轴承用碳钢检测的重要性
轴承作为机械设备中承受载荷和传递动力的核心部件,其材料性能直接决定了设备运行的可靠性和使用寿命。碳钢因具有高强度、耐磨性和经济性,成为轴承制造的常用材料之一。然而,碳钢的化学成分、硬度、金相组织等参数若不符合要求,可能导致轴承过早失效,甚至引发设备故障。因此,对轴承用碳钢进行系统化检测是确保产品质量、延长使用寿命的关键环节。通过科学检测,可精准评估材料的力学性能、微观结构缺陷及抗疲劳能力,为轴承设计、选材和生产工艺优化提供数据支撑。
轴承用碳钢核心检测项目
1. 化学成分分析
采用光谱分析仪或湿法化学分析,检测碳(C)、锰(Mn)、硅(Si)、硫(S)、磷(P)等元素含量是否符合GB/T 699-2015《优质碳素结构钢》标准。碳含量需控制在0.95%-1.10%范围内以平衡硬度和韧性,硫磷杂质需低于0.025%以避免脆性增加。
2. 硬度测试
通过洛氏硬度计(HRC)或布氏硬度计(HB)测量表面硬度和芯部硬度梯度,确保轴承钢经热处理后表面硬度达到58-64HRC,同时芯部保持适度韧性。硬度不均匀易导致接触疲劳失效。
3. 金相组织检查
使用金相显微镜观察退火态球化组织(球状珠光体占比≥90%)及淬回火后的马氏体形态,要求晶粒度≥8级。碳化物分布不均或存在网状碳化物会显著降低轴承抗剥落能力。
4. 力学性能测试
