超声探伤仪检测的原理与应用
超声探伤仪是一种利用超声波技术对材料内部缺陷进行非破坏性检测(NDT)的关键设备,广泛应用于航空航天、轨道交通、压力容器、建筑工程等领域。其核心原理是通过探头向被测物体发射高频声波,当声波遇到材料内部的缺陷(如裂纹、气孔、夹杂物等)时,会产生反射、散射或衰减现象,仪器通过接收并分析这些信号的变化,即可精准定位缺陷的位置、大小和性质。相较于传统检测方法,超声探伤技术具有灵敏度高、穿透力强、操作灵活且不损伤工件的显著优势,已成为工业质量控制的必备手段。
超声探伤仪的主要检测项目
1. 内部缺陷检测
超声探伤仪可高效识别材料内部的裂纹、未熔合、气孔、夹渣等缺陷。通过调整探头频率(通常为1-10MHz)和扫描方式(如脉冲回波法、衍射时差法TOFD),能够对不同厚度和材质的工件进行分层检测。例如,在焊接接头检测中,可清晰分辨焊缝内部的未焊透区域,并通过B扫描图像生成缺陷的三维分布图。
2. 厚度测量与腐蚀评估
针对管道、储罐等易腐蚀设备,超声探伤仪可通过单探头脉冲回波法精确测量剩余壁厚,测量精度可达±0.1mm。通过对比设计厚度与实测数据,能够评估材料腐蚀速率并预测设备寿命。此外,结合C扫描模式,可生成大面积厚度分布云图,为维护决策提供可视化依据。
3. 复合材料分层检测
