套管和油管检测的关键作用与技术要点
在石油天然气开采与输送系统中,套管和油管作为核心承压部件,承担着支撑井壁、隔离地层流体、保障油气传输等重要职能。随着油气田开发深度增加和工况环境复杂化,套管和油管的完整性直接影响着生产安全与经济效益。通过系统化的检测手段,能够有效识别材料缺陷、腐蚀损伤及结构失效风险,为设备维护和寿命预测提供科学依据,已成为油气田全生命周期管理中不可或缺的技术环节。
核心检测项目体系
针对套管和油管的检测体系主要包括以下七大类关键技术指标:
1. 几何尺寸检测
采用激光扫描仪与数字游标卡尺对管体外径、壁厚、椭圆度进行三维测量,重点检测螺纹加工精度是否符合API SPEC 5B标准。通过纵向拉伸试验验证接箍连接强度,确保各规格参数满足API SPEC 5CT规范要求。
2. 材料性能分析
运用直读光谱仪进行材料化学成分检测,验证C、Mn、Cr等元素的配比是否达标。通过万能试验机开展拉伸、冲击、硬度等机械性能测试,配合金相显微镜分析材料微观组织结构,确保材料具备足够的强度储备和韧性指标。
3. 密封完整性验证
采用液压试验装置进行承压检测,按照API RP 5C5标准实施多级压力循环测试。应用氦质谱检漏仪对螺纹连接部位进行气密封检测,配合数字图像相关技术(DIC)分析应力分布状态,确保承压密封系统在极端工况下的可靠性。
4. 腐蚀损伤评估
使用电磁超声测厚仪(EMAT)进行管体腐蚀扫描,结合交流电压降(ACVG)技术定位腐蚀热点。通过三维轮廓扫描构建腐蚀形貌图谱,采用有限元分析软件评估剩余强度,为腐蚀管段的修复决策提供量化依据。
