多晶体材料检测的核心价值与应用场景
多晶体材料是由大量微小晶粒随机取向组成的固态材料,广泛应用于航空航天、电子器件、能源装备等领域。其性能受晶粒尺寸、取向分布、晶界状态及内部缺陷的直接影响。通过科学检测手段对材料微观结构和宏观性能进行系统性评估,能够有效优化材料加工工艺、预测服役寿命并提升产品可靠性。随着现代工业对材料性能要求的不断提高,多晶体材料检测已成为材料研发、质量控制和故障分析的关键技术支撑。
核心检测项目与技术方法
1. 晶体结构分析
采用X射线衍射(XRD)和电子背散射衍射(EBSD)技术,精确测定材料的晶格常数、晶体对称性和相组成。同步辐射光源的引入可将空间分辨率提升至纳米级别,特别适用于薄膜材料和纳米晶体系的分析。
2. 晶粒尺寸与取向分布
通过扫描电镜(SEM)结合EBSD系统实现三维取向成像,配合图像分析软件统计晶粒尺寸分布。透射电镜(TEM)可观测亚微米级晶界结构,揭示晶粒生长动力学机制。
3. 残余应力检测
运用中子衍射法和X射线应力分析仪,对材料加工/服役过程中产生的残余应力场进行非破坏性测量。超声表面波技术可快速评估大型构件的应力分布状态。
4. 晶界特性表征
