电动汽车用锂离子电池检测的关键项目与技术标准
随着电动汽车(EV)产业的快速发展,锂离子电池作为其核心动力源,其性能、安全性及可靠性受到广泛关注。为确保电池满足车辆运行需求并降低安全隐患,国际和国内机构建立了全面的检测体系。电池检测覆盖从电化学性能到环境适应性的多维指标,贯穿研发、生产到使用的全生命周期。当前,中国、美国、欧盟等均制定了严格的强制性标准,如GB 38031-2020《电动汽车用动力蓄电池安全要求》和UN R100法规,重点防范热失控、短路等风险。
一、安全性能检测
安全检测是锂离子电池测试的首要环节。短路测试模拟电池正负极意外接触场景,要求电池在外部短路后不起火、不爆炸;过充/过放测试验证保护系统在异常充放电状态下的响应能力,需触发电压保护阈值并切断电路。机械安全测试包含针刺、挤压、振动等项目,例如针刺测试需用直径3-8mm钢针以25mm/s速度穿透电芯,观察是否发生热失控。2023年新国标新增热扩散测试,要求电池包在单电芯热失控后5分钟内不引发整车起火。
二、电化学性能检测
能量密度测试通过恒流充放电法测量电池单位质量/体积的储能能力,高端EV电池能量密度已突破300Wh/kg;循环寿命测试需完成上千次充放电循环(如0.5C充放,100%DOD),容量保持率需≥80%;倍率性能测试评估电池在高功率场景下的表现,快充型电池需支持4C以上充电速率。内阻测试采用交流阻抗法,要求新电池内阻值低于3mΩ,高内阻会显著降低能效。
三、环境适应性检测
