工业场所电气与电子设备检测的重要性
在现代化工业生产中,电气和电子设备的稳定运行是保障生产效率、人员安全及工艺质量的核心要素。工业环境通常具有高温、高湿、粉尘、振动等复杂工况,设备长期暴露于此可能引发绝缘老化、接触不良、电磁干扰等问题。因此,依据国际标准(如IEC 60079、GB/T 3836等)和行业规范,对工业场所的电气与电子设备进行系统性检测成为控制风险、预防事故的重要手段。检测项目需涵盖安全性能、功能稳定性、环境适应性及能效表现四大维度,确保设备在全生命周期内满足生产需求。
关键检测项目分类与实施
1. 电气安全性能检测
包括绝缘电阻测试(500V/1000V兆欧表)、接地连续性验证(≤0.1Ω)、耐压强度试验(2倍额定电压+1000V)等,重点防范漏电、短路风险。针对防爆设备还需进行隔爆面间隙测量和外壳机械强度测试。
2. 电磁兼容性(EMC)检测
通过辐射发射测试(30MHz-1GHz)和抗扰度试验(如静电放电4kV、浪涌冲击2kV),评估设备在工业电磁复杂环境下的抗干扰能力和对其他设备的影响,确保PLC、变频器等敏感装置可靠运行。
3. 环境适应性检测
模拟高温(+55℃)、低温(-25℃)、湿热循环(95%RH)、IP防护等级(防尘防水)、机械振动(5-500Hz)等严苛工况,验证设备结构密封性和元件耐久性。尤其关注接线端子氧化、PCB板结露等潜在失效模式。
4. 能效与功能验证
对电机、变频器等设备开展负载特性测试(效率≥IE3)、功率因数测量(≥0.9),同时进行控制逻辑验证(HMI人机交互测试)、故障诊断功能模拟,确保能耗指标与工艺控制要求相符。
5. 防爆设备专项检测
依据ATEX指令和GB 3836标准,对隔爆型、增安型设备进行外壳耐压试验(1.5倍参考压力)、温度组别验证(T1-T6分级)、电缆引入装置夹紧测试等,防止爆炸性气体环境中的引燃风险。
检测周期与智能化趋势
常规设备建议每6-12个月开展预防性检测,高危区域设备需缩短至3个月。随着工业物联网(IIoT)技术发展,在线监测系统可实时采集温度、电流谐波等参数,结合AI算法实现故障预警,推动检测模式从定期维护向预测性维护转型。
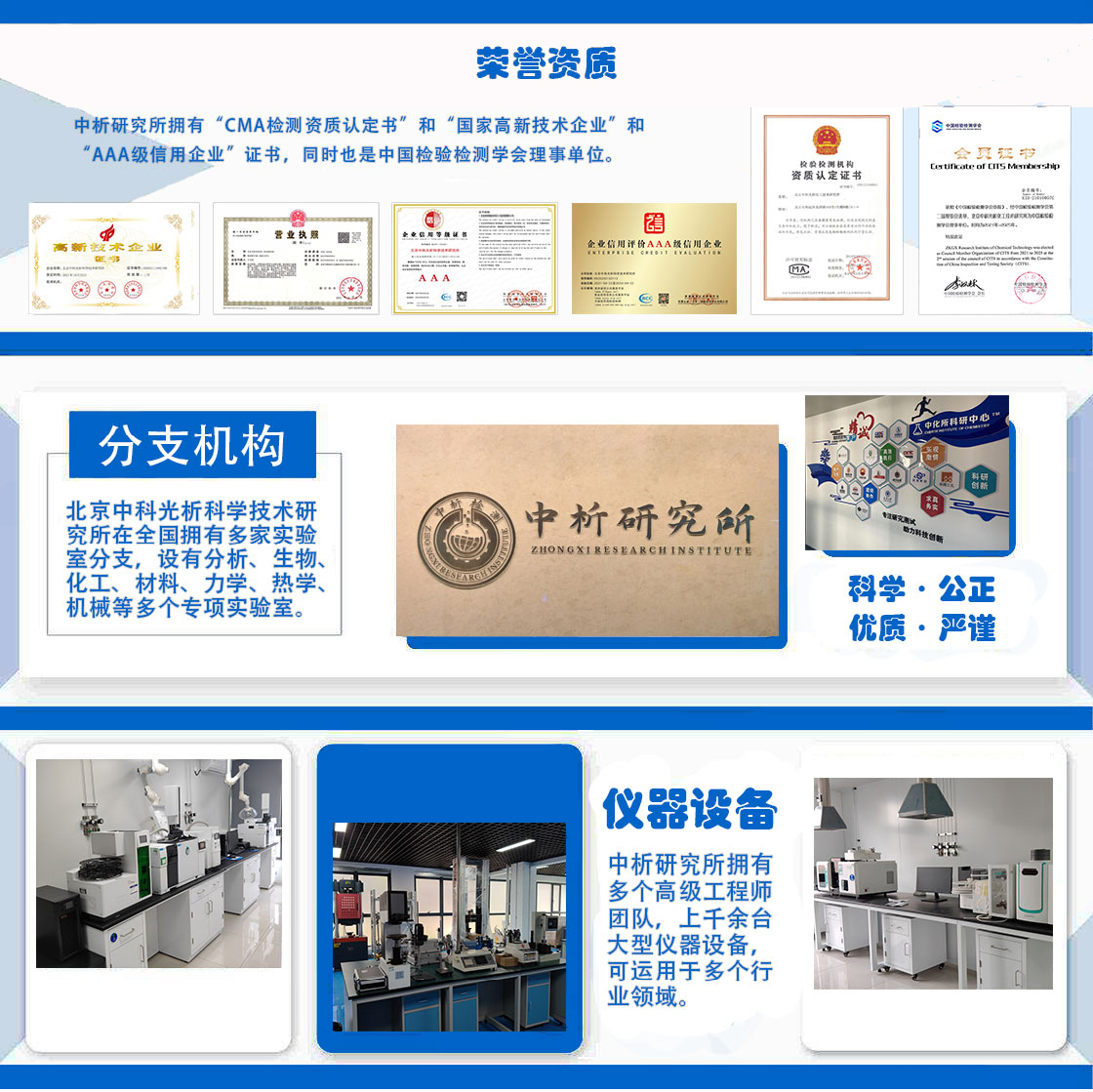
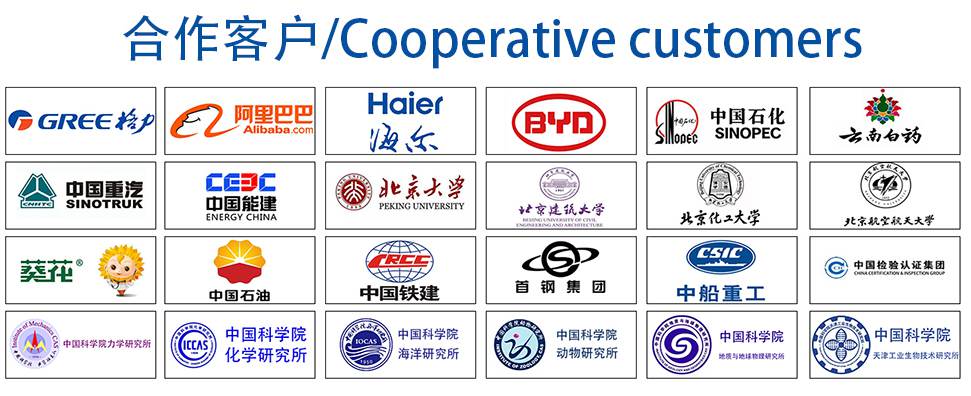