高速扭结机检测的必要性与核心内容
高速扭结机作为线材加工、电缆制造、金属丝编织等领域的关键设备,其运行精度和稳定性直接影响产品质量和生产效率。随着工业自动化程度的提升,设备转速和连续作业时间不断增加,对机械结构、电气系统及控制模块的可靠性提出了更高要求。定期开展高速扭结机检测,能够有效预防设备异常磨损、参数偏移等问题,降低停机风险,延长设备使用寿命,同时保障产品扭结均匀性、抗拉强度等核心指标符合标准。
核心检测项目及技术要求
1. 机械系统检测
包括主轴同心度校准(偏差≤0.02mm)、轴承润滑状态评估(油膜厚度≥10μm)、扭结模具磨损量测量(磨损深度≤0.1mm)以及传动齿轮啮合间隙检测。需采用激光对中仪、振动分析仪等工具,确保设备在8000rpm以上高速运转时无异常振动。
2. 电气与控制系统检测
重点验证伺服电机动态响应性能(响应时间<5ms)、变频器输出频率稳定性(波动率≤±0.5%)、PLC程序逻辑准确性,以及张力控制系统的闭环调节精度(误差<±2N)。通过示波器、数据采集卡记录运行波形,分析异常信号干扰源。
3. 工艺参数验证
针对不同线径(0.1-5mm)材料,测试扭结节距一致性(CV值≤3%)、扭结角度偏差(≤±1°)、断线率(<0.1次/万米)等指标。需使用光学投影仪测量成品几何参数,结合拉力试验机验证抗拉强度损失(<8%)。
4. 安全防护装置检测
检查急停按钮触发响应时间(<0.5s)、防护罩连锁开关有效性、过载保护阈值设定合理性(额定电流110%时动作)。需通过模拟故障测试,确保设备符合ISO 13849安全等级PLd要求。
5. 环境适应性检测
在温湿度循环(-10℃至50℃/30%-85%RH)条件下,验证设备启动特性、扭结精度保持能力,并检测散热系统效能(温升≤15K)。同时评估长期运行时的噪音水平(≤75dB(A))。
检测周期与数据管理建议
建议每500小时进行日常点检(含润滑、皮带张力等基础项),每3000小时开展全面检测并生成趋势分析报告。采用MES系统记录扭结力曲线、电机电流波形等数据,建立设备健康度预测模型,实现从被动维修向预防性维护的转型。
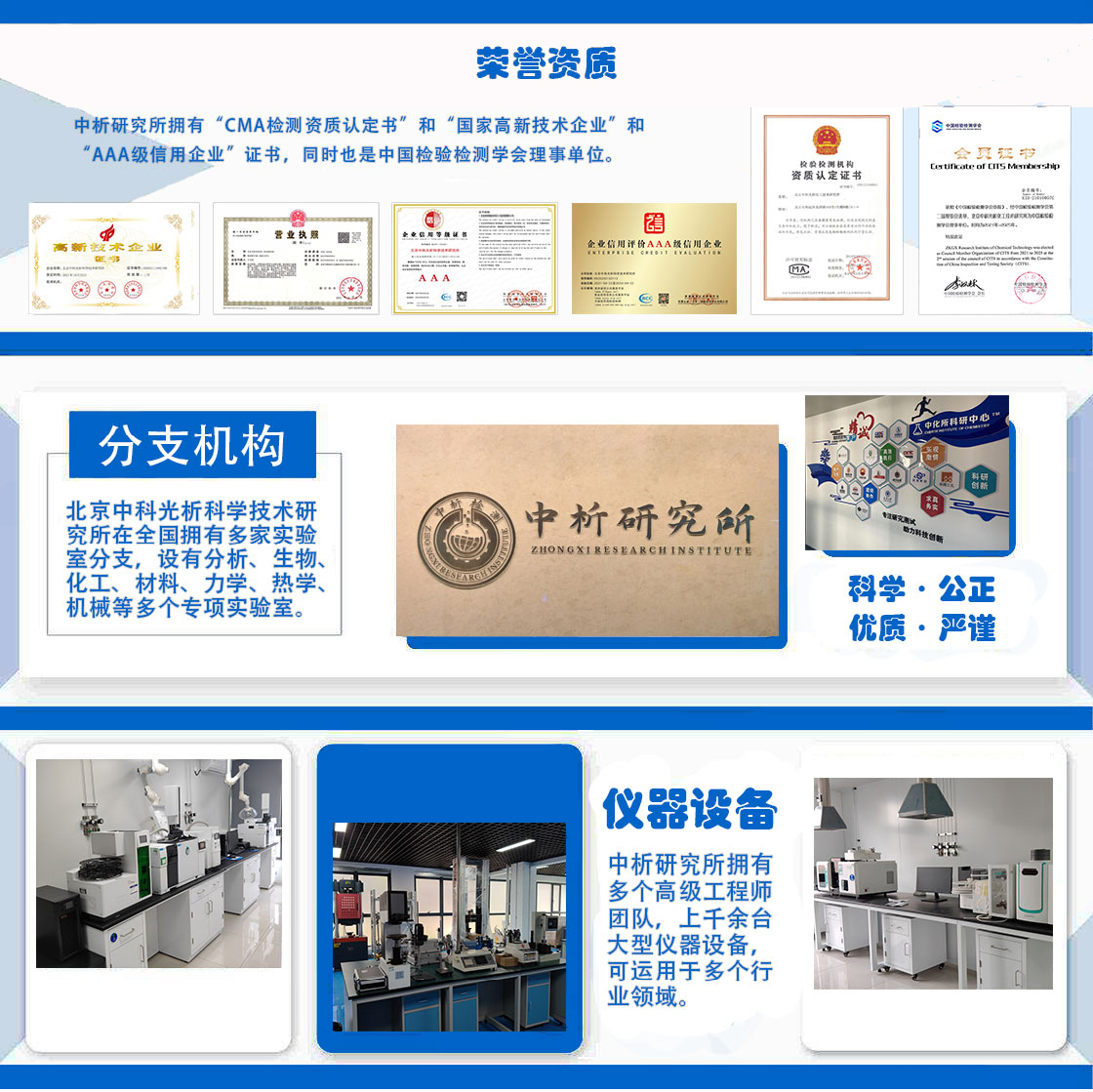
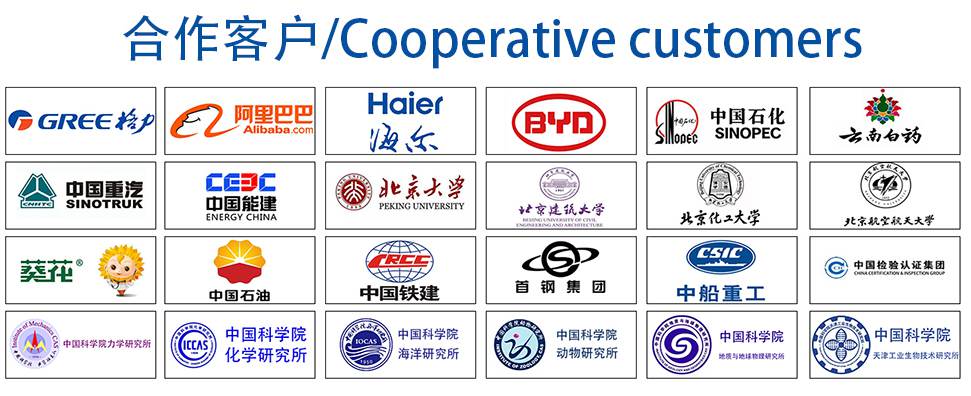