拖拉机传动箱检测的重要性与必要性
作为拖拉机动力传输系统的核心部件,传动箱承担着传递发动机扭矩、调节转速和改变行驶方向的关键作用。其工作环境常年承受高负荷、频繁换挡及复杂工况的冲击,内部齿轮、轴承、油封等零部件的磨损与老化问题尤为突出。据统计,农机故障中约35%与传动系统异常相关,其中传动箱问题占比超过60%。定期开展系统性检测不仅能延长设备使用寿命,还可避免因突发故障导致的作业中断,显著降低维修成本,同时保障操作者安全。尤其在春耕秋收等农忙季节前,专业的传动箱检测已成为现代农业机械维护的标准化流程。
核心检测项目及实施方法
1. 外观与密封性检测
采用目视检查法对传动箱壳体进行全面排查,重点观察结合面是否存在油渍、裂纹或变形。使用塞尺测量箱体接合面间隙(标准值≤0.1mm),同时通过荧光渗透检测法定位微裂纹。对通气阀进行功能性测试时,须确保其能在0.03-0.05MPa压力下正常开启。
2. 齿轮组啮合检测
运用齿轮测量仪测定齿面磨损量,当渐开线齿形误差超过0.08mm或齿侧间隙大于0.3mm时必须更换。通过磁粉探伤检查齿根是否有疲劳裂纹,配合振动频谱分析仪捕捉异常频率(200-800Hz区间的突变峰值得重点关注)。
3. 轴承运行状态评估
采用红外热像仪监测轴承工作温度,正常范围应保持在45-65℃。使用电子听诊器采集运行声响,配合加速度传感器测得振动值不应超过4.5mm/s(RMS值)。对于滚道出现点蚀面积超过10%或游隙增大0.15mm以上的轴承应及时更换。
4. 油液综合分析
