气路系统密封性检测的重要性与核心内容
气路系统是工业设备、医疗仪器、汽车制造等领域中依赖压缩空气或气体传输的关键组成部分。其密封性能直接影响系统效率、能耗及安全性。若存在泄漏,不仅会导致能源浪费、运行成本上升,还可能引发设备故障甚至安全隐患。因此,气路系统密封性检测成为日常维护与设备验收的必要环节。通过规范化的检测流程,可精准定位泄漏点,评估系统整体可靠性,并为优化设计提供数据支持。
气路系统密封性检测的核心项目
气路系统的密封性检测需覆盖以下关键项目:
1. 压力衰减测试
通过向系统内注入压缩气体并监测压力变化,计算单位时间内压力下降值。若压力降超出标准范围,表明存在泄漏。此方法适用于管道、阀门及连接件的快速筛查。
2. 流量测试法
在系统末端安装流量计,测量气体输出流量与输入流量的差值。差值越大,泄漏量越高,适用于持续供气设备的动态检测。
3. 气泡法/检漏液检测
在可疑部位涂抹专用检漏液(如肥皂水),观察是否产生气泡。该方法操作简单、成本低,但对微小泄漏的灵敏度较低。
4. 红外热成像检测
利用气体泄漏导致的局部温度变化,通过红外热像仪捕捉异常热点,适用于复杂管路或高危环境下的非接触式检测。
检测设备与技术要求
检测过程需结合专业设备和标准规范:
