产品几何技术规范(GPS) 表面结构检测的重要性
在制造业中,产品表面结构的质量直接影响其功能性、耐久性和美观性。根据ISO 1302和ISO 4287等国际标准,产品几何技术规范(GPS)通过轮廓法对表面结构进行系统化评定,为精密零部件的设计、加工和检测提供了科学依据。表面结构的评定不仅涉及粗糙度、波纹度等微观形貌特征,还需结合轮廓曲线的数学分析,以全面评估产品性能是否符合设计要求。检测过程中需严格遵循标准化规则和方法,确保数据的一致性和可比性,这对提升产品质量、降低生产成本具有重要意义。
表面结构轮廓法的主要检测项目
基于GPS标准,表面结构的轮廓法检测主要包括以下核心项目:
1. 表面粗糙度(Roughness)参数检测
粗糙度是评价表面微观不平度的核心指标,常用参数包括Ra(算术平均偏差)、Rz(最大高度)、Rq(均方根偏差)等。检测时需使用接触式轮廓仪或光学干涉仪,沿垂直于加工纹理的方向采集数据,排除波纹度的影响。根据ISO 4288,需选择至少5个采样长度并计算平均值,确保结果的代表性。
2. 波纹度(Waviness)分析
波纹度反映了介于粗糙度和宏观形状误差之间的周期性起伏,通常由加工系统振动或刀具磨损引起。检测需采用长波滤波技术(截止波长0.8mm-8mm),分离出波纹度轮廓,并计算Wa、Wz等参数。根据应用场景(如密封件或轴承),需结合ISO 12085标准设定允许阈值。
3. 轮廓形状偏差评定
