丸子成型机检测的重要性与核心项目解析
在食品加工行业中,丸子成型机作为肉丸、鱼丸等球形食品的核心生产设备,其性能稳定性直接关系到产品成型质量与生产效率。随着《GB 16798-2018 食品机械安全要求》等国家标准的实施,对丸子成型机进行系统性检测已成为保障食品安全、提升企业竞争力的必要环节。通过科学的检测流程,可有效规避设备故障导致的原料浪费、规格偏差等风险,同时满足食品接触材料卫生标准等法规要求。
核心检测项目体系
1. 结构完整性检测
采用三维测量仪对模具尺寸进行0.01mm级精度检测,确保成型腔体直径偏差≤0.5mm。使用压力传感器测试液压系统稳定性,验证单位时间成型量是否达到标称值的±3%误差范围内。特别注意传动部件的同轴度检测,避免因偏心导致的震动异常。
2. 食品接触面合规性检测
按照GB 4806.7-2016标准,对不锈钢模具表面进行重金属迁移量测试,重点检测铅、镉、砷等有害物质析出量。使用表面粗糙度仪测量Ra值应≤0.8μm,确保无死角残留。对密封圈等橡胶部件进行挥发性有机物(VOC)检测,要求符合FDA 21 CFR 177.2600标准。
3. 电气安全性能检测