5. 无损检测技术应用
集成多频涡流检测(MFEC)与相控阵超声波检测(PAUT)技术,实现对管体表面裂纹和内部缺陷的立体化检测。应用磁粉检测(MT)强化螺纹部位的表面缺陷识别,配合数字射线检测(DR)进行焊缝质量验证,形成多维度缺陷检测网络。
6. 力学性能模拟测试
通过全尺寸试验机模拟井下复合载荷环境,开展挤毁试验、弯曲试验和内压爆破试验。采用分布式光纤传感技术实时监测管体应变分布,结合数字孪生技术构建力学响应模型,准确预测管柱在不同工况下的力学行为。
7. 特殊环境适应性检测
针对含硫油气田开展硫化物应力腐蚀开裂(SSCC)试验,通过四点弯曲法评估材料抗SSC性能。对深海井管进行高压舱模拟试验,检测材料在高压低温环境下的性能变化。开发酸性介质加速腐蚀试验装置,评估涂层体系在CO₂/H₂S环境中的防护效能。
检测技术发展趋势
随着智能检测装备的发展,基于工业机器人的自动化检测系统和数字孪生评估平台正在改变传统检测模式。电磁声传感器(EMAT)与导波检测技术的集成应用,可实现长管段的快速筛查。三维数字成像与AI缺陷识别算法的结合,大幅提升了检测效率和结果判读的准确性,推动着油气田管柱检测向智能化、数字化方向持续演进。
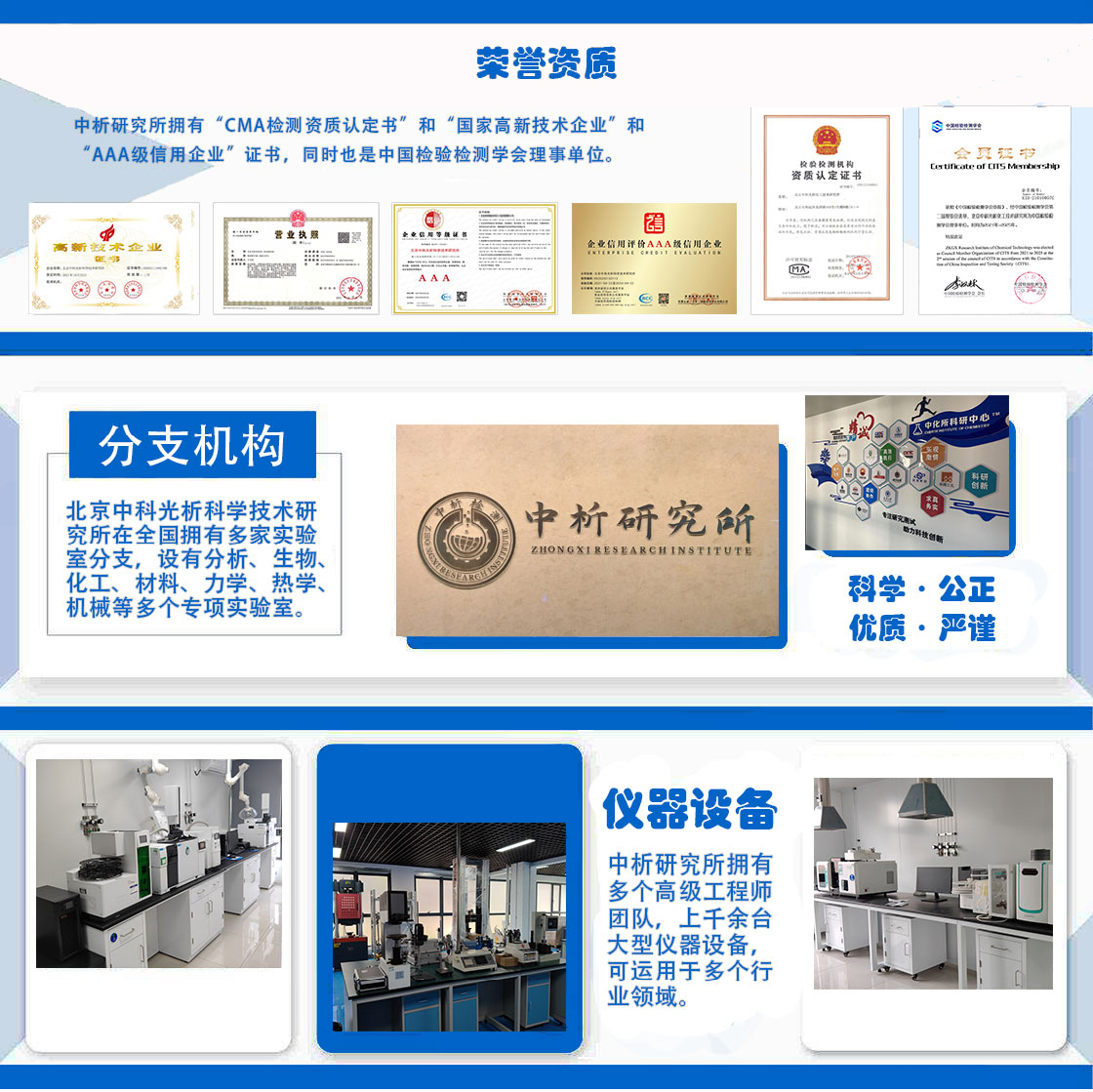
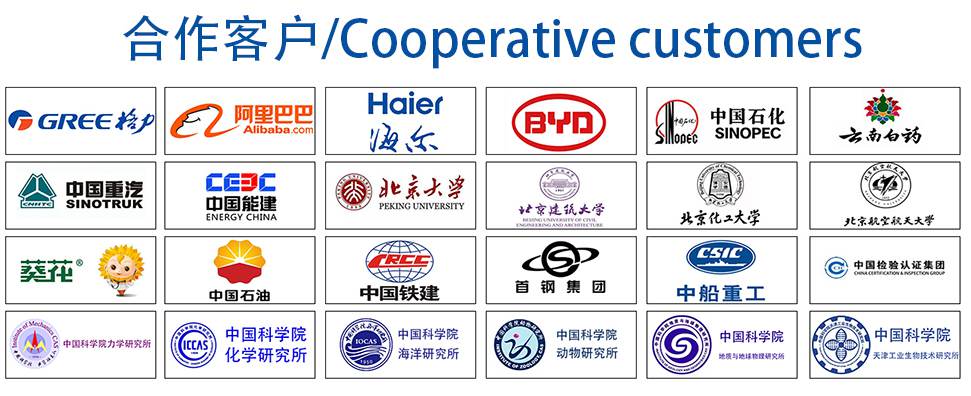