铸件性能检测的重要性与实施流程
铸件作为机械制造、汽车工业、航空航天等领域的基础零部件,其质量直接影响设备的可靠性和使用寿命。铸件性能检测是通过系统化的测试手段对材料的化学成分、物理性能、缺陷分布等核心指标进行评价的过程。随着现代工业对精密铸造要求的提升,检测项目已从传统的目视检查发展为涵盖材料科学、力学分析、无损检测技术的综合性质量管控体系。
核心检测项目与技术要求
1. 化学成分分析
采用光谱分析仪(OES)或X射线荧光光谱仪(XRF)对铸件基体材料进行元素定量检测,重点监控碳、硅、锰、硫、磷等主量元素及微量合金元素含量是否符合GB/T 223系列标准。对于高端铸件需执行ISO 4990规定的超差元素限量控制。
2. 金相组织检验
通过金相显微镜观察铸件微观组织,评估石墨形态(球化率、蠕化率)、基体结构(珠光体/铁素体比例)、晶粒度等指标。依据ASTM E3标准制备试样,配合图像分析软件实现组织定量评级,确保满足JIS G5502等材质规范要求。
3. 力学性能测试
在万能试验机上进行拉伸试验(GB/T 228.1)、冲击试验(ISO 148-1)、布氏硬度测试(ASTM E10),获取抗拉强度、屈服强度、延伸率、冲击功等关键数据。对于大型铸件可采用现场便携式硬度计进行分区硬度映射检测。
4. 无损检测技术应用
综合运用X射线探伤(ASTM E94)、超声波检测(EN 12680-1)、磁粉探伤(ISO 4986)等手段,检测铸件内部气孔、缩松、裂纹等缺陷。引入工业CT扫描可实现三维缺陷重构,检出精度可达Φ0.3mm当量缺陷。
5. 尺寸与几何公差检测
使用三坐标测量机(CMM)依据GD&T标准进行尺寸链分析,配合激光扫描仪获取铸件三维点云数据,通过Geomagic Control软件进行数模比对,确保关键配合尺寸误差控制在ISO 8062规定的CT8-CT10精度等级范围内。
检测结果分析与质量改进
建立检测数据库进行SPC统计过程控制,对超标数据启动8D问题分析流程。通过DOE实验设计优化浇注系统,结合MAGMAsoft铸造仿真软件预测缺陷位置,形成从检测到工艺改进的闭环质量管理体系,持续提升铸件良品率。
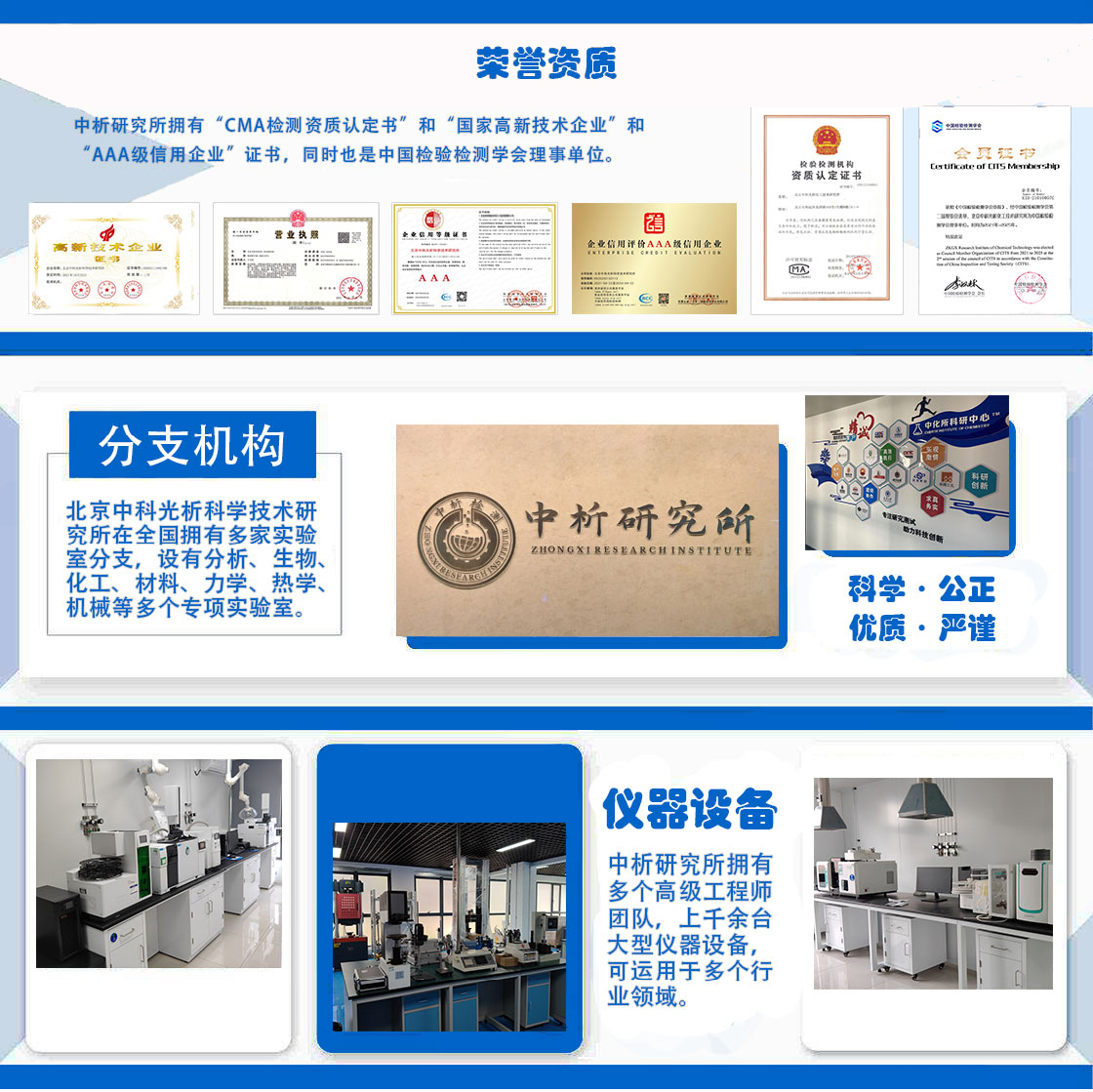
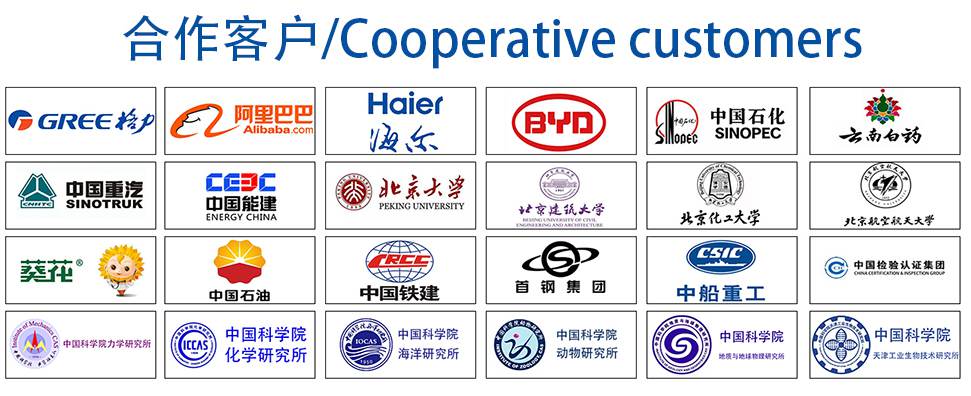