在碳纤维增强复合材料(CFRP)等层合结构中,超声探伤仪可检测层间脱粘或分层缺陷。采用水浸式探头或相控阵技术,能够适应复杂曲面工件的检测需求。典型的应用场景包括飞机机翼蒙皮、风力发电机叶片的质量控制,缺陷检出率可达99%以上。
4. 应力腐蚀裂纹监测
针对奥氏体不锈钢、铝合金等易发生应力腐蚀开裂的材料,超声探伤仪通过表面波或爬波探头,可检测近表面微米级裂纹。结合时间飞行衍射(TOFD)技术,能准确测定裂纹深度,为高风险设备的预防性维护提供数据支持。
检测流程与质量控制要点
标准化的超声检测流程包括校准试块选择、探头耦合剂涂覆、扫描路径规划、信号采集与数据分析等环节。关键质量控制点包含:
- 仪器灵敏度校准(如DAC曲线制作)
- 耦合剂均匀性与厚度控制
- 扫查速度与探头角度稳定性
- 缺陷定量分析的误差修正(如端点衍射法)
通过科学选择检测参数并严格执行标准(如ISO 17640、ASME Boiler Code),可确保检测结果的可靠性与重复性。随着相控阵超声(PAUT)和全聚焦技术(TFM)的普及,超声探伤仪正向智能化、图像化方向持续发展,为工业安全提供更强大的技术保障。
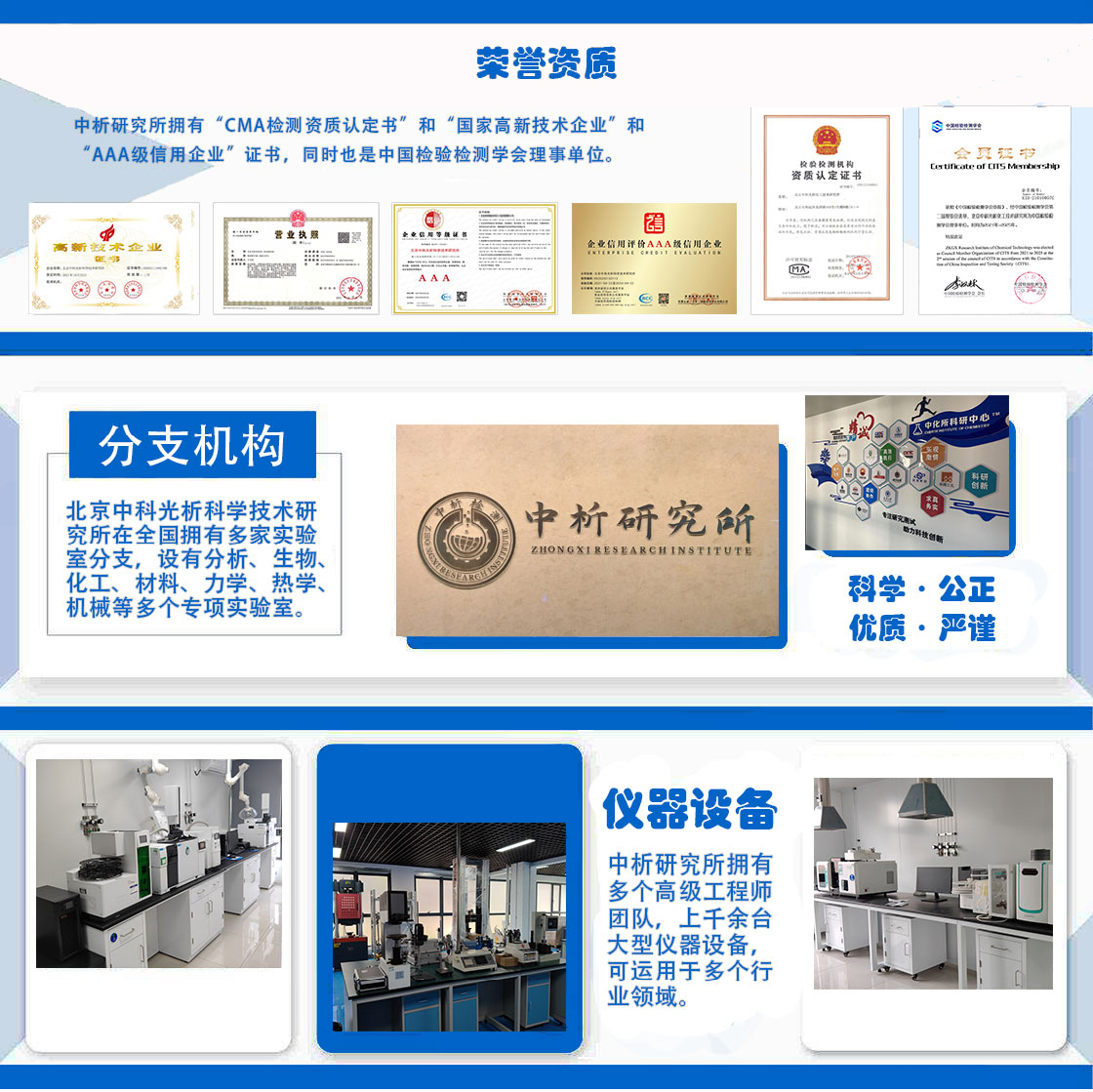
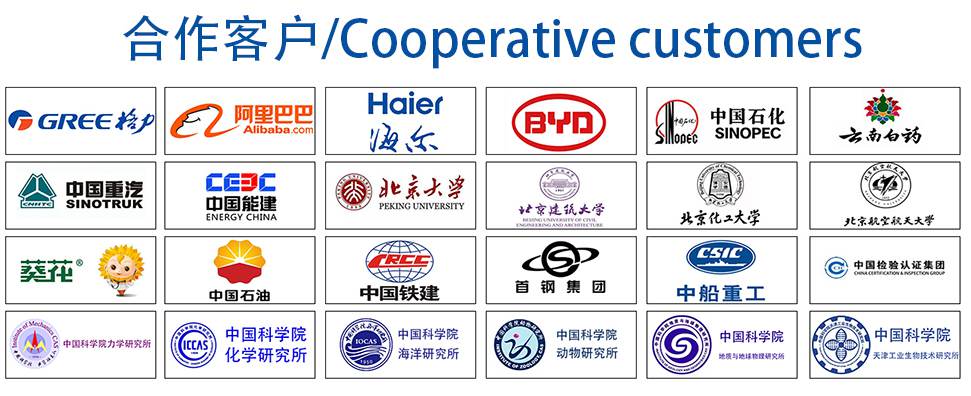