航空机架轴承检测的重要性与核心内容
航空机架轴承作为飞机机械系统的核心部件,承担着支撑旋转机构、传递载荷和减少摩擦的关键作用。由于其工作环境需承受极端温度、高速运转及高频振动,任何微小缺陷都可能引发连锁反应,威胁飞行安全。因此,航空轴承的检测是飞机制造、维护和适航认证中不可或缺的环节。目前,国际航空法规(如FAA、EASA)均明确要求对轴承进行周期性检测,并通过多维度项目评估其性能与可靠性,确保其满足严苛的适航标准。
核心检测项目及技术手段
1. 尺寸精度与几何公差检测
通过三坐标测量仪(CMM)或激光扫描技术,对轴承内外圈直径、滚道圆度、沟道位置等参数进行微米级测量,确保尺寸符合设计规范。几何公差检测重点关注同轴度、平行度及游隙,避免因装配误差导致异常磨损。
2. 表面缺陷与微观形貌分析
使用金相显微镜、扫描电子显微镜(SEM)和表面粗糙度仪,检测滚道、滚子表面的裂纹、剥落、点蚀等缺陷。针对涂层轴承,还需评估镀层厚度与结合强度,防止分层脱落引发失效。
3. 材料性能与金相组织检测
通过硬度测试(洛氏/维氏硬度计)、冲击试验和光谱分析,验证轴承钢的硬度梯度、韧性及化学成分是否符合AMS 6491等航空标准。金相组织分析则用于观察材料晶粒度、碳化物分布及热处理效果,确保抗疲劳性能达标。
