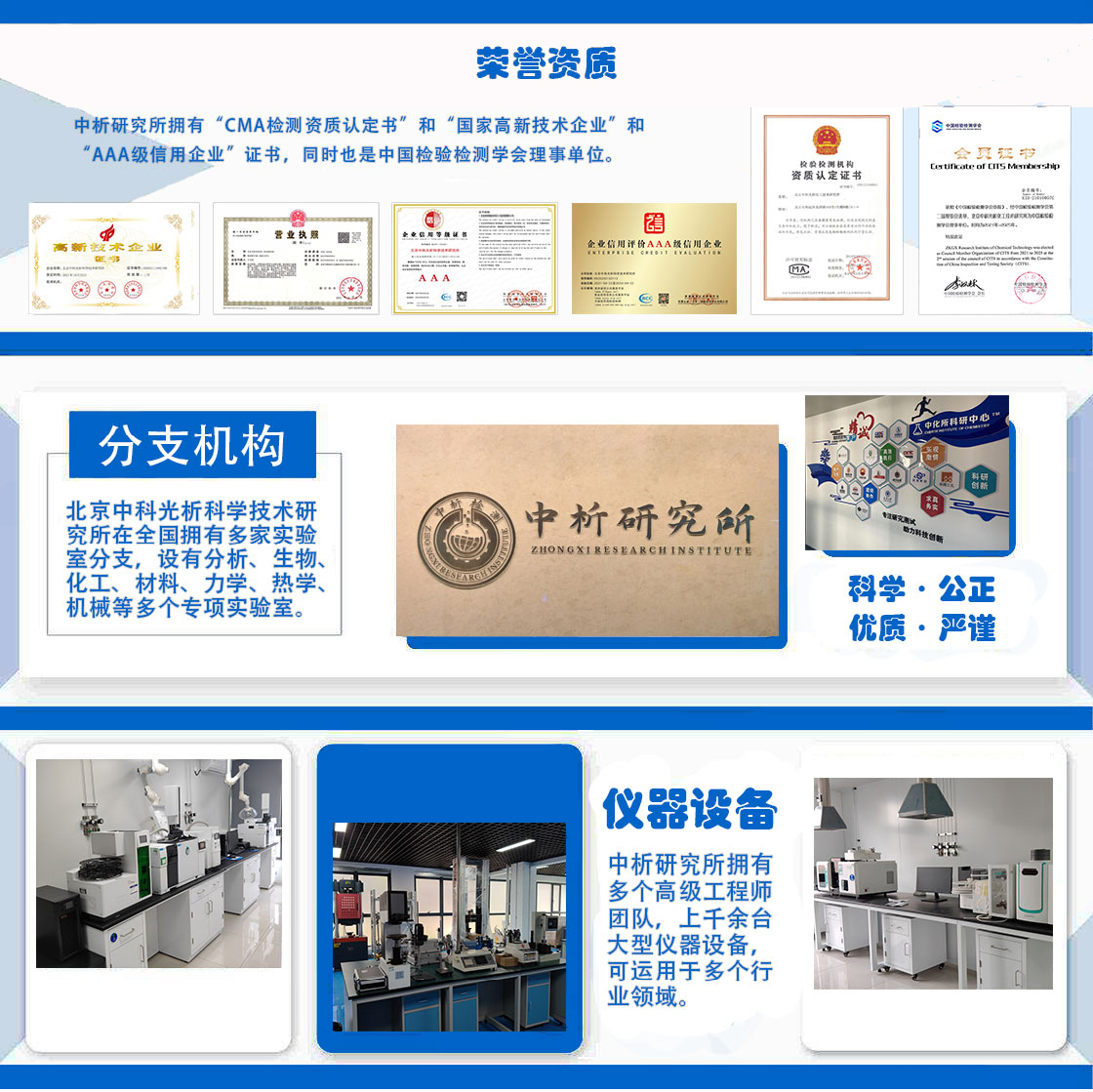
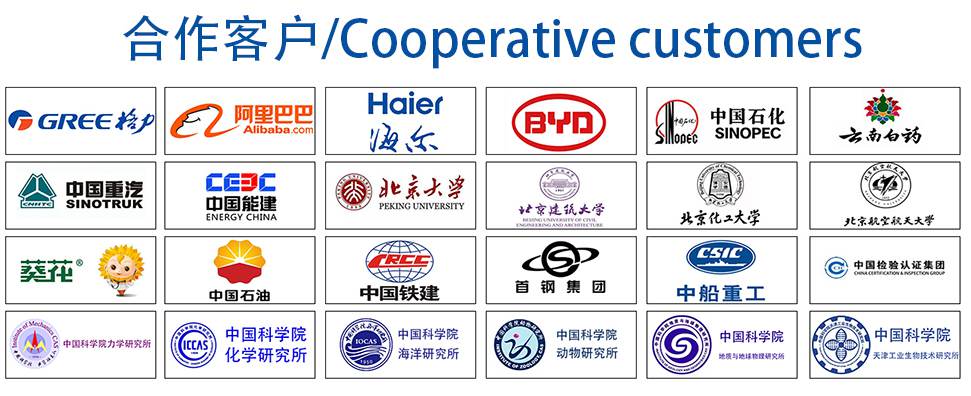