光滑工件尺寸检验检测的重要性
在机械制造领域中,光滑工件(如轴、孔、套筒等)的尺寸精度直接影响产品的装配性能和使用寿命。随着现代制造业对精度要求的不断提升,尺寸检验检测成为质量控制的核心环节。光滑工件通常具有高表面质量(Ra≤1.6μm)和严格的公差要求(IT6-IT8级),其检测需综合运用接触式与非接触式测量技术,覆盖几何参数、形位公差及表面特征等多维度指标,确保工件符合设计图纸和工艺规范。
关键检测项目及方法
1. 基本尺寸测量
包括外径、内径、长度等线性尺寸的检测。精密外径采用三点式千分尺或气动量仪(分辨率0.1μm),深孔内径使用电子塞规配合电感测头,长度测量则通过激光干涉仪(精度±0.5μm/m)实现。对于批量生产,常采用通止规进行快速判定。
2. 几何公差分析
重点检测圆度、圆柱度、直线度等形状公差。圆度误差通过旋转式圆度仪(配备高精度回转主轴)测量,圆柱度需在三维坐标测量机(CMM)上采集截面数据,直线度使用激光准直仪或光学平直仪检测,测量精度可达0.5μm级别。
3. 位置公差验证
对同轴度、垂直度、跳动等位置公差进行检测。三坐标测量机(配φ1mm红宝石测针)可完成复合位置度的数字化分析,专用芯轴配合千分表常用于现场同轴度快速检测,垂直度检测则需借助精密直角尺和光隙法。