通过对比实测轮廓与理论轮廓(如直线、圆弧或复杂曲面)的差异,评估工件的形状精度。检测中需使用高精度坐标测量机(CMM)或激光扫描仪,按ISO 12180进行数据拟合,量化计算直线度、圆度、圆柱度等形状公差。
4. 表面缺陷与纹理方向检测
包括划痕、凹坑、毛刺等局部缺陷的识别,以及加工纹理方向(如磨削、车削痕迹)的定性分析。需结合目视检查、电子显微镜或3D轮廓成像技术,依据ISO 8785标准对缺陷进行分级,并评估其对摩擦、润滑等功能的影响。
5. 滤波与基准线处理
根据ISO 16610系列标准,采用高斯滤波或样条滤波消除测量噪声,并确定基准线(中线)用于参数计算。滤波截止波长(λc)的选择需与表面功能特性匹配,例如对接触密封面选用较短的λc(0.25mm),而对光学元件可能要求更精细的滤波分析。
检测方法与设备要求
现代表面结构检测广泛使用触针式轮廓仪、白光干涉仪和共聚焦显微镜等高精度仪器。设备需定期校准(符合ISO 25178-70),测量力控制在0.75mN-1mN范围内,触针半径不超过2μm。数据采集时需考虑扫描速度、采样间距(建议为0.5μm-5μm)及环境振动因素,确保重复性误差小于5%。
结论
通过GPS标准化的表面结构评定流程,企业可实现从设计规范到生产验证的全流程质量控制。随着智能测量技术的发展,基于AI的轮廓数据自动分析系统正在成为提升检测效率的新方向,但核心参数的定义与评定规则仍需严格遵循国际标准,以保证供应链中的技术一致性。
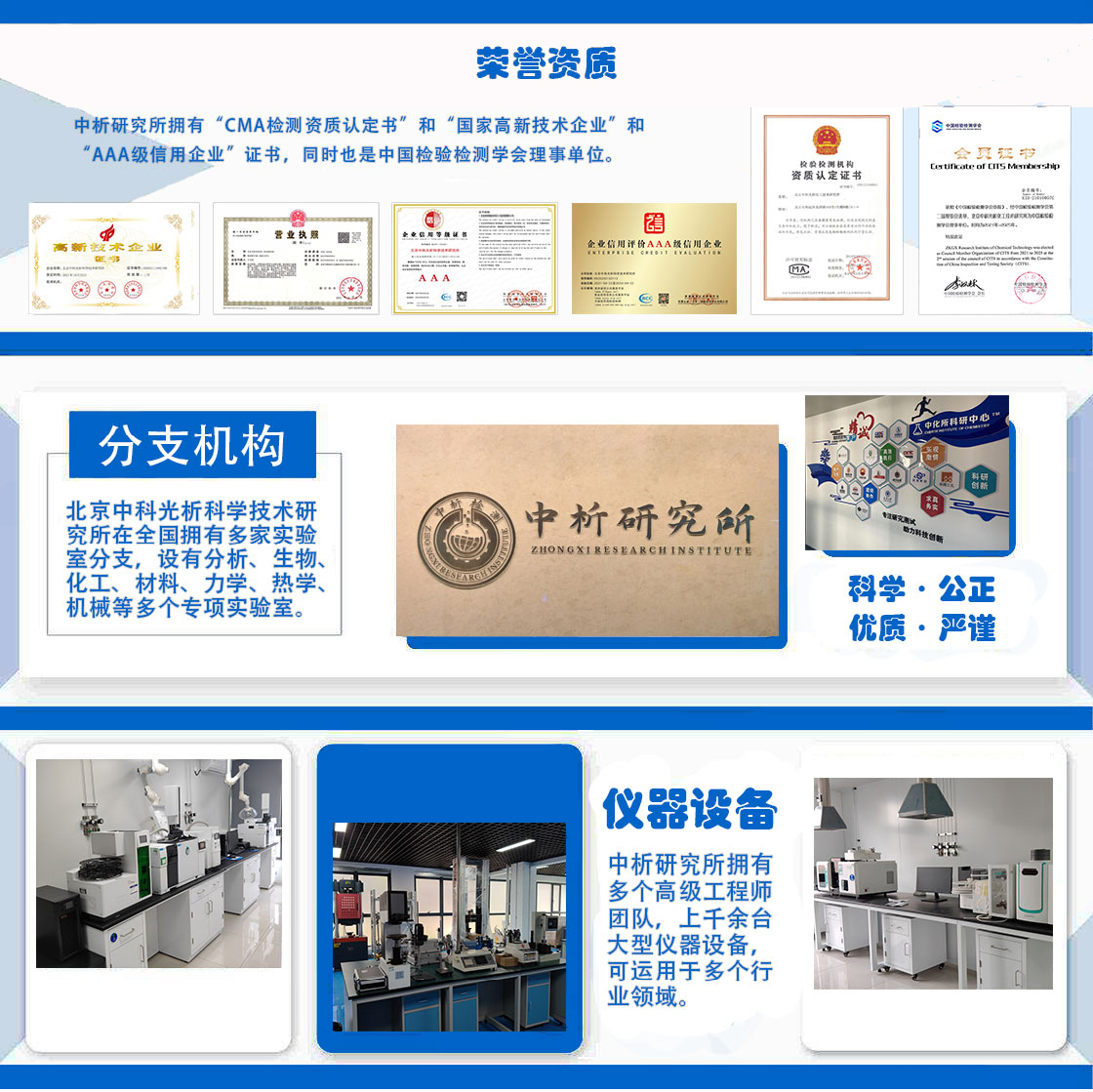
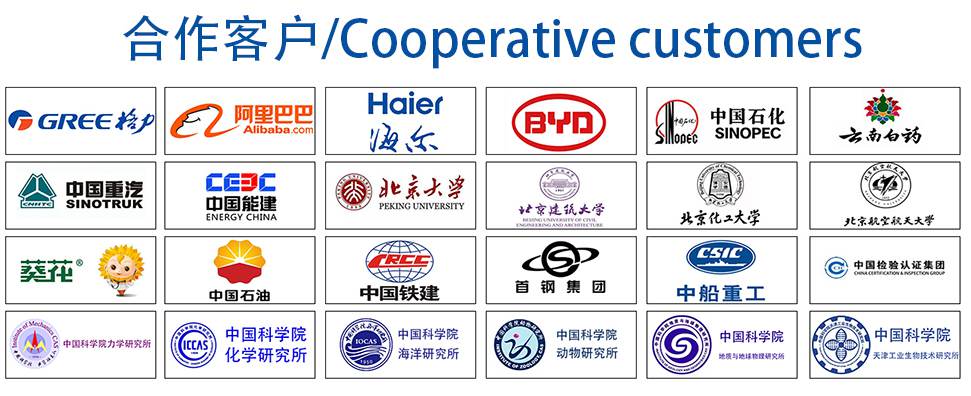