• 压力传感器与数据记录仪:实时记录压力波动,精度需达到±0.5% FS;
• 超声波检漏仪:捕捉高频泄漏声波,适用于高压气路;
• 氦质谱检漏仪(高精度场景):通过氦气示踪检测微小泄漏,灵敏度可达10-9 Pa·m³/s;
• 执行标准:参照ISO 8573(压缩空气质量)、ASME B16.34(阀门密封)等行业规范。
常见泄漏源与解决方案
检测中需重点关注以下高频泄漏点:
• 管路接头与法兰:密封圈老化或安装不当导致泄漏,需更换材质(如改用氟橡胶密封件);
• 电磁阀/气缸活塞:密封件磨损或杂质卡滞,需定期清洁并采用耐磨涂层;
• 软管破损:因折弯、高温或化学腐蚀引发,建议使用带钢丝编织层的耐压软管。
检测结果分析与优化建议
依据检测数据可制定针对性改进方案:
• 对于泄漏率>5%的系统,需优先修复大泄漏点并复检;
• 采用分段隔离法缩小泄漏范围,提升排查效率;
• 建立周期性检测计划,结合预测性维护(如振动分析)降低故障率。
通过系统性检测与优化,气路系统的密封性可提升30%-50%,显著降低能耗并延长设备寿命。
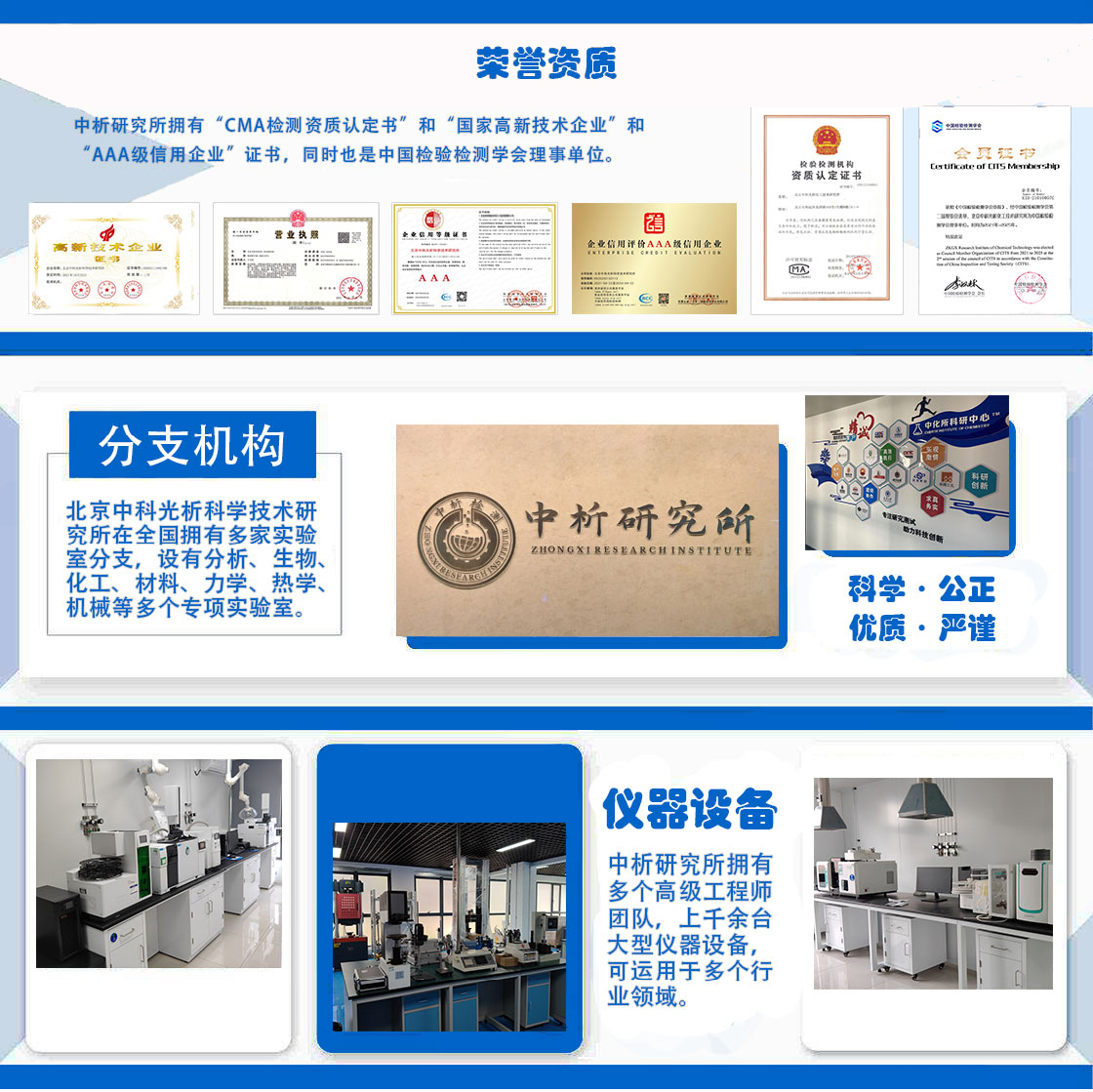
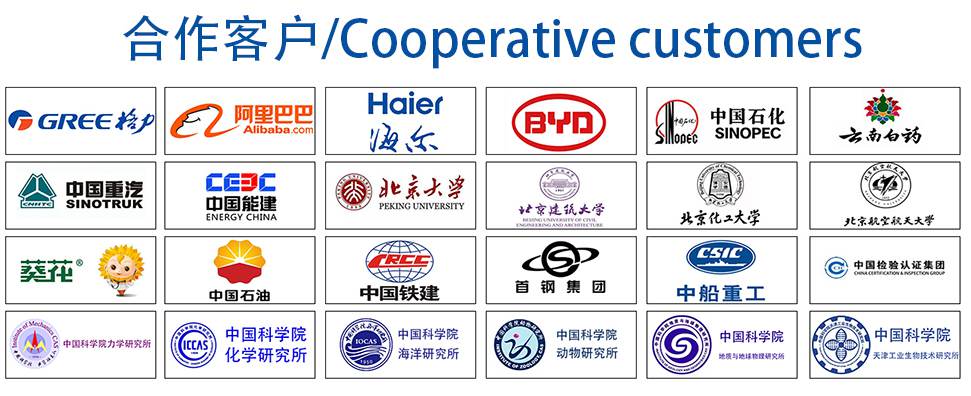