电动汽车驱动电机用冷轧无取向电工钢带(片)检测的重要性
随着新能源汽车产业的快速发展,电动汽车驱动电机的高效性和可靠性成为技术竞争的核心。作为电机核心材料之一,冷轧无取向电工钢带(片)的性能直接影响电机的能效、功率密度及运行稳定性。该材料需具备低铁损、高磁导率、良好的机械强度等特性,以确保电机在高速、高负载、复杂工况下的长期稳定运行。因此,对冷轧无取向电工钢带(片)进行系统性检测,是保障电机性能、延长使用寿命及满足行业标准的关键环节。
核心检测项目及方法
1. 磁性能检测
磁性能是电工钢的核心指标,主要包括铁损(P1.5/50、P1.0/400)和磁感应强度(B50)。检测需采用爱普斯坦方圈法或单片测试仪,依据IEC 60404、GB/T 3655等标准,模拟实际工况下的交变磁场,测量单位质量铁损及特定磁场强度下的磁感值。重点验证材料在高频(400Hz以上)下的磁化与损耗特性,以适应电动汽车驱动电机的高转速需求。
2. 机械性能检测
包括抗拉强度、屈服强度、延伸率和硬度测试。通过万能材料试验机和维氏硬度计,评估材料在冲压、叠装工艺中的成形性与尺寸稳定性。延伸率需≥20%以确保加工时无开裂,抗拉强度通常要求350-550MPa,平衡磁性能与机械强度。
3. 涂层性能检测
绝缘涂层的附着力、耐腐蚀性和耐热性是关键检测项。采用划格法(ASTM D3359)测试涂层附着力,盐雾试验(GB/T 10125)评估耐腐蚀能力,高温烘烤(200℃×1h)后观察涂层是否起泡或脱落,确保电机长期运行中绝缘性能不退化。