4. 表面微观特征检测
表面粗糙度采用触针式轮廓仪(取样长度0.8mm)测量Ra/Rz值,波纹度检测需使用长行程轮廓仪(滤波波长2.5mm)。最新白光干涉仪可实现三维表面形貌重构,分辨率达纳米级,能同步分析纹理方向和加工缺陷。
5. 功能性综合检测
对配合件的实际装配效果进行验证,如液压阀芯的配磨间隙检测采用气密性试验台(压力灵敏度0.01MPa),轴承配合采用动态扭矩测试仪,模拟实际工况下的摩擦性能,确保尺寸链闭合精度。
质量控制与数据处理
现代检测系统集成SPC统计过程控制,通过MINITAB软件进行过程能力指数(CPK≥1.33)分析。检测数据自动上传MES系统,生成数字化检测报告,实现质量追溯。对于关键尺寸实施100%全检,配合X射线测厚仪等在线监测设备,构建闭环质量控制体系。
结语
光滑工件尺寸检测已从单一的尺寸判定发展为多参数、高精度的系统性质量工程。随着智能传感器和机器视觉技术的应用,检测效率提升40%以上,测量不确定度降低至微米级。企业需根据工件特性建立分级检测标准,融合计量学原理与智能制造技术,持续提升产品合格率。
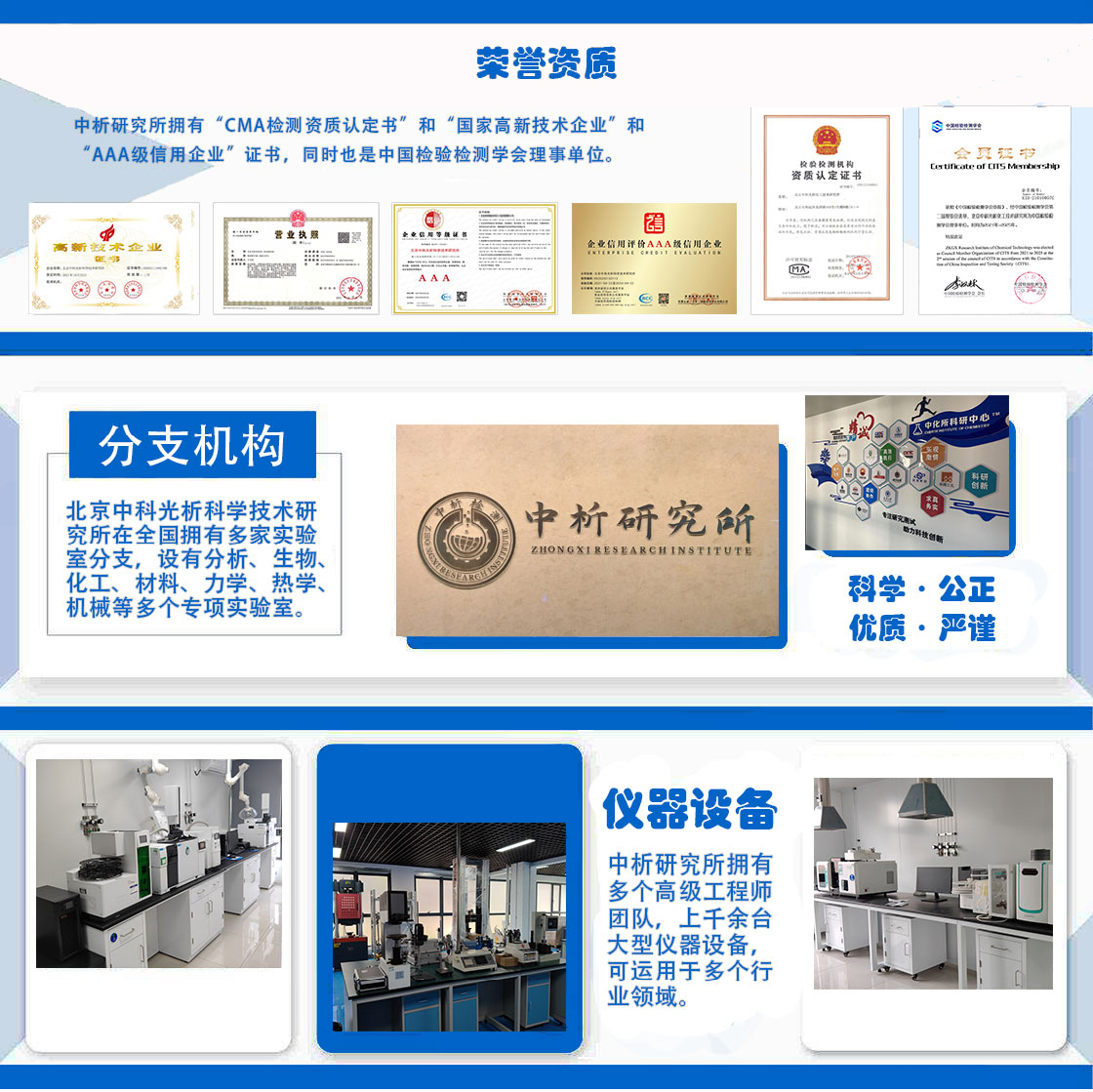
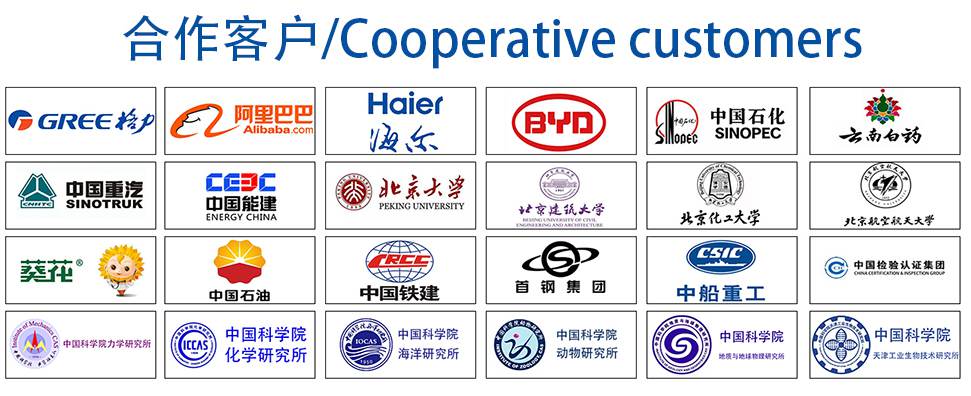