工业设备检测的重要性与核心目标
在现代化工业生产中,设备的高效稳定运行是保障企业生产效率和经济效益的关键。工业设备检测作为预防性维护的核心环节,旨在通过系统化的技术手段识别设备潜在隐患,避免因突发故障导致的停机损失和安全事故。随着智能化、数字化技术的发展,检测手段从传统的人工巡检逐步转向自动化、数据驱动的模式,涵盖机械性能、电气系统、材料状态等多维度分析。通过科学规范的检测项目,企业能够实现设备寿命延长、能耗降低及生产环境安全性的全面提升。
工业设备检测的核心项目分类
1. 外观与结构完整性检测
包括设备外壳腐蚀程度评估、连接件松动检查、焊缝裂纹探测等,结合目视检测和三维扫描技术,快速定位物理损伤区域。针对高温、高压设备还需进行密封性测试,防止介质泄漏风险。
2. 性能参数动态监测
通过传感器实时采集振动、噪声、温度、压力等关键参数,建立基线数据库进行趋势分析。例如使用红外热成像仪检测电机轴承过热现象,或通过振动频谱分析预判齿轮箱磨损状态。
3. 无损检测技术应用
采用超声波探伤、磁粉检测、X射线成像等方法对设备内部缺陷进行非破坏性检查。例如压力容器壁厚的超声波测量,管道焊缝的渗透检测,以及涡轮叶片内部微裂纹的工业CT扫描。
4. 润滑与磨损分析