4. 动态性能与寿命测试
在模拟工况的试验台上,对轴承进行高速(≥15,000 rpm)、高载荷(轴向/径向复合载荷)耐久性测试,监测温升、振动噪声及润滑剂消耗量。加速寿命试验结合威布尔分布模型,可预测轴承在极端条件下的失效阈值。
5. 润滑状态与污染度监测
采用铁谱分析、颗粒计数器检测润滑脂中的金属磨粒含量与污染等级。红外光谱技术可识别油脂氧化程度及添加剂衰减情况,避免因润滑失效导致轴承卡滞。
6. 无损检测(NDT)技术应用
综合运用超声波检测(UT)探测内部孔隙与夹杂物,磁粉检测(MT)识别表面/近表面裂纹,涡流检测(ET)评估导电涂层的完整性。相控阵超声和X射线断层扫描(CT)技术已逐步应用于复杂结构轴承的精细化检测。
检测数据管理与智能化趋势
现代航空检测体系通过数字化平台整合多源数据,利用AI算法对历史检测结果进行趋势分析,实现故障预警与剩余寿命预测。基于数字孪生技术的虚拟检测模型,可大幅缩短试验周期,为轴承设计优化提供数据支撑。
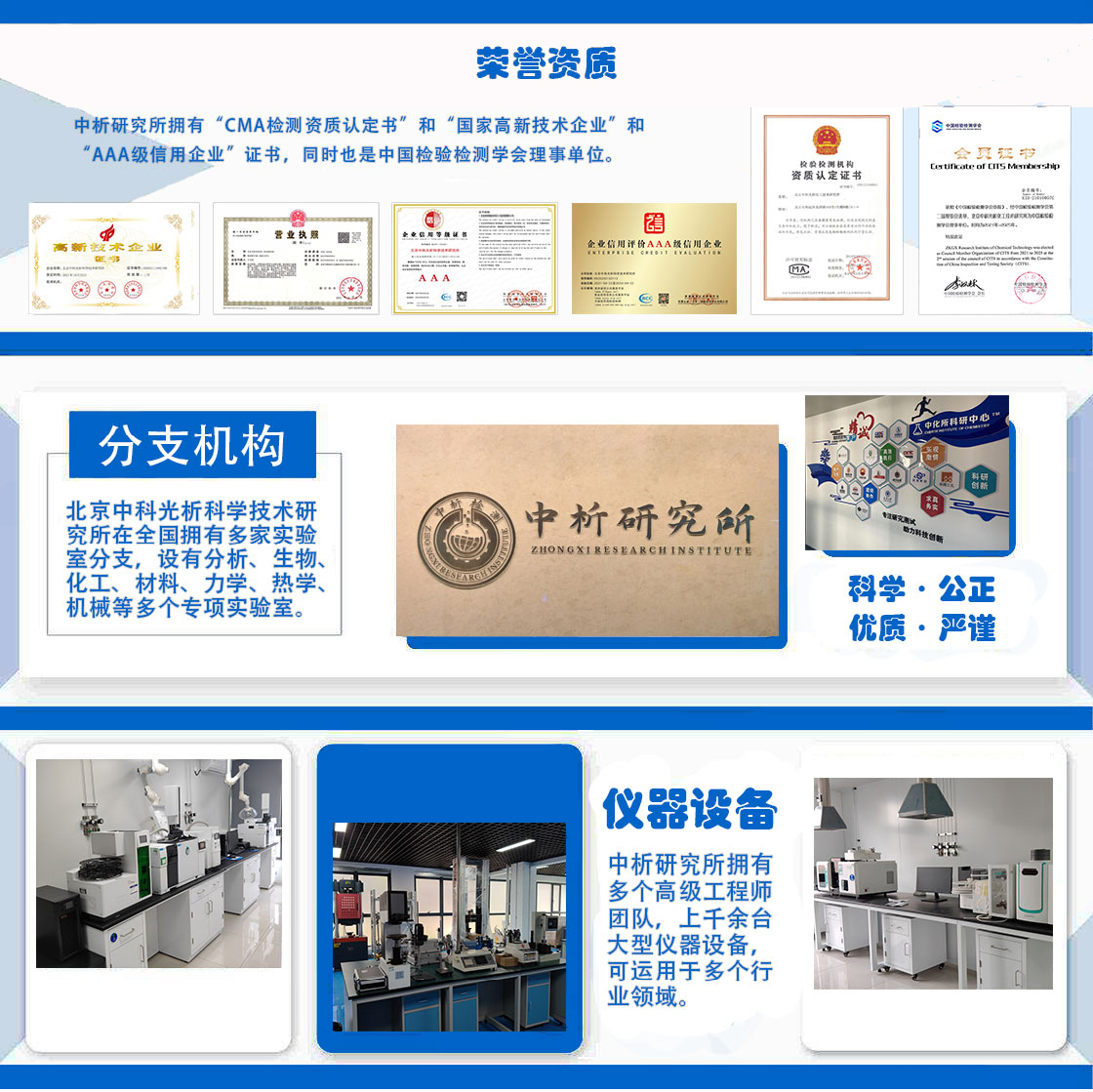
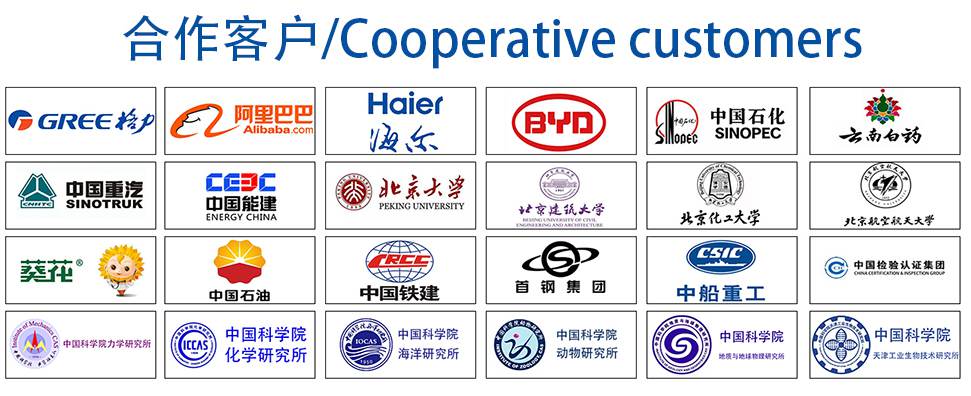