使用耐压测试仪进行1500V/1min绝缘强度试验,测量泄漏电流需<0.75mA。通过接地电阻测试仪验证保护接地连续性,阻值应≤0.1Ω。模拟电压波动(±10%)测试控制系统稳定性,要求成型重量偏差率≤2%。
4. 卫生设计符合性检测
依据EHEDG标准验证设备易清洁性:检查可拆卸部件占比是否>85%,使用内窥镜检查管道内壁焊接质量。进行微生物采样检测,设备清洗后菌落总数应<10CFU/cm²。特别关注出料口防滴漏设计有效性测试。
5. 动态性能测试
采用高速摄像系统(1000fps)记录成型过程,分析物料填充均匀度和脱模成功率。连续运行8小时测试稳定性,要求成型合格率≥98.5%。通过电子秤联机系统监测1000个样品重量,计算CPK值≥1.33。
检测周期与维护建议
建议每季度进行预防性检测,关键轴承部位每2000小时更换润滑脂。每次模具更换后需重新校准成型参数,年度大检应包含传动系统疲劳强度测试。保留完整的检测报告可作为ISO22000、HACCP等认证的重要佐证材料。
通过建立完善的丸子成型机检测体系,企业可有效降低停机损失30%以上,延长设备使用寿命40%,同时将产品不良率控制在0.3%以下,为食品安全生产提供可靠保障。
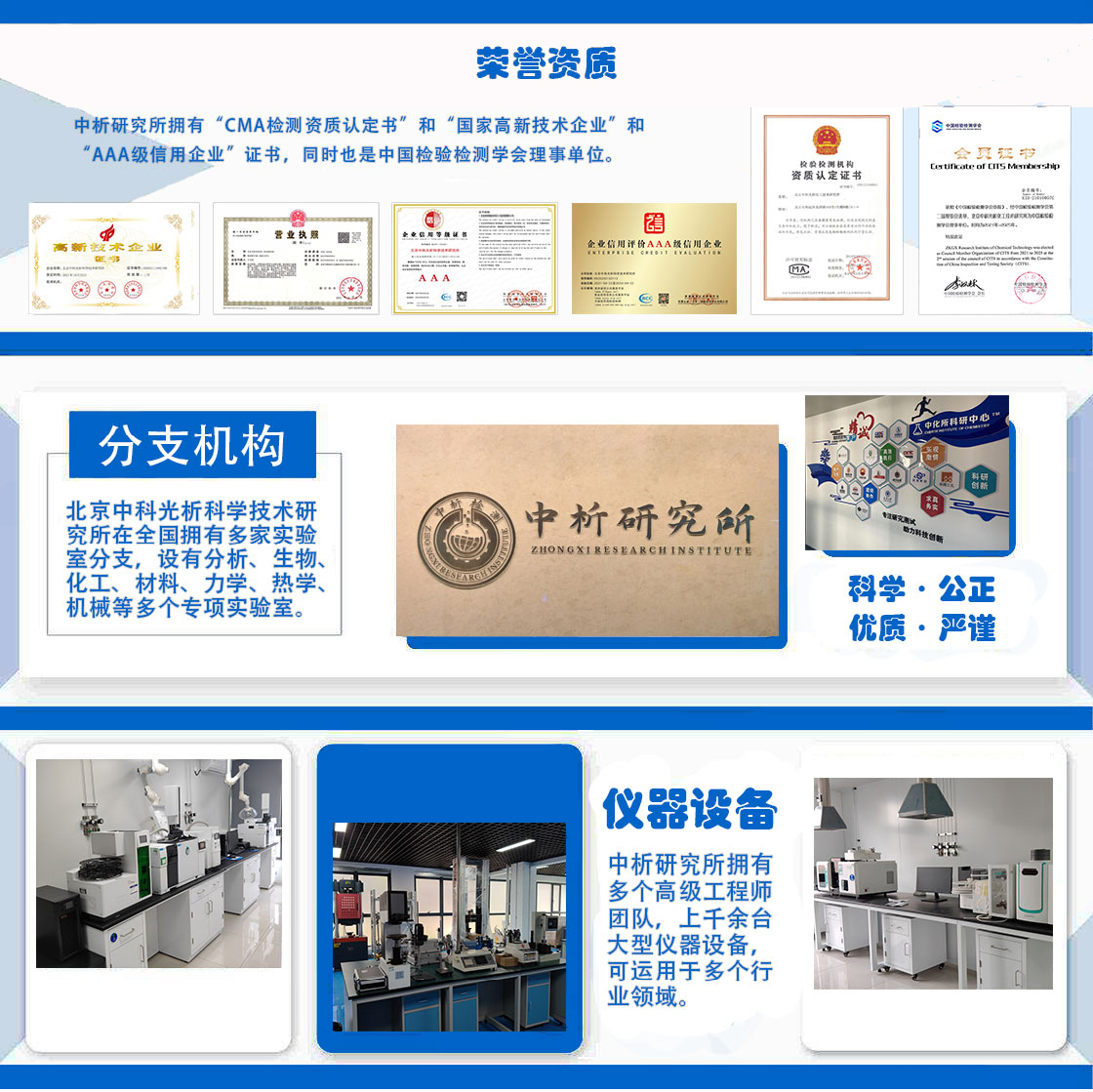
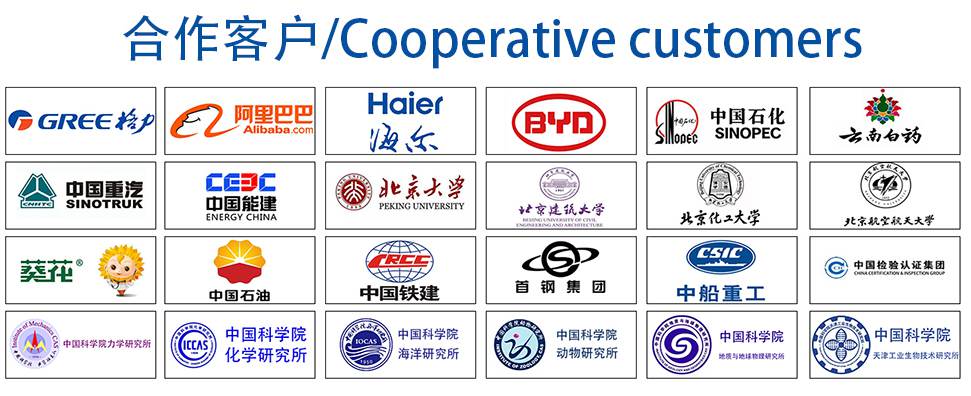