下肢假肢主结构检测的重要性
下肢假肢作为截肢患者恢复行动能力的重要辅助器具,其主结构的安全性、耐用性和功能性直接关系到使用者的生活质量和健康安全。随着材料科学与生物力学的发展,现代假肢从传统机械结构向智能化、仿生化方向升级,但无论技术如何革新,主结构的性能检测始终是产品质量控制的核心环节。通过系统化的检测流程,可验证假肢的承重能力、抗疲劳特性、材料稳定性以及运动适配性,确保产品满足国际标准(如ISO 10328)和临床使用需求。
核心检测项目及技术要点
1. 静力性能测试
通过万能材料试验机对假肢主结构(包括承重杆、关节连接件等)施加垂直负荷,验证其在极限负重下的形变率和断裂阈值。检测需覆盖轴向压缩、三点弯曲及扭转三种受力模式,模拟人体行走、跑步及意外冲击场景。例如,膝上假肢需承受至少体重的5倍静载荷而不发生永久性变形。
2. 动态疲劳测试
采用伺服液压系统模拟步行循环(通常设定50万次以上),监测假肢在重复载荷下的性能衰减。重点检测踝关节弹性元件、膝关节铰链等运动部件的磨损量,并通过高速摄像记录运动轨迹偏差。最新测试设备可同步采集压力分布数据,评估能量回馈效率是否符合人体工学要求。
3. 材料成分分析