严格按照SAE标准取样检测润滑油,重点关注三项指标:粘度变化率(允许±15%)、水分含量(≤0.05%)、金属磨粒浓度(铁元素<100ppm)。采用直读式铁谱仪分析磨粒形态,当出现大量片状或切削状颗粒时提示异常磨损。
5. 同步器功能性测试
在空载状态下进行档位切换测试,要求换挡力不超过150N且无打齿现象。使用角度编码器测量同步时间,各档位同步时长差异应控制在0.2秒以内。对锥面摩擦系数进行测定时,标准值需保持在0.09-0.12区间。
6. 总成密封性能验证
采用气压试验法,向箱体内注入0.15MPa压缩空气后保压10分钟,压降不得超过初始值的10%。对于迷宫式密封结构,需配合氦质谱检漏仪定位泄漏点,允许泄漏率标准为≤1×10^-5 Pa·m³/s。
智能化检测技术应用
现代检测体系已集成在线监测装置,通过安装温度、振动、油质等多参数传感器,实现实时数据采集与云端分析。基于MATLAB开发的故障诊断系统能提前30-50小时预警潜在故障,使传动箱维护从定期检修转向预测性维护,设备利用率可提升22%以上。
检测周期与标准规范
建议遵循"500小时常规检测+2000小时深度检测"的周期管理制度。检测过程需符合GB/T 15370-2018《农业拖拉机试验规程》和ISO 11684:2005标准要求,所有检测数据应建立电子档案并保存至少5个作业季,为设备全生命周期管理提供数据支撑。
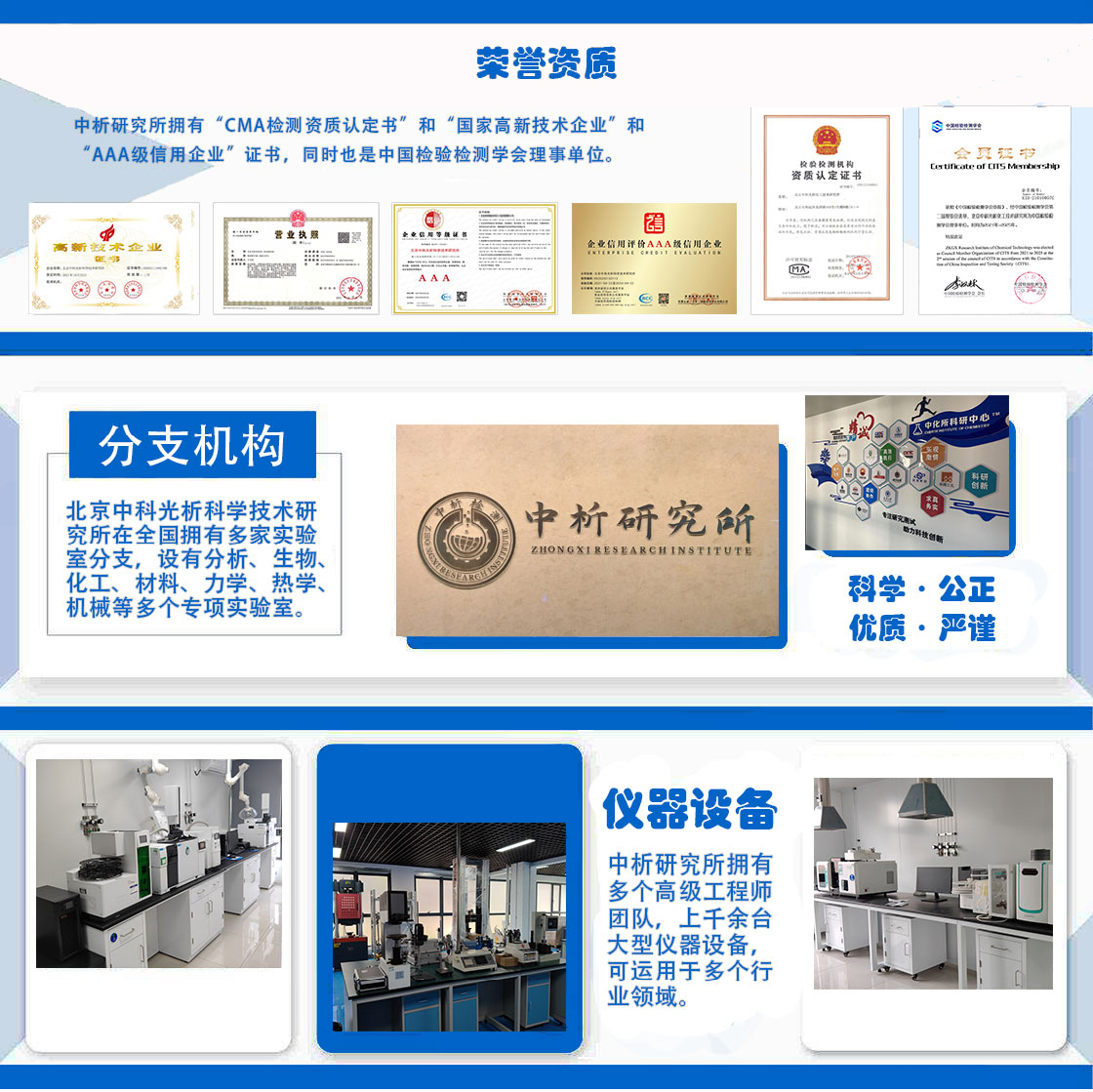
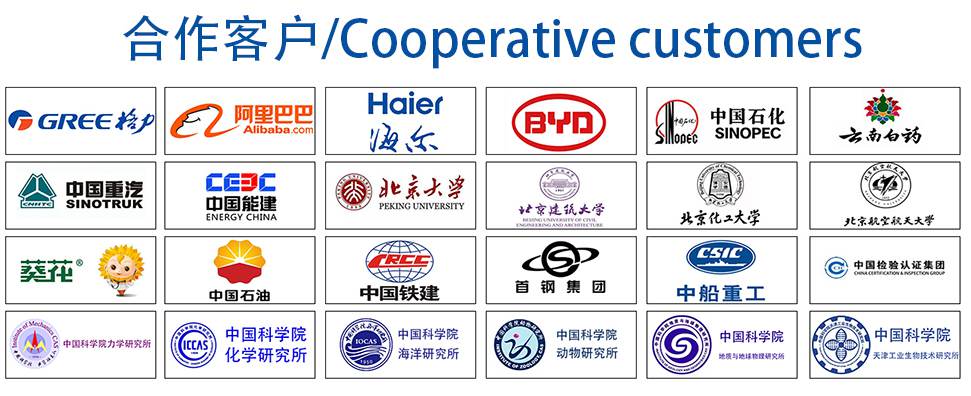