定期提取润滑油样本进行铁谱分析和光谱检测,判断金属磨粒成分及浓度变化,预判轴承、齿轮等运动部件的磨损阶段。同时监测润滑油的黏度、酸碱值等指标,优化换油周期。
5. 电气系统安全检测
包括绝缘电阻测试、接地连续性验证、谐波分析等,使用绝缘电阻测试仪、电能质量分析仪等专业设备,确保配电系统符合安全规范,预防短路或电弧故障发生。
6. 环境适应性测试
针对特殊工况设备开展温湿度循环试验、防爆性能验证、盐雾腐蚀测试等项目,确保设备在极端环境下的可靠性。例如海上平台设备需通过IP68防护等级认证。
7. 智能化预测性维护系统
集成物联网(IoT)传感器和大数据分析平台,建立设备健康状态评分模型。通过机器学习算法预测剩余使用寿命(RUL),实现从定期检修到状态维修的转变。
检测流程标准化与优化策略
企业需根据设备类型、使用频率和工况特点制定分级检测计划,结合行业标准(如ISO 17359)建立检测规程。同时应注重历史检测数据的积累与分析,通过PDCA循环持续改进检测方案,将检测结果与备件管理、维修决策深度融合,最终构建全生命周期的设备管理体系。
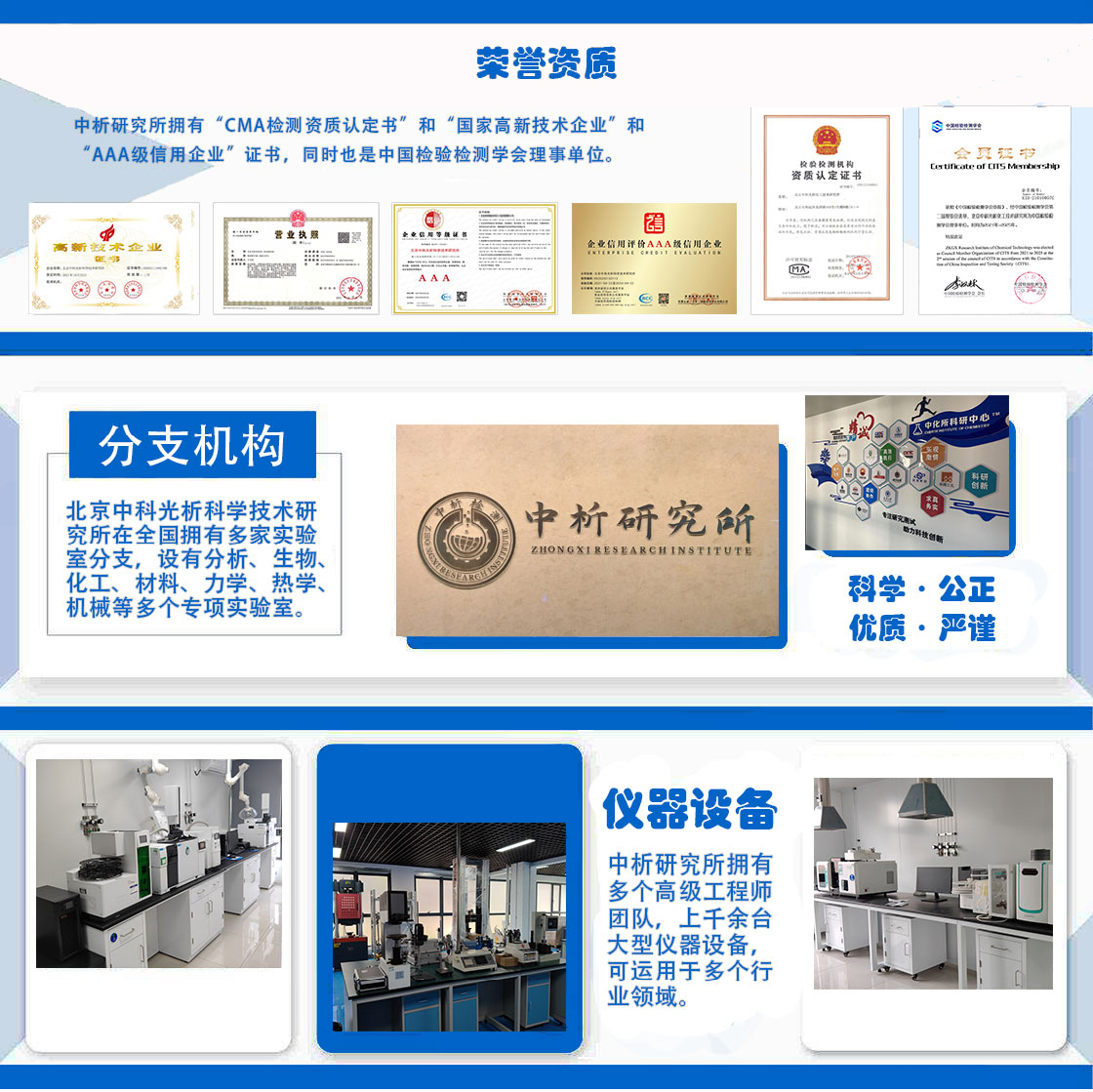
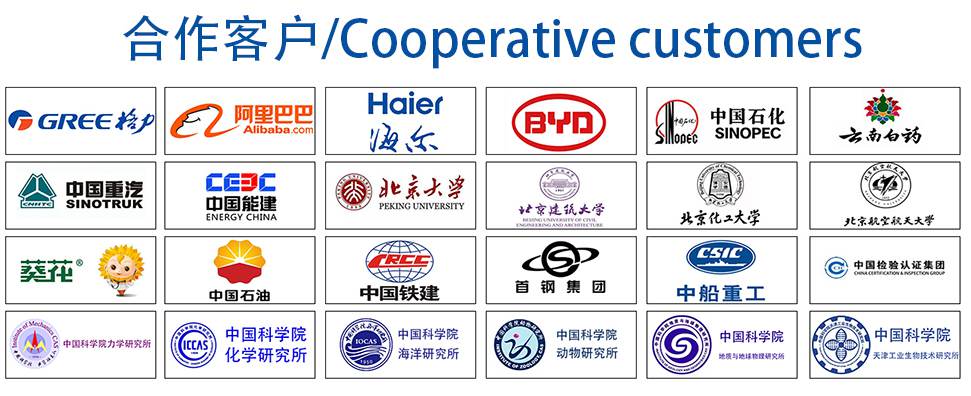