静电复印(打印)设备用刮板检测的重要性
静电复印设备(如激光打印机、复印机)的核心工作原理依赖于感光鼓、碳粉及刮板的协同作用。其中,刮板作为关键的清洁组件,承担着清除感光鼓表面残留碳粉、保证成像质量的重要任务。若刮板存在材质缺陷、尺寸偏差或性能不足,可能导致打印图像出现条纹、底灰、重影等问题,甚至加速感光鼓磨损,缩短设备使用寿命。因此,对刮板进行系统性检测是确保设备高效运行和输出质量的核心环节。
检测工作需覆盖原材料、物理性能、化学稳定性等多个维度,并严格遵循行业标准(如ISO 19752、ASTM相关规范)。尤其在高速打印设备和精密成像场景中,刮板的微小瑕疵可能被快速放大,引发连锁故障。通过科学的检测流程,企业可筛选出符合要求的刮板产品,降低设备维护成本,提升用户体验。
刮板检测的关键项目及方法
1. 材质成分与均匀性检测
刮板通常由聚氨酯(PU)、硅橡胶等高分子材料制成。需通过光谱分析(如FTIR)、热重分析(TGA)验证材料成分是否达标,并利用显微镜观察材料断面是否存在气泡、杂质或分层现象。材料均匀性直接影响刮板的抗疲劳性和耐磨性。
2. 尺寸精度与几何形状检测
使用精密测厚仪、投影仪或三坐标测量仪(CMM)检测刮板的厚度、长度、刃口角度等参数。例如,刃口直线度偏差需控制在±0.02mm以内,边缘倒角半径需符合图纸要求,以确保与感光鼓的贴合度。
3. 硬度与弹性模量测试
采用邵氏硬度计(A型或D型)测量刮板硬度,典型值范围为50-90 Shore A。动态机械分析(DMA)可测定弹性模量,确保刮板在长期压力下不易变形,同时保持适度的柔韧性以保护感光鼓表面。