采用原子探针层析技术(APT)分析晶界处元素偏聚行为,结合高分辨TEM观察晶界位错结构。电子能量损失谱(EELS)可定量检测晶界处的化学键合状态。
5. 缺陷检测与评估
超声相控阵技术实现毫米级孔洞/裂纹的精准定位,同步辐射CT技术可重建材料内部三维缺陷网络。热激励红外检测(LOCKIN-THERMOGRAPHY)有效识别近表面微裂纹。
前沿检测技术发展趋势
随着人工智能技术的深度融合,深度学习算法已应用于EBSD图像自动标定和缺陷模式识别。原位检测装置的发展使得在高温/应力加载条件下实时观察晶粒演变成为可能。基于大数据分析的晶体结构预测模型正在革新传统材料研发范式。
质量控制与标准化实践
依据ASTM E112晶粒度测定标准、ISO 21479残余应力测试规范等行业标准,建立从原料入厂到成品出厂的全流程检测体系。引入统计过程控制(SPC)方法,将晶粒尺寸标准差、取向分布熵值等参数纳入过程质量监控指标。
通过构建覆盖材料-工艺-性能的全维度检测方案,企业可显著提升产品合格率,降低质量成本。当前国际领先实验室已实现检测数据与数字孪生系统的实时交互,为智能工厂建设提供关键支撑。
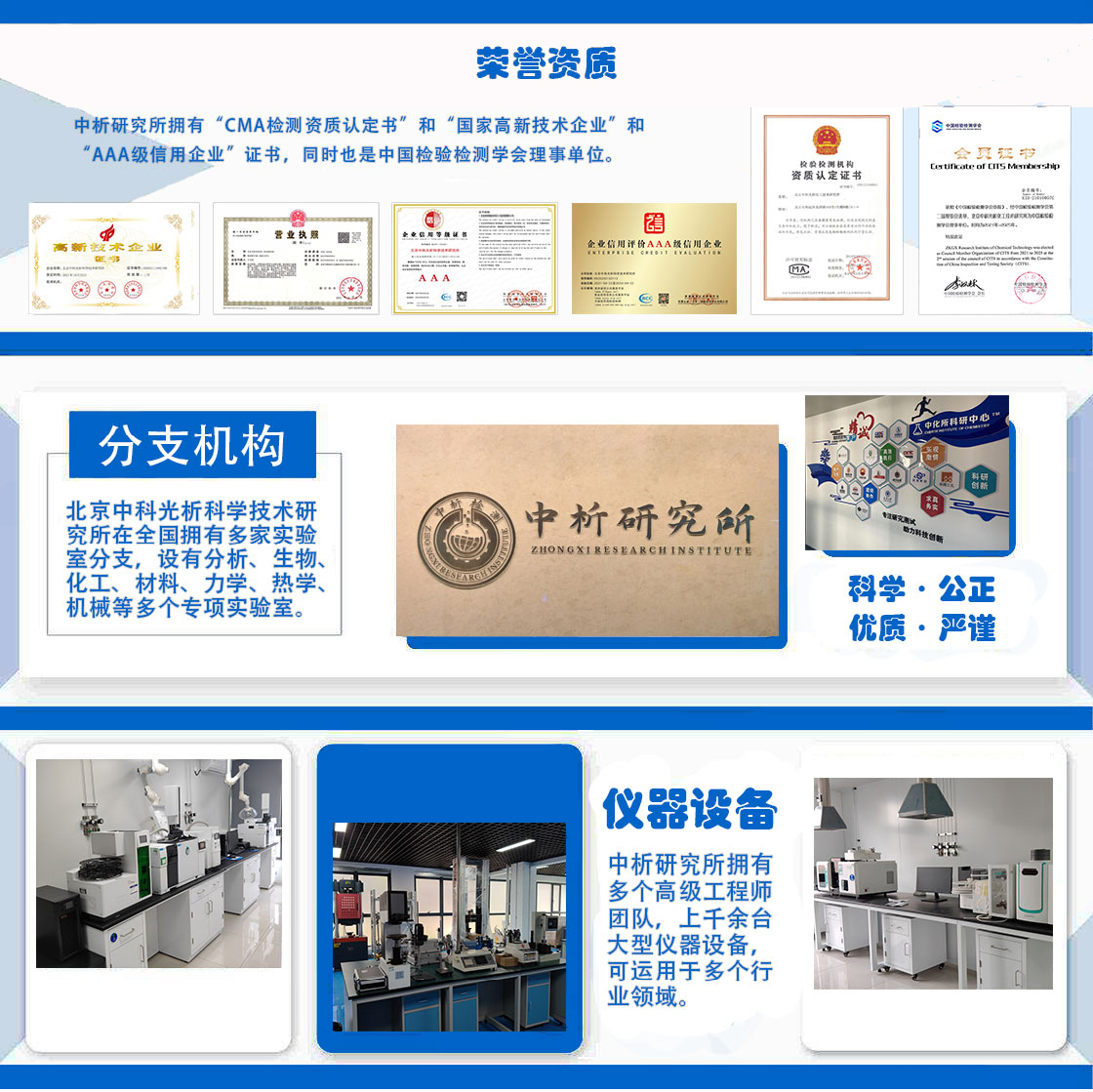
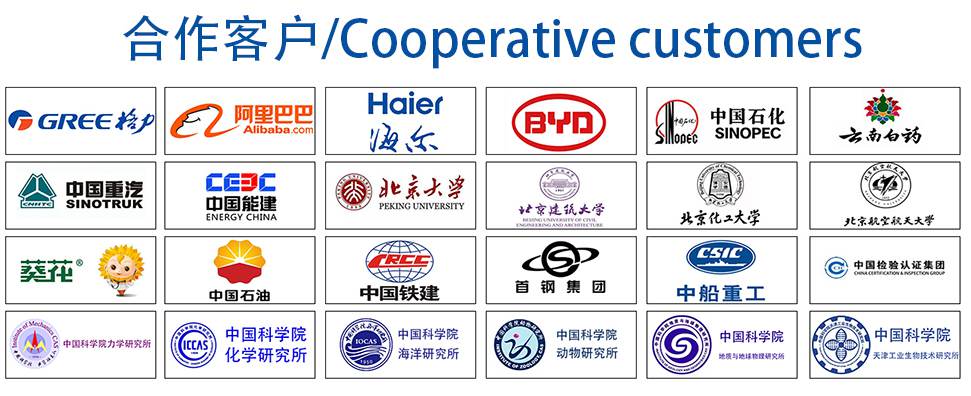