通过万能试验机测定抗拉强度(≥1800MPa)、屈服强度(≥1600MPa)和冲击韧性(≥32J/cm²),验证材料在高载荷、冲击工况下的承载能力,确保满足GB/T 18254-2016《高碳铬轴承钢》要求。
5. 非接触式尺寸检测
采用三坐标测量仪或激光扫描仪检测轴承钢坯料的直径公差(±0.05mm)、圆度误差(≤0.01mm)及表面波纹度,避免加工过程中因尺寸偏差导致轴承装配干涉或振动异常。
6. 超声波探伤
利用5MHz高频探头检测内部夹杂物、裂纹等缺陷,要求缺陷当量直径≤φ0.8mm,密集缺陷区面积≤3mm²。内部缺陷是轴承早期疲劳裂纹的主要诱因。
检测技术与质量控制流程
现代轴承钢检测采用"原材料入厂检验-制程抽检-成品全检"三级控制体系,结合X射线能谱分析、扫描电镜(SEM)等齐全手段,实现从微观组织到宏观性能的全维度监控。通过建立SPC(统计过程控制)模型,可动态优化热处理工艺参数,将材料不合格率控制在0.3%以下。
结语
系统化的轴承用碳钢检测不仅需要精准的仪器设备,更依赖于完善的检测标准和专业的技术团队。通过多维度参数联检,可有效预防材料缺陷,提升轴承产品的疲劳寿命和可靠性,为高端装备制造提供基础材料保障。
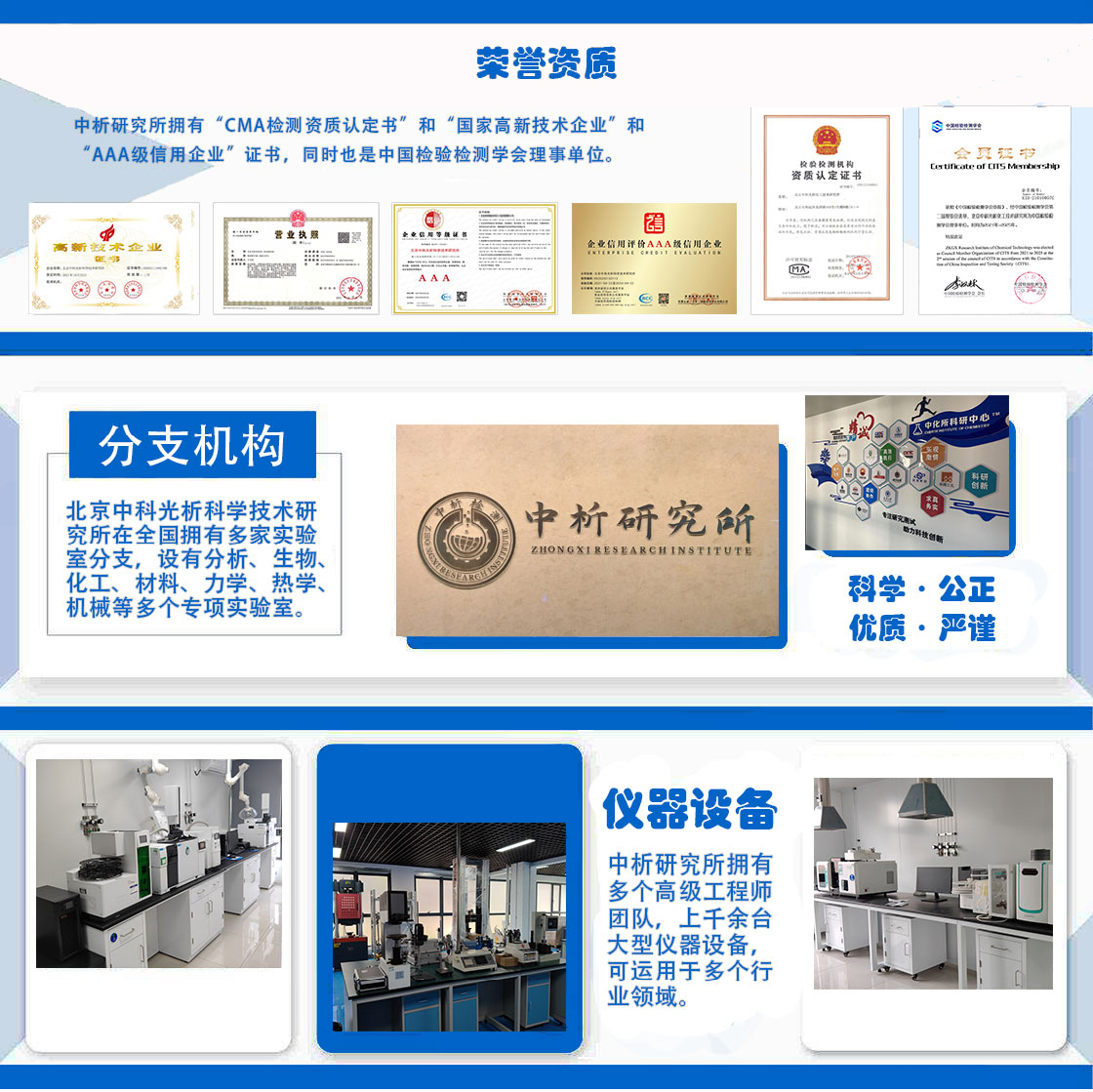
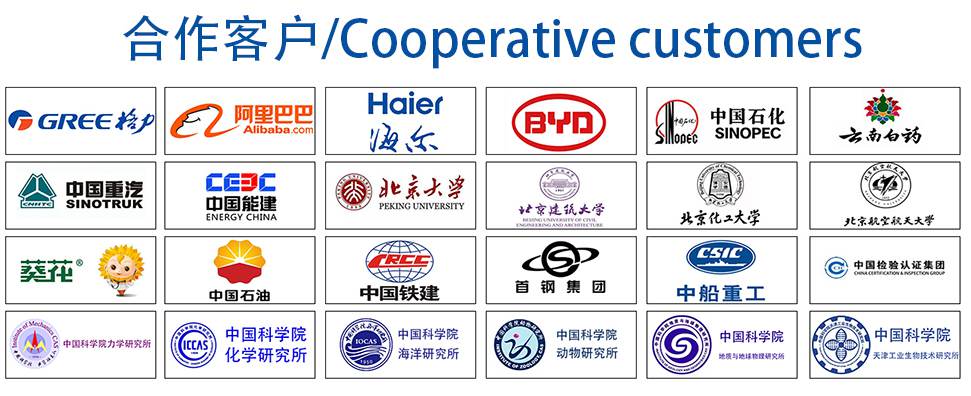