4. 耐磨性与寿命测试
通过模拟运行实验,将刮板安装于测试设备中连续工作5万至10万页,观察刃口磨损量(需≤0.1mm)及性能变化。同步监测打印样张的清洁度,防止因磨损导致碳粉残留。
5. 表面粗糙度与摩擦系数检测
使用表面轮廓仪测量刃口区域Ra值(通常要求≤0.8μm),并通过摩擦试验机测定与感光鼓涂层的动/静摩擦系数(标准范围0.2-0.5)。过高摩擦系数会加剧磨损,而过低则可能导致清洁不彻底。
6. 耐化学性与环境适应性测试
将刮板浸泡于碳粉溶剂(如丙酮、异丙醇)中24小时,检测其体积膨胀率(需≤3%)和硬度变化。同时进行高低温循环试验(-10℃至60℃),验证刮板在极端环境下的性能稳定性。
7. 安装适配性与动态压力测试
通过夹具模拟实际装配状态,检测刮板与支架的配合间隙及压力分布。使用压力传感器测量刃口对感光鼓的接触压力(通常为20-50g/cm),确保压力均匀且符合设备设计要求。
检测数据管理与质量追溯
现代检测体系需结合数字化管理,对每批次刮板的检测结果建立数据库,包括批次号、材料供应商、关键参数曲线等。通过SPC(统计过程控制)分析数据趋势,提前预警潜在风险。对于不合格品,需追溯至生产环节(如混炼工艺、硫化时间)进行工艺优化,形成闭环质量控制。
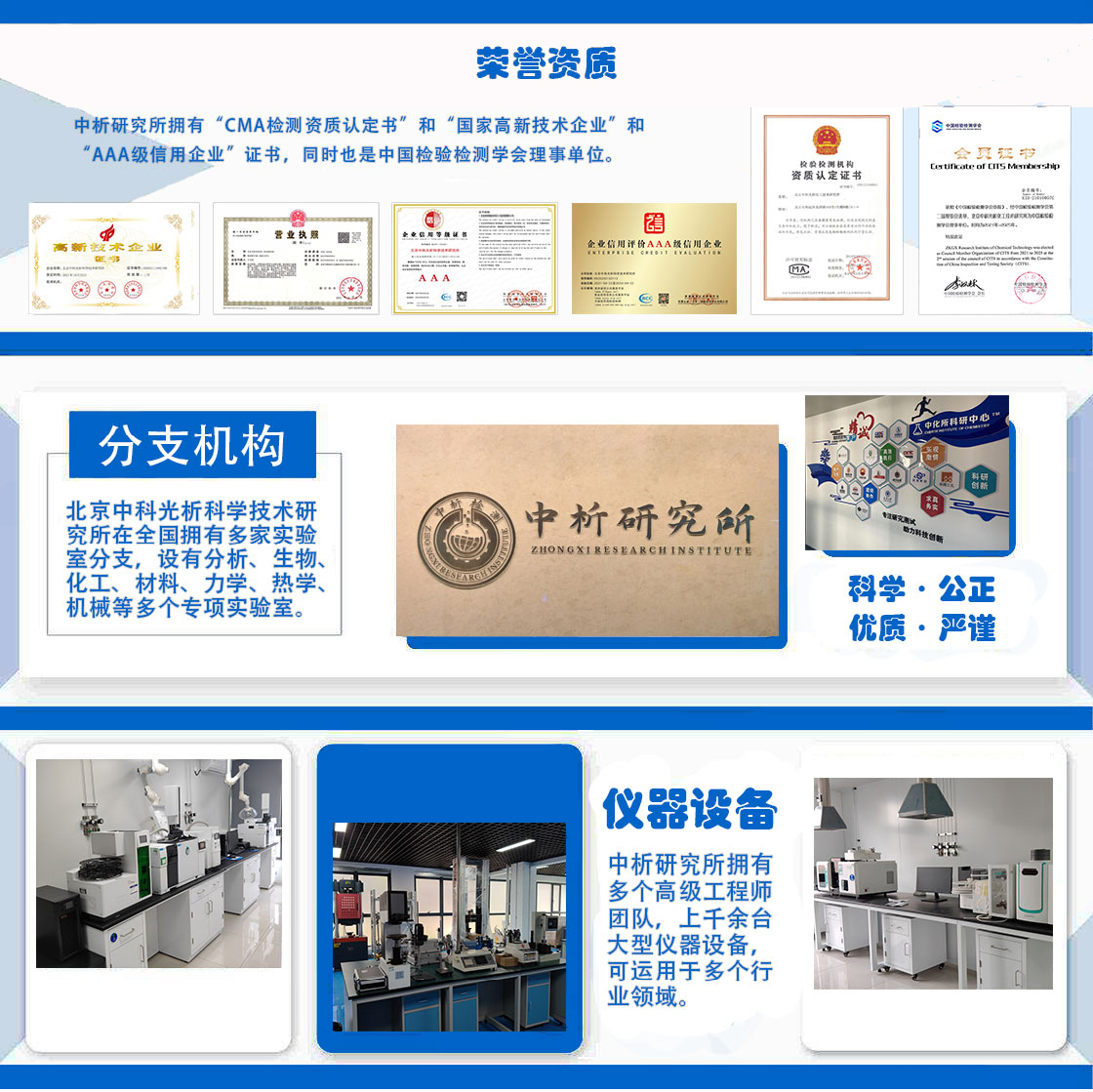
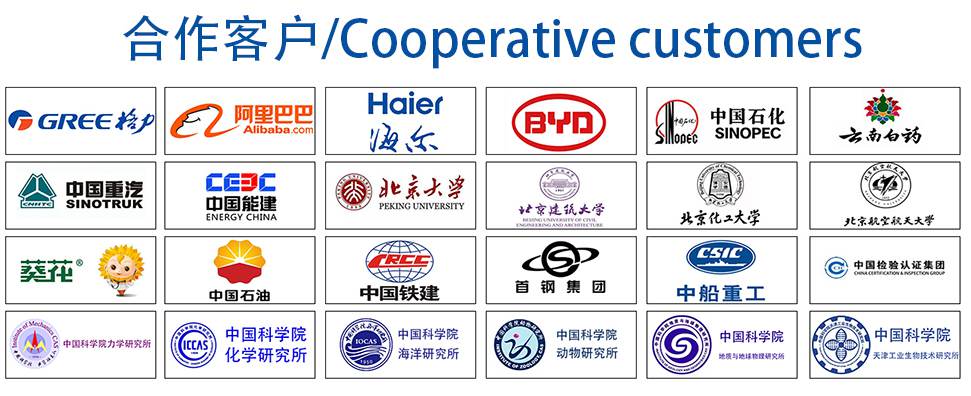