使用X射线荧光光谱仪(XRF)和红外光谱仪(FTIR)对碳纤维复合材料、钛合金等主材进行元素检测,确保无重金属析出风险。同时通过加速老化实验验证材料的耐候性,包括湿热循环(温度85℃/湿度85%)和紫外线辐照测试,评估材料抗脆化、抗褪色能力。
4. 适配性评估体系
基于三维动态捕捉系统(VICON)和压力传感阵列,量化假肢与残肢接受腔的匹配度。检测项目包括:接受腔边缘压力分布(需<25kPa)、步态周期中矢状面角度偏差(应<5°)、以及坐姿/站立姿态切换时的稳定性。智能假肢还需验证传感器响应延迟是否低于50ms。
5. 安全防护检测
针对可能失效的机械结构设置冗余保护机制测试,例如膝关节锁死装置需在150N·m扭矩下保持稳定,防滑脚底模块需通过倾斜30°的湿滑表面测试。对于电子驱动假肢,还需进行EMC电磁兼容测试和IP67级防水验证。
检测标准的演进方向
随着3D打印定制假肢和神经控制技术的普及,检测体系正从单一物理性能评估转向"生物-机械-电子"多维验证。未来将更注重个性化适配参数的动态检测,以及长期使用中的生物相容性追踪,通过大数据分析建立更精准的假肢失效预警模型,为行业发展提供技术支撑。
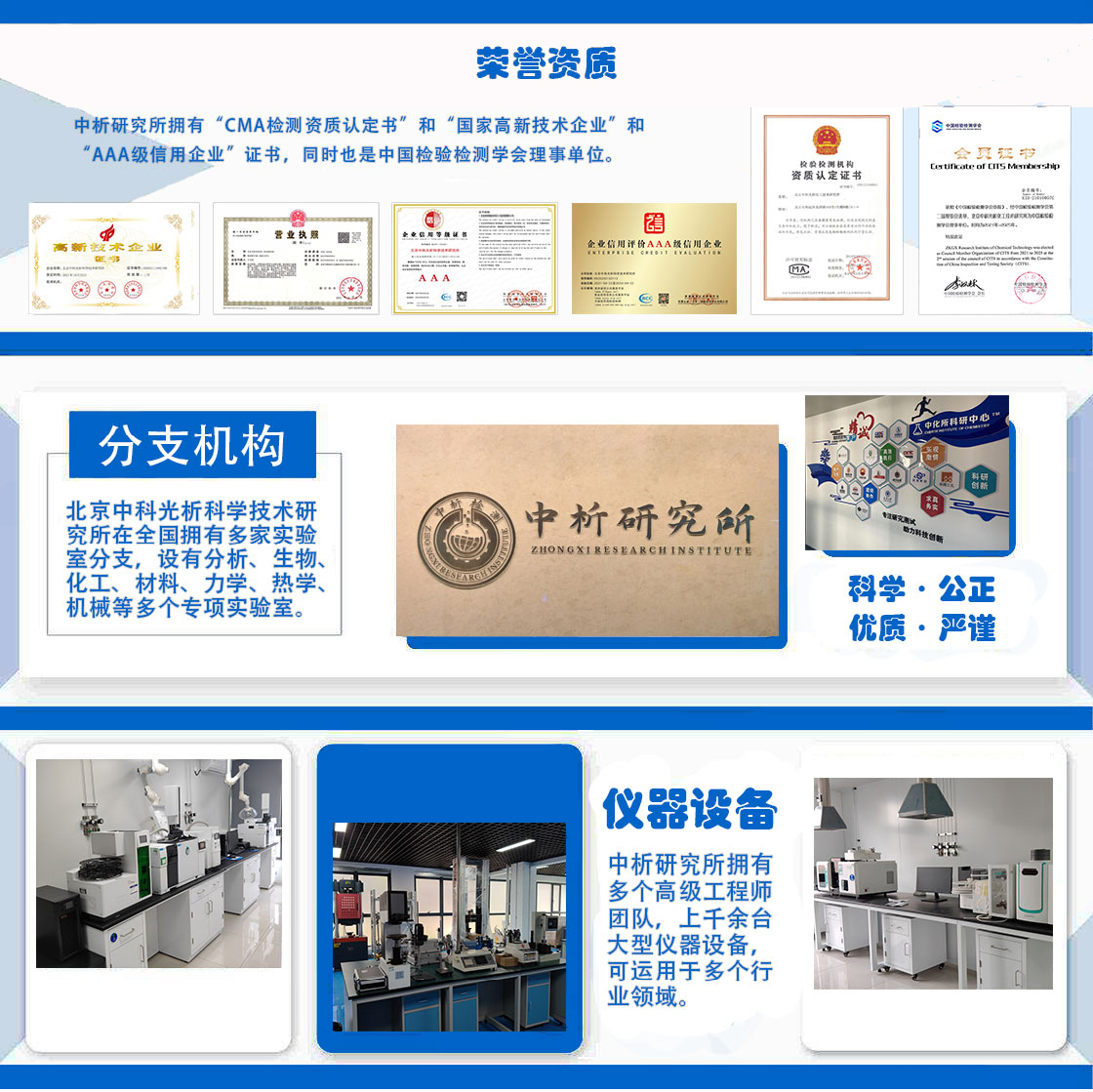
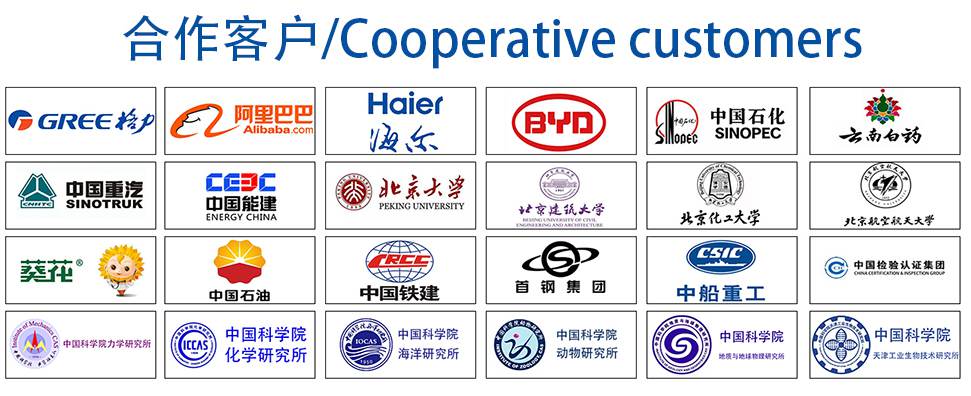