重力式自动装料衡器检测的重要性与核心内容
重力式自动装料衡器是工业生产中广泛应用的称重设备,尤其在化工、食品、制药等行业中承担着精准配料和定量装料的关键任务。其性能直接影响生产效率、产品质量及成本控制,因此定期进行专业检测是保障设备可靠性和合规性的必要措施。依据国家标准《JJG 564-2019重力式自动装料衡器检定规程》,检测需覆盖机械结构、电子系统、称量精度及环境适应性等多个维度,确保设备达到法定计量要求。
核心检测项目详解
1. 静态称量精度检测
通过标准砝码对衡器的静态称量误差进行校准,检测其在不同载荷下的示值偏差。需验证最大允许误差(MPE)是否符合规程要求,重点关注非线性误差和重复性误差的合格范围。
2. 动态称量精度测试
模拟实际生产中的连续装料流程,使用已知质量的物料进行动态称量测试。记录多次装料结果的变异系数(CV值),评估设备在高速运行状态下的稳定性与一致性。
3. 重复性与零点稳定性检测
通过重复加载相同载荷(通常为最大称量的50%-100%)10次以上,计算示值的标准偏差和极差。同时测试设备在空载状态下的零点漂移,确保长期运行的稳定性。
4. 物料适应性评估
针对不同物料的特性(如流动性、颗粒度、湿度),检测装料系统的适应性。例如,粉末状物料需验证防尘密封性能,黏性物料需测试卸料残留量是否超标。
5. 抗干扰能力测试
通过电磁兼容性(EMC)试验和机械振动测试,验证设备在电磁干扰、电源波动或生产振动环境下的称量精度。特别是对传感器信号传输系统的抗干扰能力需重点考核。
6. 机械结构耐久性检测
对给料装置、称量斗、卸料机构等核心部件进行疲劳试验,模拟高频率工作状态下的磨损情况。同时检查气动/电动执行元件的响应速度和密封性能。
7. 软件功能验证
对控制系统进行黑盒测试,包括配方管理、故障诊断、数据存储等功能模块的完整性验证,确保软件符合OIML R61国际建议中关于计量安全的保护要求。
检测流程与结果判定
检测通常分为预检(目视检查、文件审查)、基本功能测试、性能校准三个阶段。所有数据需依据规程中的允差表进行判定,对于首次检定的衡器,若关键项目(如动态称量误差)超出MPE的0.7倍即判定不合格,使用中检验的容差可放宽至MPE的1.0倍。检测机构需具备 认证资质,并出具包含修正系数和校准周期的完整报告。
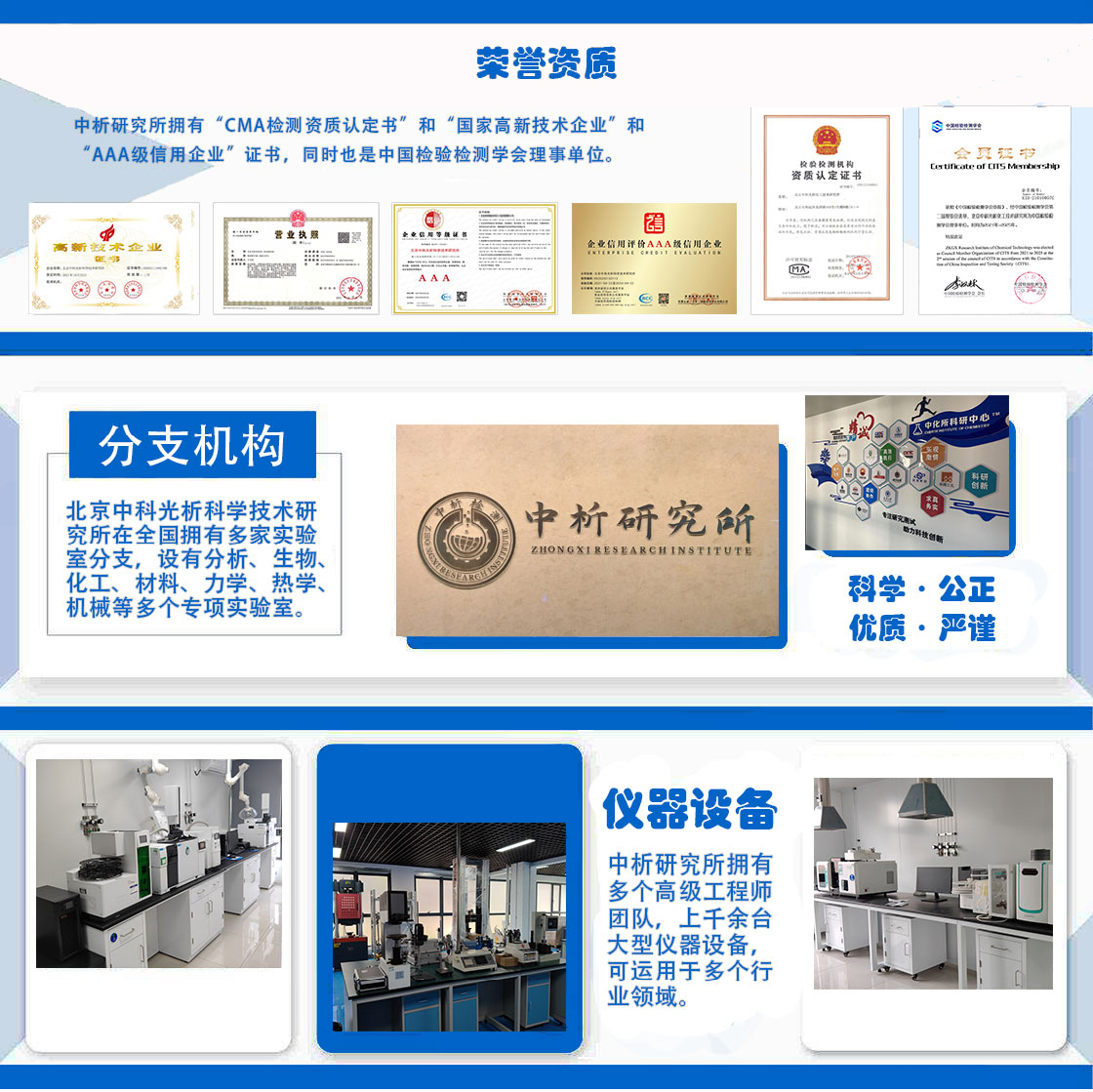
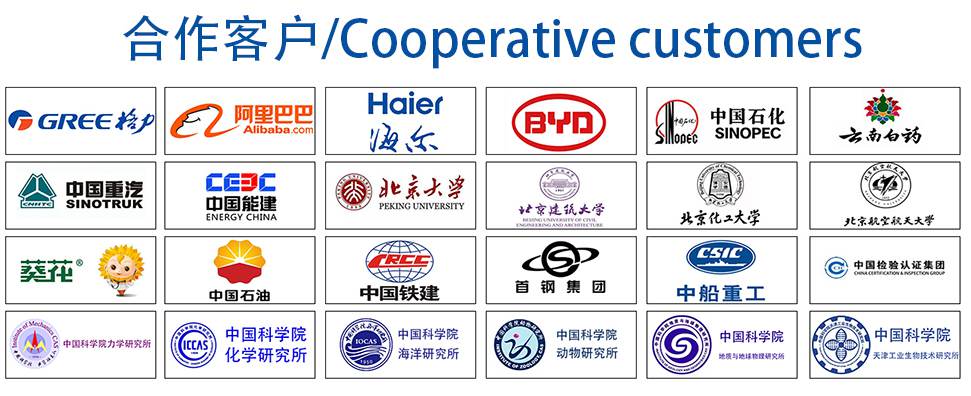