温度循环测试模拟-40℃至85℃极端气候,验证电池密封性和材料稳定性;高低温充放电测试规定不同温区的性能阈值,如-20℃下放电容量不低于常温的70%。湿热测试在85%RH湿度环境下持续720小时,检测绝缘电阻是否≥100MΩ。海拔模拟测试通过减压舱验证2000米以上高海拔地区的散热与气压平衡能力。
四、电池管理系统(BMS)功能验证
BMS作为电池的"大脑",需通过SOC估算精度测试(误差≤3%)、均衡功能测试(单体电压差≤20mV)及故障诊断测试。热管理测试包含液冷系统流量控制、加热膜响应速度等指标,要求电池包温差控制在±2℃以内。过温保护测试需在电芯温度达到60℃时0.5秒内切断回路。
五、智能化检测技术发展
行业正推动AI赋能的检测革新,X射线CT技术实现电芯内部缺陷三维成像,检测精度达微米级;大数据平台通过分析百万级测试数据建立寿命预测模型,准确率超90%。无线BMS测试系统可同步采集128个电芯数据,采样频率提升至10kHz。2024年欧盟拟推行电池数字护照制度,要求全生命周期检测数据上链存储。
动力电池检测体系的持续完善,不仅推动了材料创新与工艺升级,更构建起电动汽车安全发展的技术屏障。随着固态电池、钠离子电池等新型技术的突破,检测标准也将同步迭代,为新能源交通提供更坚实的质量保障。
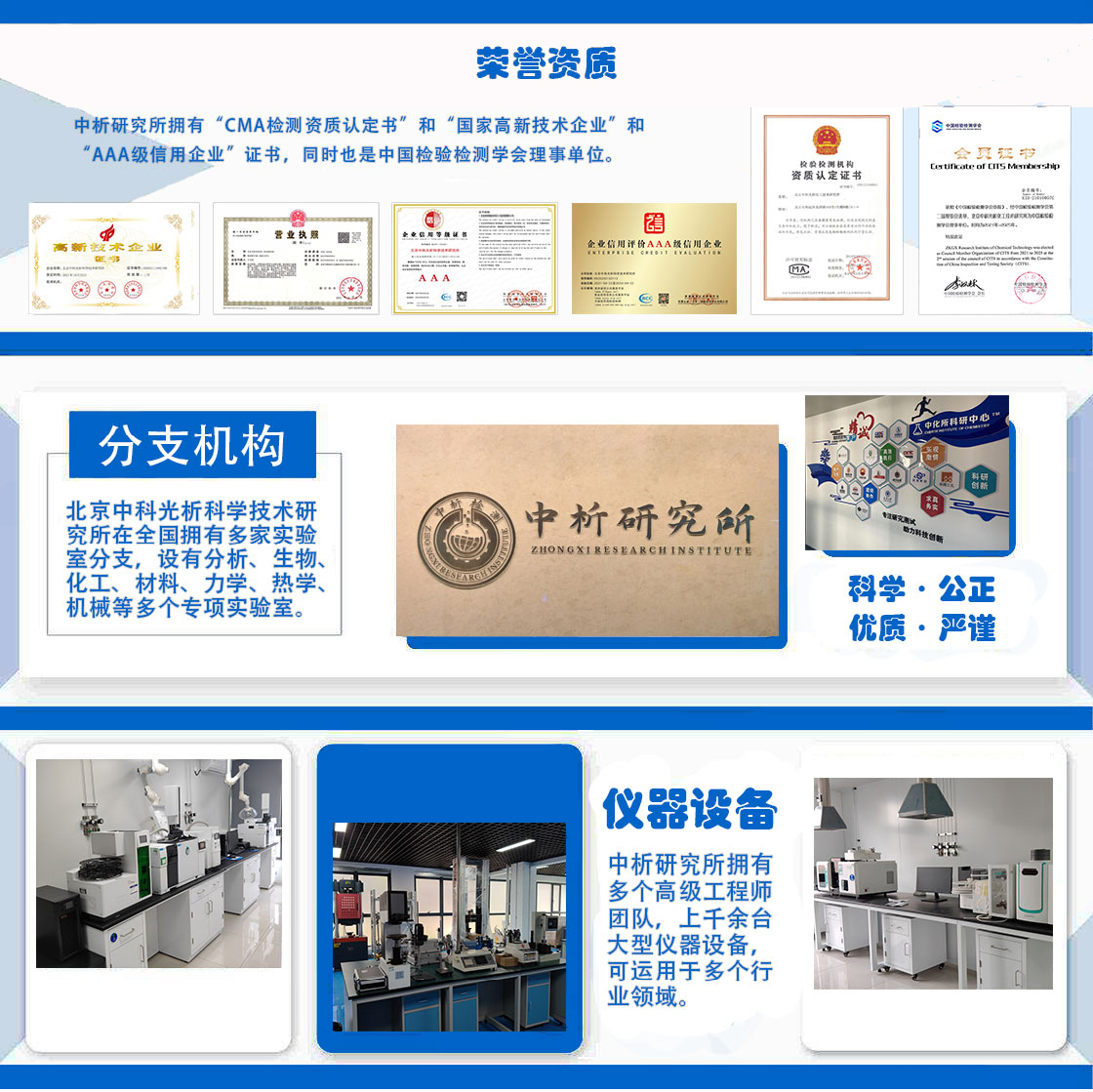
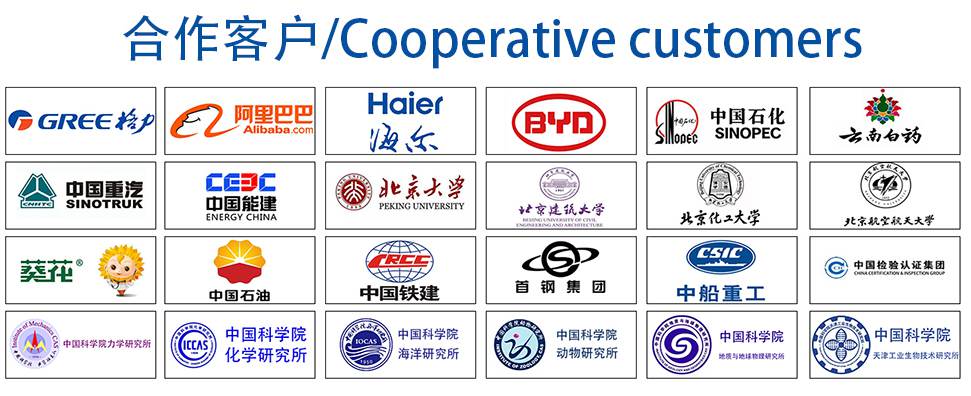