4. 化学成分分析
通过光谱分析仪检测硅(Si)、铝(Al)、锰(Mn)等合金元素含量。硅含量(2.5%-3.5%)直接影响电阻率和铁损,需严格控制;残余元素(C、S、P)需低于0.005%以减少磁时效风险。
5. 尺寸与形位公差检测
包括厚度公差(±0.02mm)、宽度公差(±0.3mm)及不平度(≤1.5mm/m)。使用激光测厚仪、影像测量仪等设备,确保钢带(片)在高速冲压和叠片工艺中的一致性,避免因尺寸偏差导致电机气隙不均或噪音问题。
检测标准与设备要求
当前主流检测标准包括IEC 60404系列、GB/T 2521、JIS C 2552及车企定制化规范。实验室需配备交直流磁性能测试系统、扫描电镜(SEM)用于晶粒观察、X射线衍射仪(XRD)分析织构,以及环境模拟试验箱等设备,形成从材料微观结构到宏观性能的全维度检测能力。
结论
随着800V高压平台、碳化硅电驱系统等技术的普及,对冷轧无取向电工钢带(片)的性能要求持续升级。通过精准的检测体系优化材料磁畴结构、降低高频损耗、提升机械强度,将成为推动下一代高功率密度电机发展的核心支撑。未来,检测技术将向在线实时监测、人工智能辅助分析等方向延伸,进一步提升质量控制效率与精度。
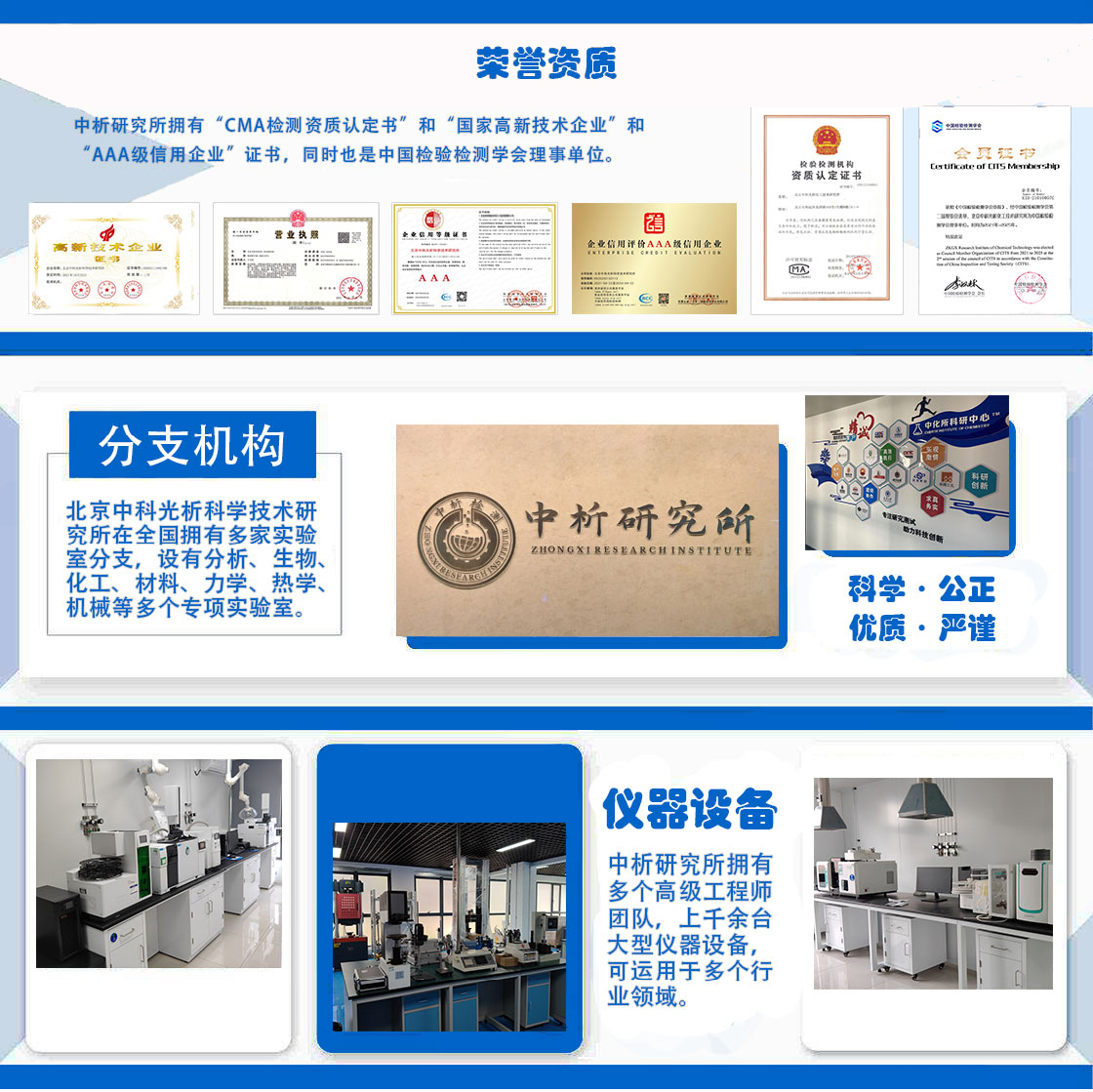
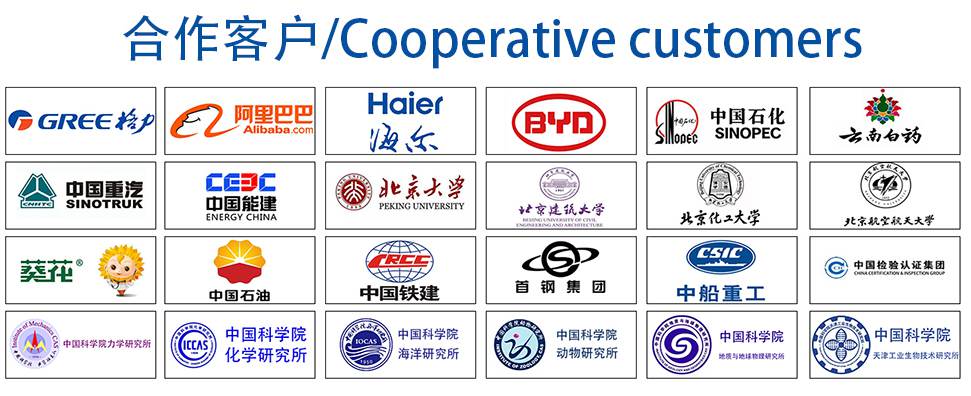